Understanding the Importance of 5% Cut-Off Wheel in Industrial Applications
In the realm of manufacturing and metalworking, the tools and equipment utilized significantly influence the quality and efficiency of production processes. Among these tools, cut-off wheels play a crucial role in various applications, ranging from metal fabrication to construction. The term 5% cut-off wheel refers to a specific design or classification of cut-off wheels that maintains a performance threshold, embodying a blend of durability, efficiency, and precision. This article delves into the characteristics, advantages, and applications of the 5% cut-off wheel in industrial settings.
What is a Cut-Off Wheel?
A cut-off wheel, also known as a cutting disc, is a type of grinding wheel designed for cutting metal and other hard materials. These wheels are typically used in power tools, such as angle grinders and chop saws. Cut-off wheels are made from a variety of materials, including aluminum oxide, silicon carbide, and diamond, depending on their intended use.
The 5% designation usually denotes a range of performance criteria, indicating that the wheel maintains its cutting ability while operating under specific conditions without exceeding a maximum of a 5% wear rate during its lifecycle. This feature is particularly important in industrial environments, where tool longevity and cost-effectiveness are paramount.
Characteristics of 5% Cut-Off Wheels
1. Material Composition The materials used in the manufacture of 5% cut-off wheels are crucial. These wheels are engineered for resilience, often incorporating a combination of abrasive grit and bonding agents that enhance their cutting efficiency.
2. Thickness and Diameter These wheels come in various thickness and diameter options, allowing for versatility in cutting different materials and thicknesses. A thinner wheel will provide quicker cuts, while thicker wheels are designed for prolonged durability.
4. Heat Resistance Due to their construction, these wheels exhibit superior heat dissipation properties. This reduces the risk of thermal damage to both the tool and the material being cut.
5 in cut off wheel
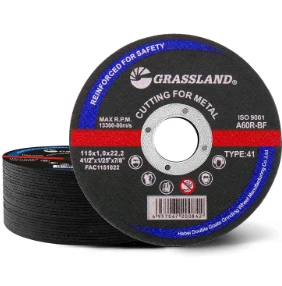
Advantages of Using 5% Cut-Off Wheels
1. Cost Efficiency The 5% designation implies a longer lifespan, reducing the frequency of wheel replacement. This not only saves costs on consumables but also minimizes downtime associated with tool changes.
2. Enhanced Performance The combination of durability and cutting efficiency ensures that the user achieves high-quality cuts with minimal effort. This is particularly beneficial in high-volume production settings where precision is key.
3. Versatility Suitable for a wide range of materials, including ferrous and non-ferrous metals, these wheels can be used in diverse applications—from automotive repair to general metalworking.
4. Safety Features The construction of these wheels often includes specific safety standards to prevent breakage during use, thereby protecting the user from potential hazards.
Applications of 5% Cut-Off Wheels
The applications for 5% cut-off wheels are extensive and span multiple industries
- Metal Fabrication In workshops, these wheels enable quick and efficient cutting of metal components, streamlining the fabrication process. - Construction Used for cutting rebar, pipes, and other materials, these wheels are essential on construction sites where heavy-duty cutting is required. - Automotive Repair In automotive shops, 5% cut-off wheels are used for cutting exhaust systems, body panels, and other metal components with precision.
Conclusion
The 5% cut-off wheel is an indispensable tool in various industrial applications, combining durability, efficiency, and safety. Understanding the specifications and advantages of these wheels allows manufacturers and craftsmen to select the right tools for their projects, enhancing productivity and ensuring high-quality results. As technology continues to advance, the evolution of cut-off wheels will likely lead to even more innovative solutions, further solidifying their position as a cornerstone of industrial tooling.
Post time:Dec - 04 - 2024