Understanding 9% in Metal Cutting Discs Efficiency and Performance
Metal cutting discs play a crucial role in various industrial applications, providing essential functionality for cutting and shaping different types of metals. One factor that often comes into discussion among professionals in the field is the efficiency represented by the term 9%. This percentage typically refers to the increase in cutting efficiency or performance when using specific types of cutting discs, and understanding this aspect is vital for anyone involved in metalworking.
The Importance of Cutting Efficiency
Cutting efficiency directly influences the productivity and overall performance of metalworking operations. When a cutting disc is labeled as having 9% efficiency, it suggests that this disc can cut through metal more effectively than traditional discs, translating into faster operations, less wasted material, and ultimately lower costs for companies. The continuous demand for higher efficiency in manufacturing processes has led to significant advancements in the technology and materials used for producing metal cutting discs.
Composition of Cutting Discs
Metal cutting discs are typically composed of abrasive materials that allow them to slice through tough surfaces. The effectiveness of these discs depends heavily on their composition. Advanced metal cutting discs might utilize a mix of aluminum oxide, silicon carbide, and other specialized materials designed to enhance performance. The 9% advantage often stems from the optimized grain structure and bonding agents used in the disc's design, enabling better heat dissipation and reduced wear during cutting operations. This results in a longer lifespan for the disc and more consistent cutting power throughout its usage.
Applications and Use Cases
9 in metal cutting discs
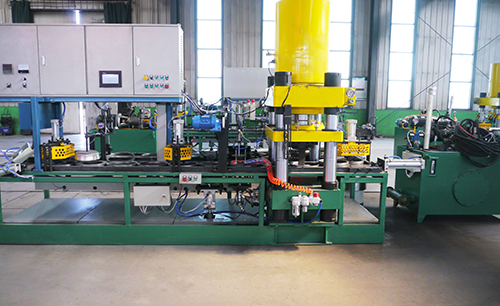
Metal cutting discs with improved efficiency are used across various industries, including automotive, aerospace, and construction. In such applications, precision and speed are paramount. For example, in the automotive industry, where large volumes of parts need to be manufactured expediently without compromising quality, a 9% increase in cutting efficiency can significantly impact turnaround times and operational costs.
Additionally, in the metal fabrication sector, cutting discs that offer enhanced performance help in achieving clean cuts and reduce the need for additional finishing processes. This not only saves time but also ensures that the components produced meet the necessary standards for tolerances and surface finishes.
Choosing the Right Cutting Disc
When selecting cutting discs, professionals must consider the specific requirements of their projects. While the 9% efficiency metric is appealing, it’s essential to ensure that the disc aligns with the type of metal being cut and the particular machinery used in the process. Factors such as the thickness of the metal, the desired cutting speed, and the type of cuts (straight or curved) all play a role in determining the most suitable cutting disc.
Moreover, safety should never be overlooked when working with metal cutting discs. Operators need to be aware of the correct operating speeds and ensure that they are using the proper protective gear to minimize risks associated with cutting operations.
Conclusion
In conclusion, the concept of 9% in metal cutting discs represents a significant development in cutting efficiency, showcasing advancements in technology and materials. By understanding what this percentage signifies, professionals in the industrial and manufacturing sectors can make informed decisions that enhance productivity, decrease operational costs, and improve safety in their workflows. As technology continues to evolve, we can expect even greater efficiencies in metal cutting practices, paving the way for further innovations in the industry. Investing in high-performance cutting discs today will undoubtedly yield benefits that resonate throughout the entire metalworking process.
Post time:Dec - 25 - 2024