The Importance and Benefits of Alumina Flap Discs in Abrasive Applications
In the realm of material processing and finishing, abrasive tools play a crucial role in achieving desired surface qualities and geometrical precision. Among the various types of abrasives available, alumina flap discs have gained significant popularity due to their versatility, efficiency, and effectiveness. This article delves into the features, applications, and advantages of alumina flap discs, highlighting why they are a preferred choice in many industries.
What Are Alumina Flap Discs?
Alumina flap discs are abrasive tools made from aluminum oxide. These discs consist of multiple overlapping flaps of abrasive material arranged radially around a central hub. The design of these discs allows for greater flexibility and adaptability when working on different surfaces and materials. The quality of the aluminum oxide coating significantly influences the performance of the flap disc, with higher purity levels resulting in more effective grinding and finishing operations.
Key Features of Alumina Flap Discs
1. Versatility Alumina flap discs can be used on various materials, including metals, plastics, wood, and composites. This versatility makes them suitable for diverse applications, from metal fabrication to woodworking.
2. Durability Aluminum oxide is known for its durability and longevity. Flap discs tend to maintain their sharpening abilities longer than traditional grinding wheels, which means fewer replacements and lower costs over time.
3. Efficiency The design of flap discs allows for quick and efficient material removal. The overlapping flaps provide a larger grinding surface, enabling operators to cover more area in less time.
4. Reduced Heat Generation One of the significant advantages of using alumina flap discs is their ability to generate less heat during operation. Traditional grinding methods can cause heat buildup, which may affect the integrity of the material being worked on. Flap discs dissipate heat more effectively, reducing the risk of warping or damage to the workpiece.
alumina flap disc
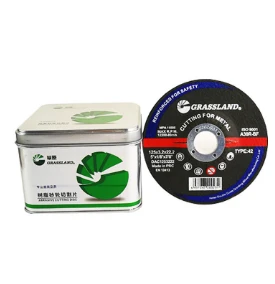
5. Enhanced Surface Finish The flexible nature of flap discs allows them to contour to the workpiece, improving the uniformity of the finished surface. As the flaps wear down, they continuously expose new abrasive material, ensuring consistent performance throughout their lifespan.
Applications of Alumina Flap Discs
1. Metal Fabrication In metalworking, alumina flap discs are used for grinding, blending, and finishing on a variety of metals, including stainless steel and aluminum. They excel in preparing surfaces for welding and painting.
2. Woodworking These discs are also popular in the woodworking industry for sanding and finishing surfaces. Their ability to conform to irregular shapes makes them ideal for intricate wood projects.
3. Automotive Industry In automotive repair and manufacturing, alumina flap discs are used for bodywork, refinishing, and welding prep, ensuring that surfaces are appropriately prepared for further processes.
4. Construction Within the construction sector, they are employed for surface preparation on concrete and masonry surfaces, as well as for finishing details on metallic structures.
Conclusion
Alumina flap discs offer a unique blend of performance, versatility, and efficiency that makes them indispensable in various abrasive applications. Their durability, reduced heat generation, and superior finishing capabilities make them a favored choice among professionals and hobbyists alike. As industries continue to evolve, the demand for effective and versatile tools like alumina flap discs will undoubtedly grow. Investing in high-quality alumina flap discs not only enhances productivity but also ensures superior results across an array of applications. With their proven track record in performance and innovation, alumina flap discs are a reliable choice for any abrasive task, paving the way for advancements in material processing and finishing across multiple fields.
Post time:Dec - 19 - 2024