Understanding the Role of 120% Grit Flap Disks in Metalworking
In the world of metalworking and fabrication, the choice of abrasive tools is crucial for achieving the desired surface finish and material removal rate. One of the most popular tools in this category is the flap disk, particularly those with a 120 grit rating. This article delves into the features, applications, and advantages of using a 120 grit flap disk, helping metalworkers understand why this tool is indispensable in various projects.
What is a Flap Disk?
A flap disk consists of overlapping segments, or “flaps,” of abrasive material that are attached to a backing plate. The design allows for flexibility and adaptability to the contours of the workpiece, making flap disks different from traditional grinding wheels. The abrasive material used can vary from aluminum oxide and zirconia to ceramic, each providing unique properties suited for different applications.
The Significance of Grit Size
Grit size is a measure of the coarseness or fineness of the abrasive material. In the case of a 120 grit flap disk, this indicates a medium-grade abrasive, striking a balance between removing material quickly and achieving a smooth finish. A 120 grit disk is typically used for blending, finishing, and light grinding tasks on various metals, such as steel, aluminum, and stainless steel.
Applications of 120 Grit Flap Disks
1. Surface Preparation Before applying coatings or paint, it is essential to prepare the surface adequately. A 120 grit flap disk can effectively clean and smooth out surfaces, removing rust, scale, and old paint while ensuring a surface that adheres well to the new materials.
2. Welding Operations In welding, preparing the edges of the metal pieces before joining them is critical. A 120 grit flap disk can grind and bevel the edges, ensuring better fusion during the welding process. After welding, these disks can also be utilized to grind down welds for a smoother appearance.
120 grit flap disk
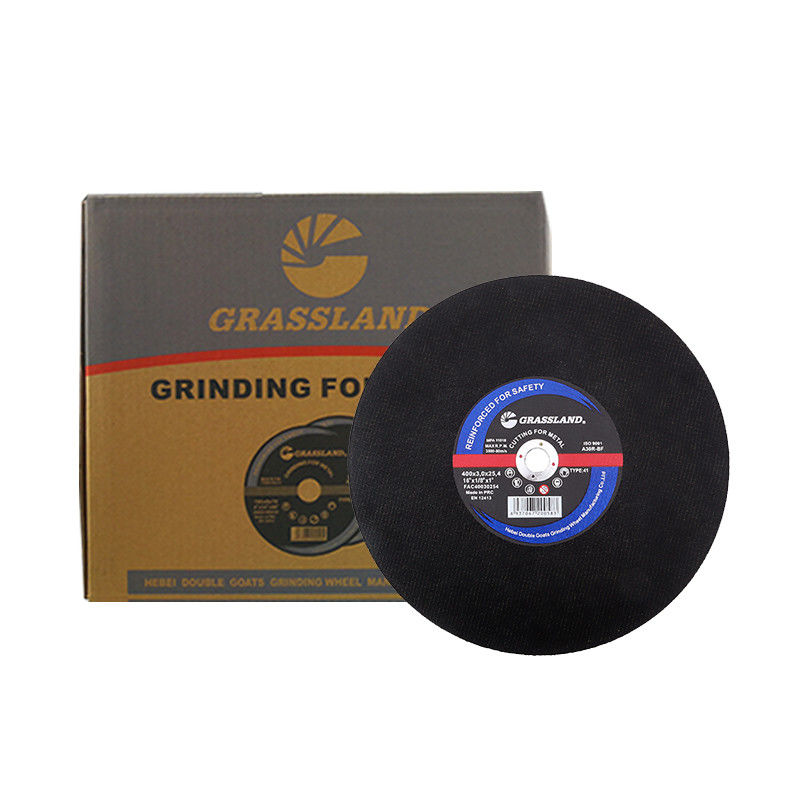
3. Deburring The process of deburring involves removing sharp edges or small imperfections from machined parts. Using a 120 grit flap disk helps in achieving a smooth finish without significantly altering the dimensions of the workpiece.
4. Finishing For projects requiring an aesthetically pleasing final appearance, a 120 grit flap disk serves as an excellent finishing tool. It ensures that the surface has a uniform texture, ready for polishing or further refinement.
Advantages of Using 120 Grit Flap Disks
1. Versatility Flap disks can be used on various materials, making them a versatile choice for metalworkers. Whether one is working on mild steel, stainless steel, or non-ferrous materials like aluminum, a 120 grit flap disk can deliver efficient results.
2. Enhanced Control and Precision Thanks to their unique construction, flap disks provide greater control compared to traditional grinding wheels. The flexible design allows them to conform to the contours of a workpiece, delivering a smoother and more precise finish.
3. Longer Lifespan The layered design of flap disks means that as one layer wears down, another continues to provide cutting action. This leads to a longer lifespan compared to flat grinding wheels, which wear uniformly from the surface.
4. Reduced Heat Generation Flap disks tend to generate less heat while working than traditional grinding wheels, reducing the risk of thermal damage to the workpiece and improving user safety.
In conclusion, a 120 grit flap disk is an essential tool in the metalworker's arsenal. Whether for surface preparation, grinding, or finishing, its versatility and effectiveness make it a preferred choice in numerous applications. Understanding how to utilize and select the appropriate flap disk can significantly enhance the quality of work, leading to professional results in every metalworking project. Embracing this tool ensures that craftsmen can achieve both efficiency and excellence, reflecting their skills and dedication to their craft.
Post time:Dec - 14 - 2024