The Versatility of 120% Flap Discs in Metalworking
In the realm of metalworking, the choice of abrasive tools can significantly impact the quality and efficiency of projects. One such tool that has gained considerable popularity is the flap disc, particularly the 120% flap disc. These discs combine the advantages of both grinding wheels and traditional sanding discs, making them a favorite among professionals and hobbyists alike.
Understanding Flap Discs
Flap discs are made by attaching multiple overlapping layers or flaps of abrasive material to a backing disc. This design not only allows for efficient grinding and finishing but also offers a longer lifespan than conventional abrasive wheels. The flaps wear down as they are used, exposing fresh abrasive material and maintaining cutting performance throughout their lifespan.
The Advantage of 120% Flap Discs
One of the most striking features of 120% flap discs is their ability to operate at a greater level of efficiency and adaptability, enabling users to achieve a broader range of finishes. The term 120% refers to the grit size typically associated with these discs, meaning they provide a balance between aggressive material removal and fine finishing.
Applications in Metalworking
The 120% flap disc is particularly effective in various metalworking tasks. It excels in welding clean-up, where the goal is to remove weld seams and prepare surfaces for further treatment. The versatility of the flap disc allows it to navigate both flat and contoured surfaces, making it ideal for intricate designs.
120 flap disc
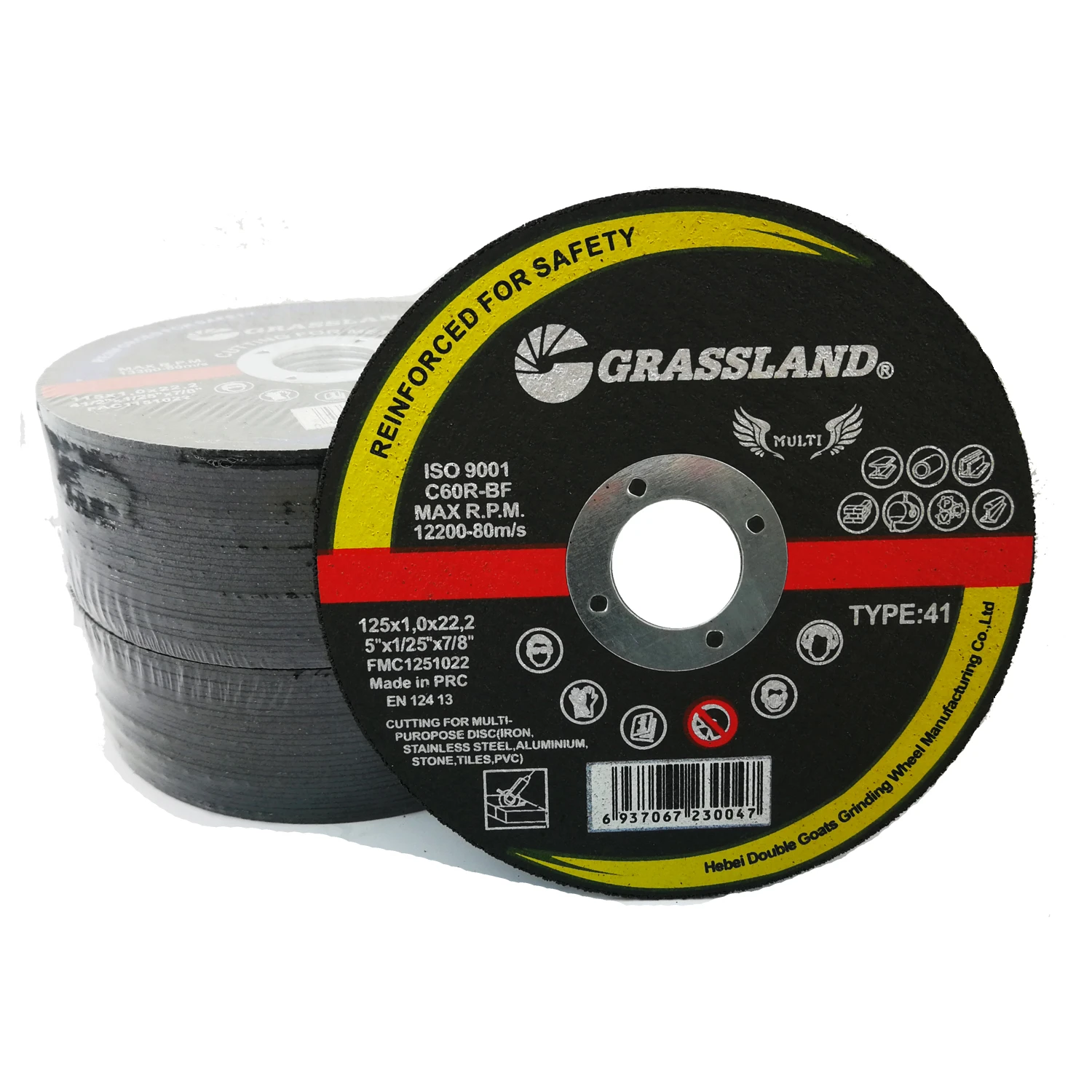
Additionally, the 120% flap disc is excellent for surface preparation prior to painting or coating. Achieving the right surface texture is crucial for the adhesion of paints and protective coatings, and the robust nature of these discs makes them perfect for this application. By providing a consistent finish and removing oxidation, flap discs improve the overall aesthetics and longevity of metal products.
Benefits Over Traditional Methods
Compared to traditional grinding wheels, 120% flap discs offer several benefits. The reduced heat generation during operation minimizes the risk of warping or damaging the metal surface. This is crucial when working with thin materials or components that require precise tolerances. Furthermore, the flexibility of the flaps allows the discs to adapt to different surfaces, reducing the need for multiple tools in the workshop.
Choosing the Right Flap Disc
When selecting a flap disc, it is essential to consider the material being worked on, the type of finish required, and the specific application. For instance, stainless steel may require a different abrasive composition compared to carbon steel. Understanding the grit size and the disc's density is also vital in determining its effectiveness.
Conclusion
In conclusion, the 120% flap disc represents a significant advancement in the field of abrasive tools. Its versatility, efficiency, and ability to achieve superior finishes have made it an indispensable tool in metalworking. Whether you are a seasoned professional or an enthusiastic amateur, investing in high-quality flap discs can enhance your projects’ overall quality and bring your metalworking skills to new heights. As the industry continues to evolve, tools like the 120% flap disc will undoubtedly play a crucial role in shaping the future of metal fabrication and repair.
Post time:Nov - 17 - 2024