Understanding Abrasive Flap Discs A Comprehensive Guide
Abrasive flap discs are an essential tool in various industries, known for their versatility and efficiency in metalworking, woodworking, and other applications requiring surface finishing, grinding, and polishing. This article will delve into what abrasive flap discs are, their construction, applications, and the benefits they offer over traditional grinding wheels.
What Are Abrasive Flap Discs?
Abrasive flap discs consist of multiple overlapping layers or flaps of abrasive material, usually made of aluminum oxide, zirconia, or ceramic. These flaps are mounted on a central hub and arranged in a way that allows them to provide both grinding and finishing functions. Unlike traditional grinding wheels, which can be aggressive and may create a rough surface, flap discs provide a more refined approach that helps in achieving a smoother finish.
Construction of Abrasive Flap Discs
A flap disc typically comprises three main components
1. Backing Material This provides structural support and stability to the disc. Common materials include fiberglass or plastic, which helps in maintaining the integrity of the disc during operation.
2. Abrasive Flaps The flaps are the heart of the flap disc. They are made from an abrasive material that determines the cutting efficiency and finish quality. The arrangement and number of flaps can vary, influencing the disc's performance.
3. Attachment Method Flap discs can be designed for use with various power tools. Common attachment methods include a threaded hole for use with angle grinders and a Velcro-like system for easy swapping.
Flap discs come in various shapes, sizes, and grit types, making them adaptable for different tasks. The shape of the disc can be flat, conical, or curved, optimizing performance in various applications.
Applications of Abrasive Flap Discs
Abrasive flap discs are widely used in numerous applications across different industries, including
abrasive flap disc
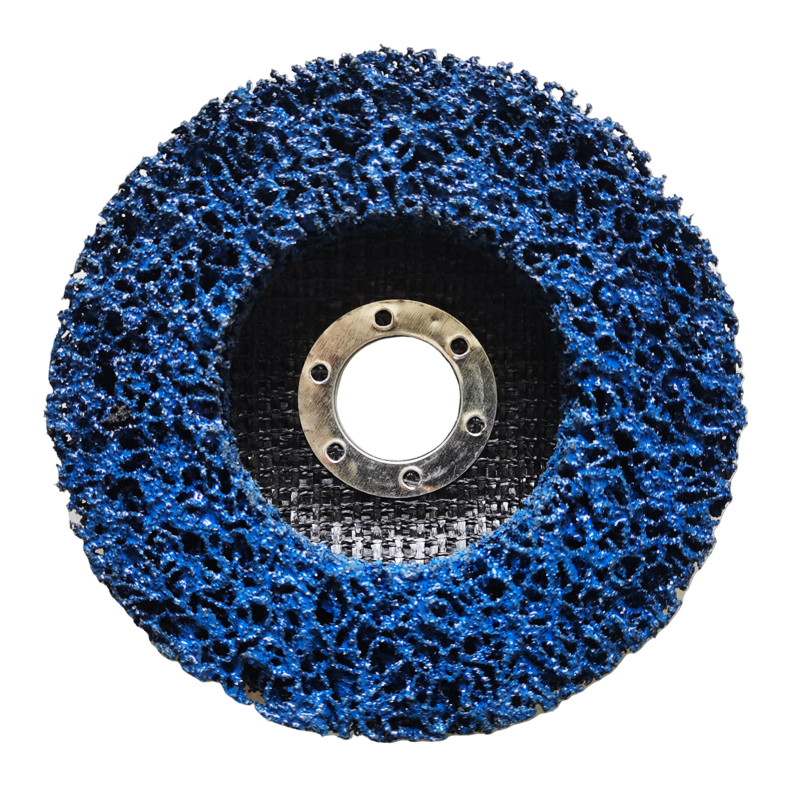
- Metalworking They are often used to grind and finish welds, remove rust, and prepare surfaces for painting or coating.
- Woodworking Woodworkers utilize flap discs for sanding and finishing wood surfaces, as they can produce smooth finishes without excessive material removal.
- Automotive Repair In the automotive sector, flap discs are used for bodywork, effectively smoothing surfaces before painting.
- Construction They are frequently employed in construction for various tasks, such as grinding concrete or removing old paint.
Benefits of Using Abrasive Flap Discs
1. Versatility Abrasive flap discs can perform multiple tasks such as grinding, blending, and finishing with a single tool, making them a more versatile choice than traditional abrasive wheels.
2. Reduced Heat Generation Flap discs are designed to minimize heat buildup during work, which can help prevent warping of the material being worked on and prolong the life of the tool.
3. Longer Lifespan The construction of flap discs allows them to wear evenly, resulting in a longer lifespan compared to traditional grinding wheels. This efficiency means fewer tool replacements and lower operational costs.
4. Better Finish Quality The design of flap discs enables more controlled and precise material removal, leading to finer surface finishes and improved aesthetics in the final product.
5. Ease of Use With various attachment methods, flap discs can be easily changed and matched to different power tools, making them user-friendly and convenient for operators.
Conclusion
Abrasive flap discs are an indispensable tool that offers a multitude of benefits across various applications. Their unique construction and versatility make them suitable for many projects, from metal fabrication to woodworking. As industries continue to evolve, the demand for efficient and effective abrasive solutions like flap discs will only grow, solidifying their place in workshops and professional settings worldwide. By understanding the capabilities and advantages of these tools, professionals can enhance their efficiency and output quality in their respective fields.
Post time:Dec - 09 - 2024