Understanding the 12% Cut-Off Wheel A Critical Component in Modern Manufacturing
In the realm of manufacturing and industrial operations, cut-off wheels play an indispensable role. Among various types of cut-off wheels available, the 12% cut-off wheel has gained prominence due to its efficiency, durability, and versatility. This article aims to delve into the intricacies of the 12% cut-off wheel, its applications, advantages, and the factors to consider when selecting the appropriate one for specific tasks.
What Is a Cut-Off Wheel?
A cut-off wheel is a type of industrial tool primarily used for cutting hard materials such as metal, concrete, stone, and ceramics. Comprising a thin circular disc, these wheels are designed to be attached to a variety of power tools, including angle grinders and stationary saws. The 12% typically refers to the wheel's thickness and composition, indicating a specific formulation that offers a unique balance between abrasiveness and operational life.
Key Features of the 12% Cut-Off Wheel
1. Material Composition The 12% cut-off wheel is often made from a combination of abrasive materials like aluminum oxide or silicon carbide, depending on the application. This composition allows for effective cutting while maintaining resistance against wear and tear during prolonged use.
2. Thickness Typically, the thickness of a 12% cut-off wheel is optimized for swift cutting with minimal material loss. This feature not only enhances cutting precision but also extends the lifespan of the wheel itself.
3. Speed and Efficiency These cut-off wheels can typically handle high rotational speeds, making them suitable for both professional and DIY tasks. Their ability to cut through tough materials efficiently translates to time savings in various projects.
4. Versatility The 12% cut-off wheels can be employed across various sectors, including construction, automotive repairs, metalworking, and manufacturing. They are versatile enough to cater to different applications, from heavy-duty tasks to precision work.
Advantages of Using a 12% Cut-Off Wheel
12 cut off wheel
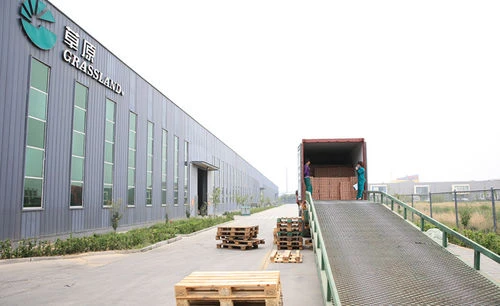
1. Enhanced Precision Due to their fine thickness and advanced material composition, 12% cut-off wheels provide cleaner cuts with reduced burrs, minimizing the need for additional finishing work.
2. Durability Engineered for longevity, these wheels are crafted to withstand the rigors of both high-load and prolonged operations. This aspect reduces the frequency of replacements, ultimately lowering operational costs.
3. Safety Modern 12% cut-off wheels are designed with safety features to withstand high speeds and heavy stresses. They often come with guidelines for proper use, ensuring operators are aware of safety protocols.
4. Cost-Effectiveness While initial costs may vary, the durability and efficiency of 12% cut-off wheels lead to long-term savings. Fewer replacements and reduced setup time can significantly impact overall project budgets.
Selecting the Right 12% Cut-Off Wheel
Choosing the proper cut-off wheel involves considering several factors
- Material Type Identify the material you are cutting. Different materials require specific wheel compositions for optimum performance. - Tool Compatibility Ensure that the wheel is compatible with your cutting tool regarding size and speed ratings. - Application Needs Consider whether precision or speed is more critical for your task, and select a wheel that aligns with those needs.
Conclusion
The 12% cut-off wheel represents a significant evolution in cutting technology, merging efficiency, durability, and safety into one package. Whether you're a professional craftsman or a DIY enthusiast, understanding the advantages and proper usage of these wheels can lead to enhanced productivity and exceptional results in your projects. Investing in quality cut-off wheels is a step toward improving your operational capabilities and achieving the best outcomes in your cutting tasks.
Post time:Dec - 11 - 2024