The Versatility and Utility of 1% 202% Flap Wheels
Flap wheels are indispensable tools in the realm of metalworking and surface finishing. Particularly, the 1% 202% flap wheel showcases a balance of efficiency and precision that is vital for achieving high-quality outcomes in various applications. This article explores the design, functionality, uses, and advantages of the 1% 202% flap wheel, shedding light on its importance in both industrial and DIY projects.
Design and Composition
The 1% 202% flap wheel is characterized by its unique construction, which consists of multiple layers of abrasive cloth or paper arranged in a radial formation. These flaps are mounted on a central spindle, allowing them to rotate and conform to the surface of the material being worked on. The 1% 202% designation typically refers to specific grit sizes and configurations that cater to different tasks, making it versatile enough for multiple applications—from heavy material removal to delicate polishing.
The abrasive material used in flap wheels can vary, with options including aluminum oxide, zirconia, and silicon carbide. Aluminum oxide, for instance, is popular for its durability and efficiency, while zirconia offers enhanced cutting speed and lifespan. The selection of abrasive material directly impacts the performance of the flap wheel, making it crucial to choose the right type based on the specific requirements of the job at hand.
Functionality and Application
Flap wheels are primarily used for grinding, deburring, and finishing metal surfaces. Thanks to their flexibility, they can reach intricate shapes and contours that traditional grinding wheels may not manage. The 1% 202% flap wheel, in particular, is ideal for operations that require a blend of aggression and finesse.
1 2 flap wheel
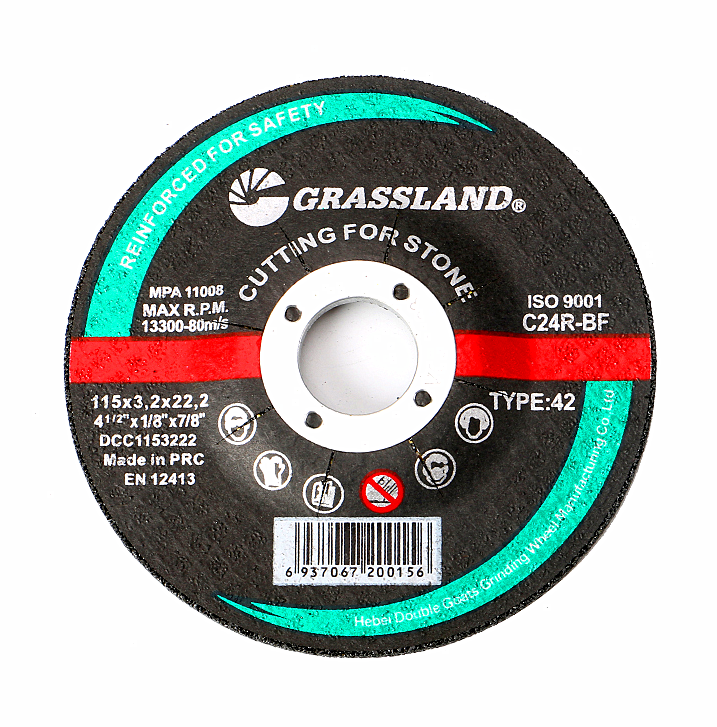
One of the most common applications of flap wheels is in the automotive industry for refining metal parts and components. From smoothing the surfaces of welded joints to perfecting intricate details on machine parts, the 1% 202% flap wheel excels at eliminating rough edges while leaving behind a fine finish. Similarly, in woodworking, these wheels can be employed to remove material and create a smooth, polished surface on hardwoods and composite materials.
Moreover, flap wheels are invaluable in the maintenance and repair sectors. By using a 1% 202% flap wheel, technicians can quickly buff out surface abrasions caused by wear and tear, ensuring that tools and machinery remain in optimal condition. This not only extends the life of equipment but also enhances safety by preventing potential failures caused by damaged surfaces.
Advantages of Using Flap Wheels
The benefits of using 1% 202% flap wheels extend beyond their versatility and precision. One significant advantage is their ability to reduce heat generation during operation. Unlike traditional grinding wheels, flap wheels disperse heat more evenly, minimizing the risk of damaging the workpiece. This is particularly crucial when working with heat-sensitive materials.
Additionally, flap wheels offer a longer lifespan compared to conventional grinding tools. Their layered design allows for a consistent performance as the outer flaps wear down, ensuring continued effectiveness throughout their use. This not only makes flap wheels cost-effective but also reduces downtime associated with tool changes.
Conclusion
The 1% 202% flap wheel is a remarkable tool that encapsulates versatility, efficiency, and precision in surface finishing applications. Whether in automotive, metal fabrication, or woodworking, its unique design and functionality cater to a wide array of tasks. By investing in high-quality flap wheels, professionals and DIY enthusiasts can achieve superior results, ensuring that their projects not only meet but exceed expectations. As technology continues to innovate, the flap wheel remains a steadfast ally in the quest for excellence in craftsmanship and surface treatment.
Post time:Nov - 17 - 2024