Understanding Abrasive Flap Discs Features and Applications
Abrasive flap discs are versatile tools widely used in metalworking and various other industries for grinding, blending, and finishing surfaces. Combining the flexibility of a flap wheel with the convenience of a standard grinding disc, they are designed to deliver a smooth finish while allowing for aggressive material removal. In this article, we will explore the features, benefits, applications, and maintenance of abrasive flap discs.
Features of Abrasive Flap Discs
One of the most notable features of abrasive flap discs is their construction. Composed of multiple layers or flaps of coated abrasive material, these discs are affixed to a central backing plate, which can be made of different materials such as fiberglass or plastic. The flaps are arranged in a manner that allows them to flex during usage, enabling the disc to adapt to the contour of the workpiece, thus providing a consistent finish even on uneven surfaces.
Abrasive flap discs come in various sizes and grit levels, making them suitable for a wide range of applications. Common sizes range from 4 inches to 7 inches in diameter, while grit levels can vary from coarse (40 grit) for heavy material removal to fine (120 grit and above) for finishing tasks. The choice of grit depends on the specific requirements of the project and the type of material being worked on.
Benefits of Using Abrasive Flap Discs
One of the primary benefits of abrasive flap discs is their efficiency. Their design allows for faster material removal, which translates into decreased processing times compared to traditional grinding wheels. The flaps wear down evenly, ensuring that the disc maintains its performance throughout its lifespan.
Another advantage is the reduced heat generation during operation. Because flap discs are less aggressive than standard grinding discs, they help to avoid overheating the workpiece. This property is particularly important when working with heat-sensitive materials, as it helps preserve the integrity of the metal and prevents undesirable warping.
Flap discs are also user-friendly. They can easily be mounted on various tools, including angle grinders, making them suitable for both professional and DIY applications. The ergonomic design and adaptability allow operators to achieve better control over the tool, resulting in a more polished finish.
abrasive flap disc
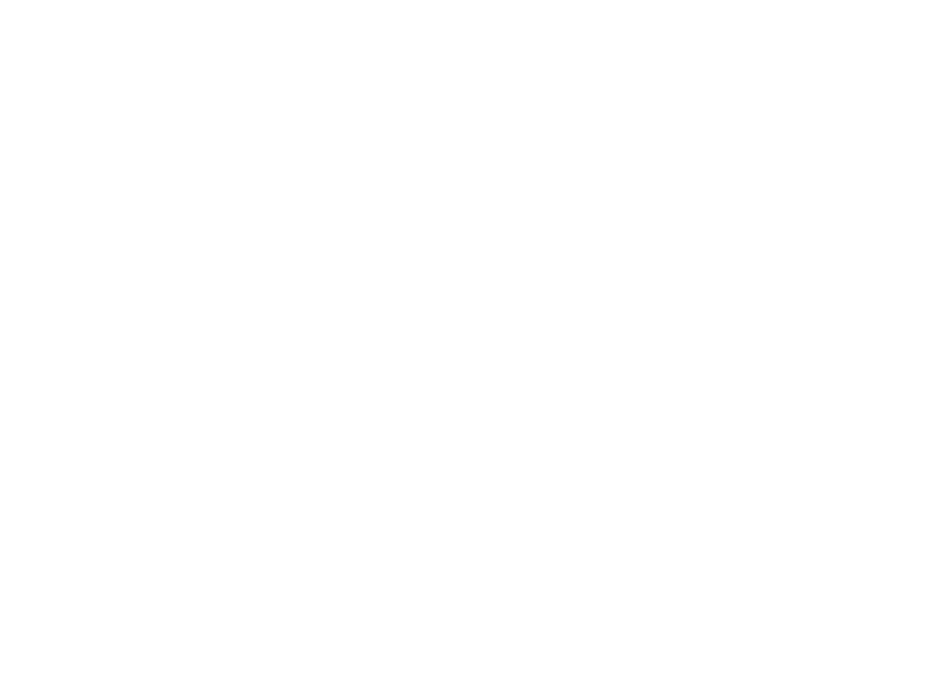
Applications of Abrasive Flap Discs
Abrasive flap discs find applications across multiple industries. In metalworking, they are commonly used for grinding welds, deburring edges, and sanding metal surfaces. Their versatility makes them ideal for both ferrous and non-ferrous metals, including aluminum, stainless steel, and other alloys.
Beyond metalworking, flap discs are also employed in woodworking for shaping and finishing wooden objects. Their ability to deliver a fine finish without damaging the wood surface makes them a valuable tool for woodworkers.
Moreover, industries like automotive, construction, and manufacturing utilize flap discs for surface preparation, paint removal, and rust elimination. Their adaptability allows for effective use on both flat surfaces and complex geometries, exemplifying how they can meet diverse finishing needs.
Maintenance and Best Practices
To maximize the lifespan of abrasive flap discs and achieve optimum performance, proper maintenance and usage practices are essential. Operators should ensure that the discs are stored in a dry, cool place to prevent moisture absorption, which can deteriorate the abrasive material over time.
Additionally, it is crucial to use the right disc for the appropriate application, as using a disc with an unsuitable grit can lead to poor results or premature wear. Following the manufacturer's guidelines regarding speed limits and operating conditions is also vital to ensure safety and effectiveness.
In conclusion, abrasive flap discs serve as an indispensable tool in various grinding and finishing applications. With their unique design, they provide efficient material removal, adaptability to different surfaces, and user-friendly operation. Whether in metalworking, woodworking, or other industrial contexts, these discs continue to be valued for their performance and reliability. Understanding their features, benefits, and best practices can significantly enhance productivity and quality in any project involving surface preparation and finishing.
Post time:Dec - 31 - 2024