Understanding 4% 201% 202% Metal Grinding Wheels
When it comes to metalworking and fabrication, the choice of tools and materials can significantly impact efficiency and the quality of the finished product. One of the essential tools in this regard is the grinding wheel, especially the 4%, 201%, and 202% metal grinding wheels, which have become indispensable in various industries such as automotive, aerospace, and general manufacturing. This article explores the characteristics, applications, and benefits of these specific grinding wheels.
What Are Metal Grinding Wheels?
Metal grinding wheels are abrasive tools used for various applications, including grinding, cutting, and shaping metals. Typically composed of a mixture of abrasive materials bound together, they come in various shapes, sizes, and grit specifications to accommodate different tasks and materials. The numbers 4%, 201%, and 202% refer to specific formulations or characteristics of these grinding wheels, indicating their composition and performance attributes.
The Importance of Composition
The composition of metal grinding wheels directly influences their performance. For instance, a grinding wheel designated as 4% may indicate a specific hardness and blend of abrasives designed for various metal types. Similarly, the 201% and 202% wheels signify different abrasive components or bonding methods, aimed at maximizing efficiency and lifespan while offering precise control over the grinding process.
- 4% Grinding Wheels These wheels are typically suited for general-purpose grinding. Their balanced composition allows for both aggressive material removal and a fine finish, making them ideal for a range of applications in metal fabrication.
- 201% Grinding Wheels The 201% wheels often contain a higher percentage of premium abrasives, providing durability and longer life. These wheels are ideal for industrial applications where sustainability and cost-effectiveness are critical.
- 202% Grinding Wheels On the other hand, the 202% wheels may incorporate advanced technologies or specific bonding agents that enhance performance in specialized tasks, such as surface grinding or finishing metal components with high precision.
Applications Across Industries
The versatility of the 4%, 201%, and 202% metal grinding wheels allows them to be employed in various sectors, including
4 1 2 metal grinding wheels
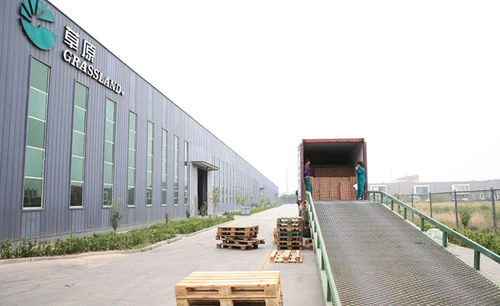
2. Aerospace Sector The aerospace industry demands high precision and quality, making specialized grinding wheels like the 201% and 202% crucial for manufacturing components that meet strict safety and performance standards.
3. Metal Fabrication In general metalworking, these grinding wheels are used for tasks ranging from deburring and stock removal to achieving fine finishes on critical components.
Benefits of Using Quality Grinding Wheels
Using high-quality grinding wheels can provide numerous benefits
- Efficiency Properly selected grinding wheels allow for faster material removal while controlling the heat generated during grinding. This efficiency translates into shorter cycle times and improved productivity.
- Surface Finish The right wheel ensures a superior surface finish, which is critical in applications where aesthetics and functionality depend on smooth surfaces.
- Cost-Effectiveness Investing in durable grinding wheels reduces frequent replacements and maintenance costs, making them a wise investment for any metalworking operation.
Conclusion
In conclusion, the 4%, 201%, and 202% metal grinding wheels represent a diverse range of products tailored for specific applications in metalworking. By understanding their unique compositions and functionalities, manufacturers and craftsmen can choose the appropriate grinding wheel type to achieve optimal results. Quality grinding wheels not only improve operational efficiency but also enhance the overall quality of metal components, making them invaluable tools in the metalworking industry.
Post time:Nov - 18 - 2024