Choosing the Right 4% 201% 202% Grinding Wheel for Steel
When it comes to metalworking, particularly steel fabrication, the importance of selecting the right grinding wheel cannot be overstated. One type that has garnered attention is the 4% 201% 202% grinding wheel, a specification that indicates specific characteristics critical to effective grinding performances. Understanding the nuances of this grinding wheel can make a significant difference in productivity, surface finish quality, and longevity of tools.
Understanding Grinding Wheels
Grinding wheels are essential tools in various industrial and fabrication applications, providing the means to remove material and achieve the desired dimensions and finishes on metal surfaces. They are composed of abrasive grains that are bonded together to form a solid circular shape. The performance of a grinding wheel is influenced by its composition, grain size, bond type, and structure.
The 4% 201% 202% designation often refers to particular characteristics in grain composition, sizes, and types of bonding, tailored specifically for steel grinding tasks. The numerical specification generally includes information about the type or percentage of the abrasives used, which directly affects the efficiency and effectiveness of the grinding process.
Benefits of the 4% 201% 202% Grinding Wheel
1. Versatility The 4% 201% 202% grinding wheel has been designed to handle various types of steel, making it an excellent choice for workshops that deal with multiple steel grades. The flexibility to grind different steel types is advantageous for fabricators who want to maintain efficiency across their operations.
2. Enhanced Material Removal Rate With the right abrasive grains designed for steel, this grinding wheel can provide a high material removal rate. It delivers efficiency in operations, allowing fabricators to spend less time on grinding tasks, thus increasing productivity.
4 1 2 grinding wheel for steel
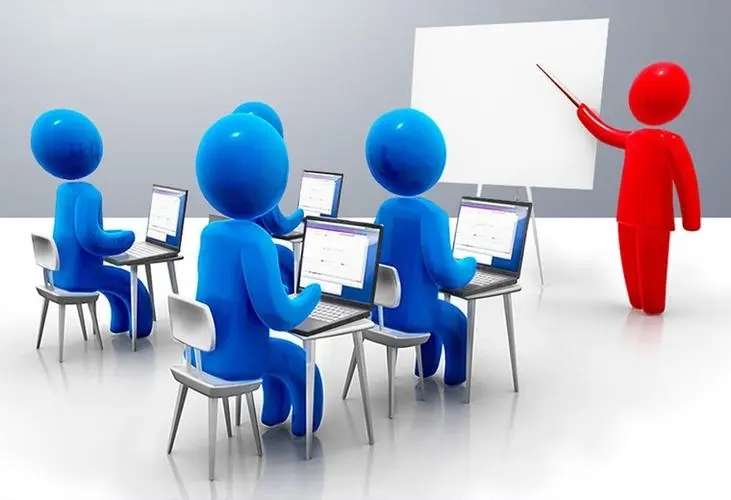
3. Consistent Finish Achieving a consistent and smooth surface finish is critical in steel fabrication. The 4% 201% 202% grinding wheel is engineered to produce a fine finish while maintaining dimensional accuracy, essential for parts requiring precise tolerances.
4. Durability One of the key factors in the grinding wheel’s design is its durability. The bonding agent and abrasive composition contribute to a longer lifespan, reducing the frequency of wheel changes and minimizing downtime in production processes.
5. Safety Considerations The structure and composition of grinding wheels can enhance safety during operation. Well-designed grinding wheels are less likely to fracture during use, reducing the risk of accidents in the workplace.
Selecting the Right Wheel for Your Needs
When choosing a grinding wheel, it’s essential to consider factors such as the type of steel you’ll be working with, the desired finish, and the specific grinding process. It’s also vital to ensure that the wheel is compatible with your grinding machine. Utilizing the manufacturer’s guidelines and recommendations will help in selecting the most appropriate wheel.
Conclusion
In conclusion, the 4% 201% 202% grinding wheel designed for steel represents a step forward in grinding technology, combining efficiency with precision. By understanding the benefits and specifications of these grinding wheels, metal fabricators can enhance their workflow, improve product quality, and ensure a safer working environment. Investing in the right grinding wheel is not just about meeting today’s demands; it’s about paving the way for a productive and efficient future in steel fabrication. As always, it’s prudent to conduct thorough research or consult with experts to find the ideal grinding wheel that aligns with your specific needs and applications.
Post time:Nov - 27 - 2024