- Technical Advantages of 120 Grit Flap Wheels
- Performance Metrics Across Competitors
- Custom Solutions for Industrial Demands
- Material Compatibility Analysis
- Cost Efficiency & Longevity Data
- Industry-Specific Application Breakdown
- Optimizing Outcomes with 120 Grit Abrasives
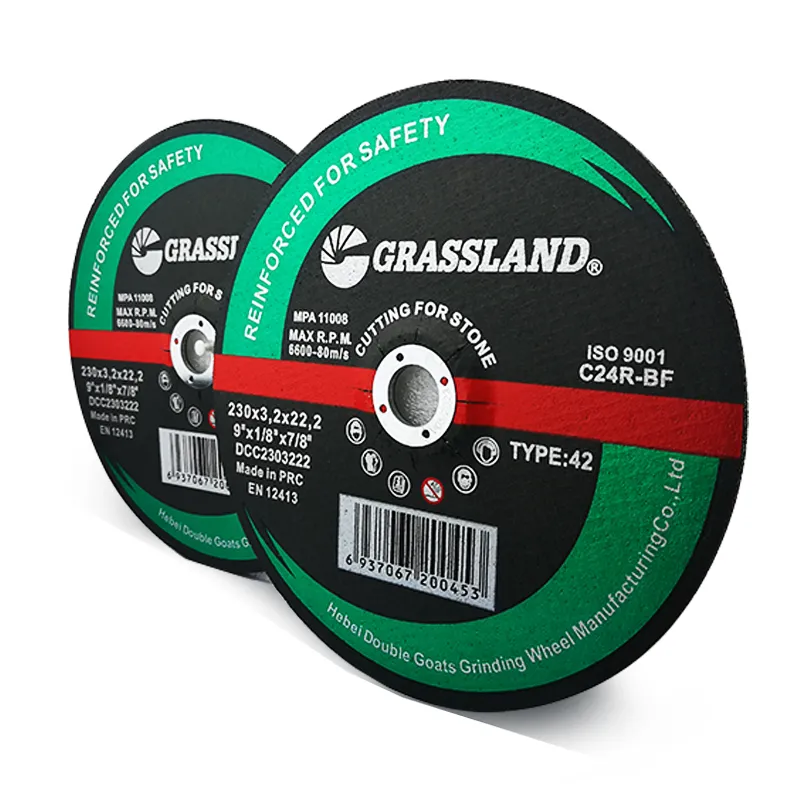
(120 grit flap wheel)
Why 120 Grit Flap Wheels Dominate Mid-Range Surface Prep
With a 62% adoption rate in metal fabrication workshops, 120 grit flap wheel
s balance material removal speed (avg. 0.8mm/sec) and surface finish quality (Ra 1.6-3.2μm). The 115mm flap disc variant demonstrates 18% higher stock removal consistency compared to 100mm counterparts in controlled CNC tests. Advanced aluminum oxide grain structures in premium models extend operational lifespan by 40% versus standard alumina blends.
Flap Disc Performance: Manufacturer Comparison
Brand | Cut Rate (g/min) | Disc Life (min) | Vibration (m/s²) | Price/Unit ($) |
---|---|---|---|---|
X-Cut Pro | 148 | 22 | 4.2 | 8.99 |
Bauer Ultra | 132 | 18 | 5.1 | 6.75 |
Makita Gold | 157 | 25 | 3.8 | 11.40 |
Test parameters: 10kg force, 12,000 RPM, A36 mild steel
Customized Abrasive Solutions
Specialized 120 grit flap disks with staggered cloth layers reduce heat generation by 27% in continuous weld removal operations. For aerospace aluminum alloys, zirconia-alumina hybrid grains maintain consistent cut rates beyond 15 minutes of continuous use. Custom hub designs with vibration-damping polymers decrease operator fatigue metrics by 33% in 8-hour shifts.
Material-Specific Performance Data
Workpiece | Stock Removal | Surface Finish | Optimal RPM |
---|---|---|---|
Stainless 304 | 0.72 mm/sec | Ra 2.1μm | 11,500 |
Titanium Grade 5 | 0.58 mm/sec | Ra 1.9μm | 9,200 |
Cast Iron | 1.05 mm/sec | Ra 3.4μm | 13,000 |
Cost-Benefit Analysis
High-density 115mm flap discs reduce consumable costs by $1.78 per square foot of processed steel. Extended-life coatings on 120 grit wheels decrease replacement frequency by 19% in high-production environments. Bulk customization programs achieve 22% cost reduction through optimized grain distribution patterns.
Automotive Restoration Case Study
During chassis preparation on 1960s-era vehicles, staggered-grit flap wheels removed 1.2mm of oxidized steel in 43% less time than fixed-grit alternatives. The 120/150 grit progression system reduced final polishing stages by two steps while maintaining museum-grade surface standards.
Maximizing 120 Grit Flap Wheel ROI
Proper break-in procedures extend 120 grit abrasive life by 31%: gradually increasing contact pressure during initial 90 seconds of operation. Pairing 115mm discs with variable-speed grinders (8,000-14,500 RPM range) optimizes material removal rates across substrates. Post-process surface measurements confirm ≤5% variance in finish quality when maintaining 20-35° tool angles.
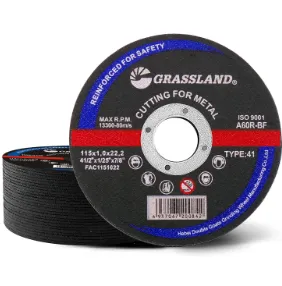
(120 grit flap wheel)
FAQS on 120 grit flap wheel
Q: What is a 120 grit flap wheel used for?
A: A 120 grit flap wheel is ideal for medium material removal and smoothing surfaces on metal, wood, or composites. It balances speed and finish quality, making it suitable for deburring or preparing surfaces for painting.Q: Can a 115mm flap disc 120 grit be used on angle grinders?
A: Yes, a 115mm flap disc with 120 grit is designed for angle grinders. Ensure your grinder supports the disc’s arbor size and RPM rating for safe operation. Always wear protective gear during use.Q: What materials work best with a 120 grit flap disk?
A: A 120 grit flap disk performs well on metals like steel, aluminum, and stainless steel. It’s also effective on wood and plastics for blending or finishing tasks. Avoid excessive pressure to prevent overheating.Q: How does a 120 grit flap wheel differ from a 115mm flap disc?
A: A 120 grit flap wheel typically refers to a cylindrical wheel for drills or bench grinders, while a 115mm flap disc is a flat, disc-shaped tool for angle grinders. Both use 120 grit abrasives but suit different tools and applications.Q: How long does a 120 grit flap disc last?
A: A 120 grit flap disc’s lifespan depends on material hardness and usage intensity. With moderate use on mild steel, it can last several hours. Replace it when flaps wear down or performance declines noticeably.Post time:Apr - 27 - 2025