Understanding the 7% Increase in Flap Disc Efficiency
Flap discs have become an indispensable tool in various industries, especially in metalworking, construction, and automotive repair. Over the years, manufacturers have continually sought innovative methods to enhance their performance and efficiency. Recent studies suggest a 7% increase in the efficiency of flap discs, signaling a significant milestone in the realm of abrasive tools. This article delves into the implications of this enhancement, its underlying technology, and what it means for professionals in the field.
What is a Flap Disc?
A flap disc is made from overlapping layers or flaps of abrasive material, typically secured to a central hub. Used primarily for grinding and finishing applications, flap discs offer numerous advantages over traditional grinding wheels. They are designed to provide a smoother finish, reduced heat generation, and improved longevity. These qualities make them highly sought after for tasks such as weld grinding, surface preparation, and deburring.
The 7% Efficiency Increase Explained
The recent discovery of a 7% efficiency increase in flap discs can be attributed to advancements in manufacturing techniques and material technology. By optimizing the abrasive grain composition and improving the adhesion between the flaps and the backing material, manufacturers have produced discs that not only last longer but also operate more effectively. This enhancement means that operators can achieve faster material removal rates while maintaining a superior finish.
Another contributing factor to this efficiency gain is the design of the flap discs themselves. Modern discs often feature an angled flap arrangement that allows for better access to surfaces and edges. This design change translates to more effective grinding and reduced likelihood of damage to the workpiece.
Benefits for Professionals
7 in flap disc
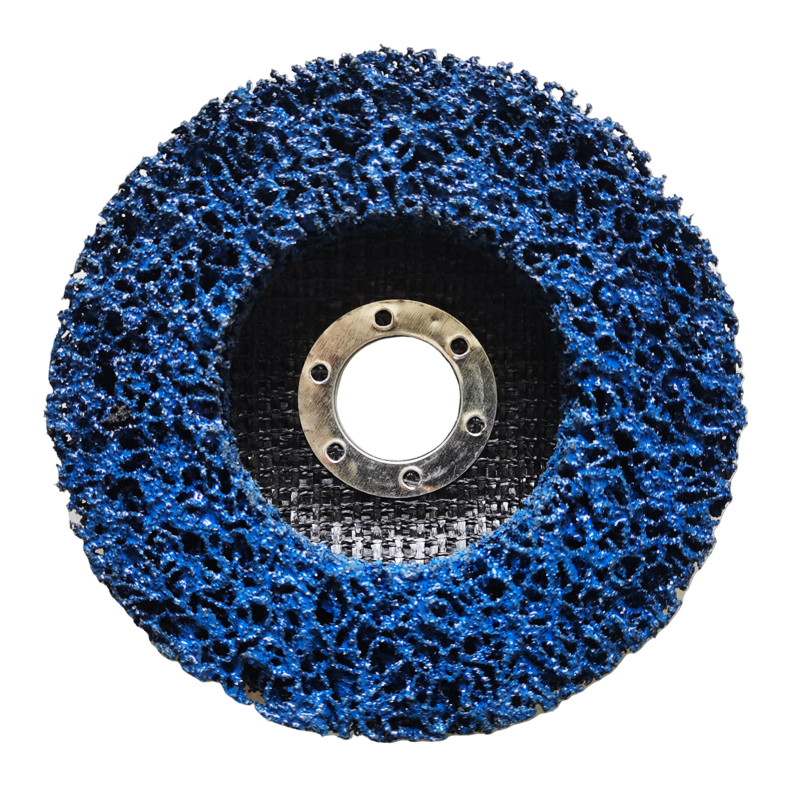
For professionals in metalworking and construction, the implications of a 7% efficiency increase are profound. Here’s how it can positively impact their work
1. Time Savings The increased efficiency allows operators to accomplish tasks more quickly, thereby reducing overall project time. This can be particularly beneficial in high-demand industries, where every second counts.
2. Cost-Effectiveness With improved longevity and faster material removal rates, users can expect a decrease in operational costs. Fewer flap discs will be needed over time, which translates to significant savings.
3. Enhanced Surface Finish The smoother finish achieved with these advanced discs reduces the need for extensive rework, leading to higher quality outcomes and increased client satisfaction.
4. Versatility The enhanced performance characteristics make these flap discs suitable for a broader range of materials and applications, offering users more flexibility in their tool choices.
Conclusion
The recent 7% increase in the efficiency of flap discs marks a noteworthy development in the manufacturing of abrasive tools. As industries demand faster, more efficient, and higher-quality finishing processes, innovations such as these meet those needs head-on. By integrating new technologies and optimizing designs, manufacturers are setting new standards for performance and reliability.
For professionals in the field, this advancement not only streamlines operations but also contributes to improved safety and reduced waste, highlighting the value of staying updated with such technological progresses. As we move forward, it’s crucial for industry players to embrace these advancements to maintain a competitive edge while delivering exceptional results in their projects. The evolution of flap disc technology exemplifies how continuous improvement can significantly impact efficiency and productivity in the ever-evolving world of metalworking and beyond.
Post time:Dec - 19 - 2024