The Versatility and Importance of 40% Grit Flap Wheels in Metalworking
In the realm of metalworking and finishing, the tools we use can significantly impact the quality of our work. Among these tools, flap wheels have gained recognition for their versatility and effectiveness, especially the 40% grit flap wheels. These specialized grinding and finishing tools play a crucial role in achieving desired surface finishes, deburring, and polishing a variety of materials.
Understanding Grit Grading
To grasp the importance of a 40% grit flap wheel, it is essential to understand grit grading. Grit refers to the size of the abrasive particles contained in the wheel. The grading scale ranges from very fine (higher numbers) to very coarse (lower numbers). For instance, a flap wheel rated at 40 grit features larger abrasive grains, making it suitable for more aggressive material removal. In contrast, a 240 grit wheel would provide a finer finish.
The designation of 40% grit typically indicates that the wheel’s abrasive surface is composed of 40 grit abrasive particles. This classification is particularly beneficial for tasks requiring substantial material removal while still maintaining some degree of smoothness in the finish. The balance between aggression and finesse makes the 40 grit flap wheel a go-to option for various applications.
Applications of 40% Grit Flap Wheels
1. Deburring One of the primary uses of 40% grit flap wheels is deburring metal surfaces. When machining metal parts, sharp edges and burrs can form, which may interfere with subsequent processes or the functionality of the part. The 40 grit flap wheel effectively removes these imperfections, preparing the surface for further treatment.
2. Surface Preparation Whether you’re preparing a surface for painting, coating, or welding, a clean and smooth base is essential. A 40 grit flap wheel can quickly remove rust, scale, and old paint, exposing a clean layer of metal ready for application. This is crucial in industries where surface integrity and adhesion play a significant role in the longevity of the finish.
3. Welding Seam Cleanup After welding, surfaces often require cleanup to ensure a strong and aesthetic bond. The 40% grit flap wheel excels at smoothing out weld seams, removing excess slag, and ensuring proper surface integrity. This process not only enhances the appearance of the weld but also contributes to the overall strength of the joint.
4. Polishing and Finishing While flap wheels are primarily known for their grinding capabilities, they can also be used for polishing applications. The layered design of flap wheels allows for incremental finishing, where a 40 grit wheel can be used as a precursor to finer grits, creating a smooth, polished surface.
Benefits of Using Flap Wheels
40 grit flap wheel
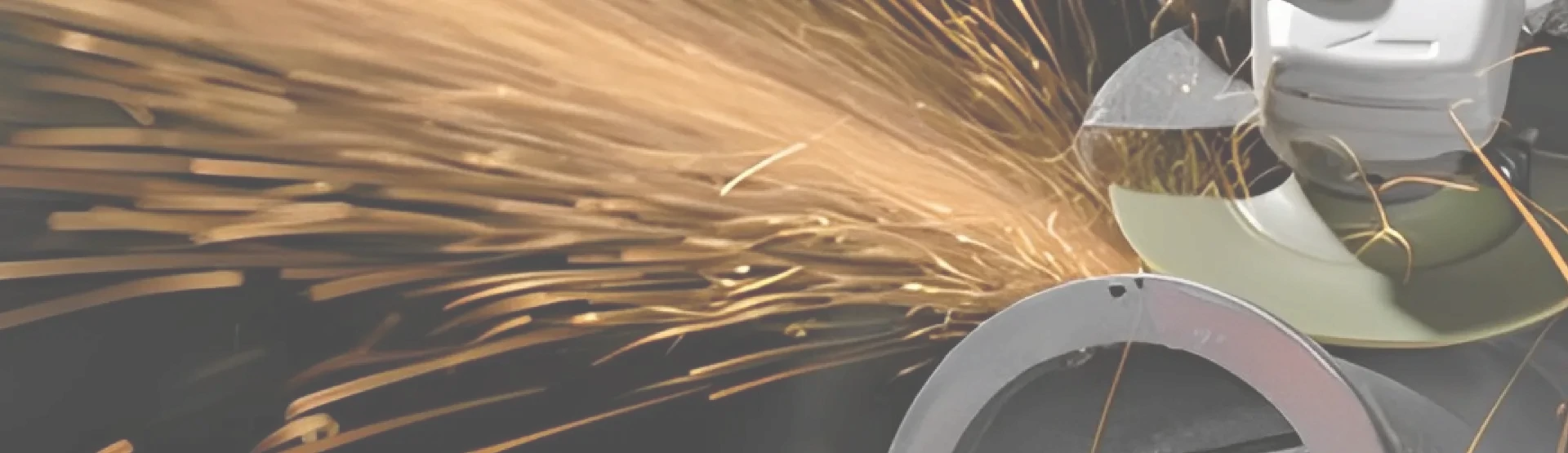
The design of flap wheels offers several distinct advantages over traditional grinding wheels. Firstly, the flexibility of the flaps allows the wheel to conform to the contours of the workpiece, providing an even finish regardless of the surface geometry. This is particularly important in industries that work with irregular shapes or delicate components.
Furthermore, flap wheels are less aggressive than standard grinding wheels, reducing the risk of damaging the workpiece. The gradual wear of the abrasive flaps means that they maintain a consistent cutting action throughout their lifespan, leading to uniform results.
Best Practices for Using 40% Grit Flap Wheels
To maximize the performance of a 40% grit flap wheel, several best practices should be considered
- Choosing the Right Speed Operating the flap wheel at the appropriate speed is vital. Too high a speed can cause overheating and damage the workpiece, while too low a speed may lead to ineffective material removal.
- Regular Inspection Regularly inspecting the wheel’s condition can help ensure optimal performance. Replace worn flaps to maintain cutting consistency and prevent irregular finishes.
- Using Appropriate Pressure Applying consistent and moderate pressure allows the wheel to work effectively without putting undue stress on the tool or the workpiece.
- Safety Precautions Always wear appropriate personal protective equipment (PPE) when working with flap wheels, as debris and particles can become airborne during operation.
Conclusion
In summary, 40% grit flap wheels are indispensable tools within the metalworking industry. Their unique design and versatile applications make them suitable for various tasks, from aggressive material removal to finishing and polishing. By understanding their capabilities and adhering to best practices, metalworkers can enhance their processes, improve the quality of their work, and achieve outstanding results. As industries continue to evolve, the significance of flap wheels in facilitating efficient and effective metalworking processes remains steadfast.
Post time:Dec - 05 - 2024