Understanding Abrasive Flap Discs An Essential Tool for Metalworking
In the realm of metalworking, the choice of tools significantly impacts the quality of the finished product. One such tool that has gained prominence in recent years is the abrasive flap disc. Used extensively for grinding, finishing, and polishing metal surfaces, abrasive flap discs offer a versatile solution for various industrial applications. This article explores the characteristics, advantages, and proper usage of abrasive flap discs.
What are Abrasive Flap Discs?
Abrasive flap discs are made up of multiple overlapping layers of abrasive material, typically coated with aluminum oxide or zirconia. These layers, or 'flaps', are attached to a backing plate, which is then mounted on a power tool, such as an angle grinder. The unique design allows these discs to provide a consistent scratching pattern and durability, making them suitable for a wide range of tasks.
Flap discs come in various types, each designed for specific applications. For instance, Type 27 flap discs are flat and ideal for grinding and polishing flat surfaces, whereas Type 29 discs are angled, making them effective for contouring and edge work.
Advantages of Abrasive Flap Discs
1. Versatility Abrasive flap discs can be used on various materials, including metal, wood, and plastic. This versatility makes them an essential tool in sectors ranging from metal fabrication and automotive industries to woodworking.
2. Efficient Material Removal The layered structure of flap discs allows for effective and quick material removal, which is especially beneficial when working on larger surfaces.
3. Control and Precision The design of flap discs provides better control compared to traditional grinding wheels. Users can achieve a finer finish and more precise work, which is crucial in metalworking and detailing.
4. Reduced Heat Generation Compared to traditional grinding wheels, flap discs generate less heat during operation. This characteristic minimizes the risk of warping and reduces the chances of damaging the workpiece.
5. Longer Lifespan Flap discs often have a longer operational life than other abrasive tools. Their layered construction leads to a slower rate of wear, which means fewer replacements and lower overall costs.
Choosing the Right Flap Disc
Selecting the appropriate abrasive flap disc is crucial for achieving optimal results. Here are some factors to consider
abrasive flap
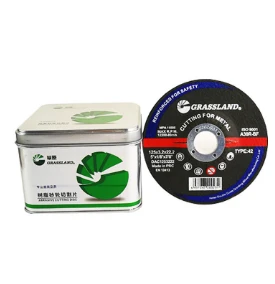
- Abrasive Material The most common materials used are aluminum oxide and zirconia. Aluminum oxide is generally suitable for ferrous metals, whereas zirconia is more durable and preferred for tougher materials like stainless steel.
- Grit Size The grit size indicates the coarseness of the abrasive material. Higher grit numbers correspond to finer finishes, while lower numbers are used for heavy material removal. It’s essential to choose grit size based on the specific task at hand.
- Backing Type The backing material can be resin, cloth, or plastic. Resin-backed discs tend to be more durable, while cloth-backed ones provide additional flexibility for contouring work.
- Disc Shape As mentioned earlier, the two common shapes are Type 27 (flat) and Type 29 (angled). Choosing the right shape depends on the surface configuration and the angle of the work.
How to Use Abrasive Flap Discs Safely and Effectively
To achieve the best results, it is vital to use abrasive flap discs correctly. Here are some tips
1. Ensure Proper Attachment Make sure the flap disc is securely attached to the power tool to prevent accidents.
2. Maintain the Correct Angle When working with angled discs, maintain the recommended angle (typically between 15° to 30°) to optimize cutting efficiency.
3. Apply Even Pressure Excessive pressure can cause premature wear of the disc. Apply consistent but moderate pressure for optimal results.
4. Wear Protective Gear Always wear suitable personal protective equipment, such as goggles, masks, and gloves, to protect against flying debris and dust.
5. Inspect Regularly Check the flap disc for signs of wear before each use and replace it if any issues are detected.
Conclusion
Abrasive flap discs are integral to the metalworking toolkit, offering a solution that combines efficiency, versatility, and precision. With the right knowledge and selection of discs, metalworkers can enhance their productivity and achieve superior finishes on their projects. By understanding the characteristics and proper usage of these discs, professionals can take full advantage of the benefits they offer, transforming the metalworking process into something more effective and refined. Whether you are a seasoned expert or a novice in the field, incorporating abrasive flap discs into your workflow is a decision that can lead to substantial improvements in quality and efficiency.
Post time:Dec - 07 - 2024