Understanding Aluminum Flap Wheels Uses, Benefits, and Applications
Aluminum flap wheels are essential tools in the world of metalworking and finishing. These versatile abrasive tools are designed to smooth, polish, and finish surfaces, making them invaluable in various industries, including automotive, aviation, construction, and manufacturing. In this article, we’ll delve into what aluminum flap wheels are, their benefits, and their common applications.
What Are Aluminum Flap Wheels?
Aluminum flap wheels consist of multiple overlapping layers or flaps of coated abrasive material attached to a central hub. The flaps are typically made of aluminum oxide, a common abrasive that provides a balance of durability and cutting ability. These flaps are arranged in a radial pattern, allowing for effective contact with the workpiece while minimizing the risk of excessive heat buildup, which can damage the surface being worked on.
Flap wheels come in various sizes, shapes, and grits, making them suitable for different tasks and materials. The flexibility of the flaps allows them to conform to the shape of the workpiece, ensuring even and consistent finishing.
Benefits of Using Aluminum Flap Wheels
1. Versatility One of the most significant advantages of aluminum flap wheels is their versatility. They can be used on a variety of materials, including metal, wood, plastic, and composites. This makes them a preferred option for multiple applications, from rough grinding to fine finishing.
2. Efficiency Aluminum flap wheels create less friction than traditional grinding wheels, which means they generate less heat during operation. This characteristic is crucial for preventing distortion or damage to sensitive components.
3. Consistent Results The design of flap wheels allows for even wear of the abrasive material, which contributes to a consistent finish. As the flaps wear away, fresh abrasive material is constantly exposed, maintaining high performance throughout the wheel's lifespan.
4. Easy to Use Flap wheels can be mounted on handheld power tools or stationary machines, making them easy to use for both professionals and DIY enthusiasts. They can be attached to angle grinders, die grinders, and other equipment, providing convenience in various working environments.
aluminum flap wheel
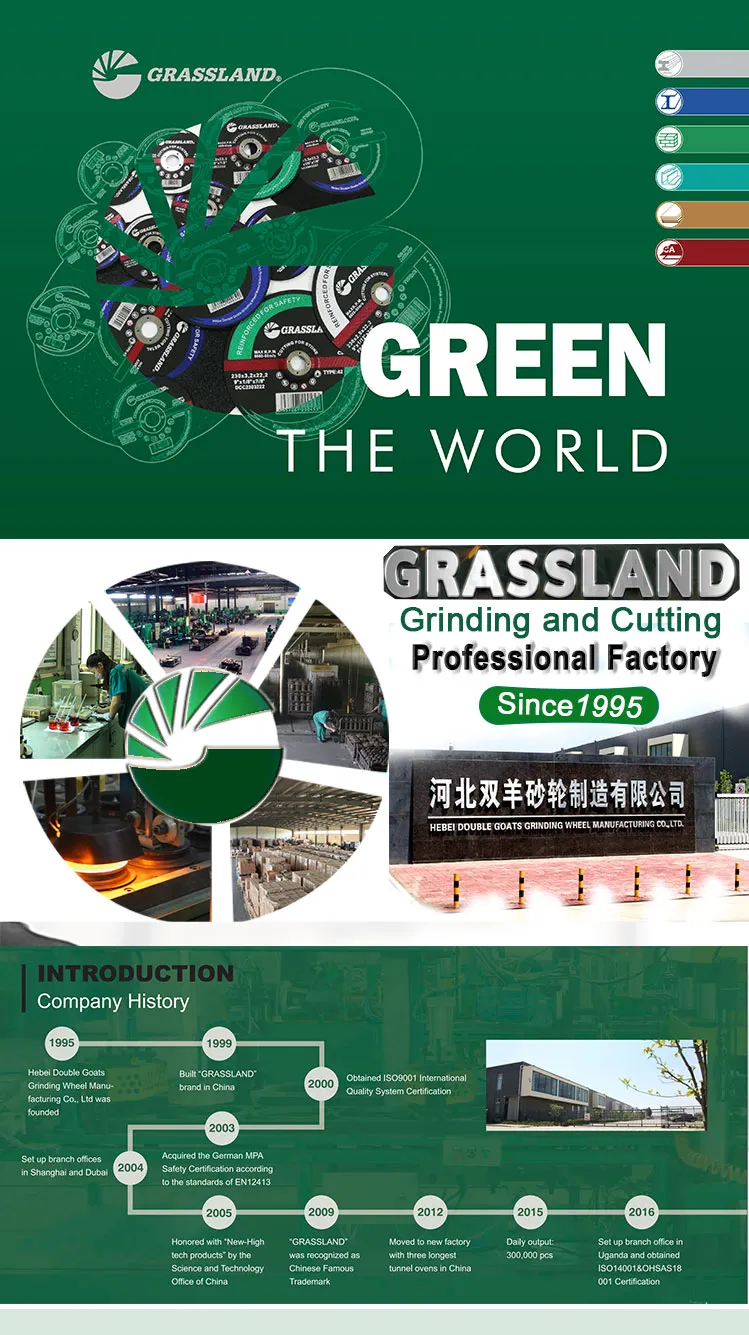
5. Cost-Effective Compared to other abrasive products, aluminum flap wheels are generally cost-effective. They offer a long operational life and reduce the number of tool changes needed, resulting in lower overall costs for users.
Applications of Aluminum Flap Wheels
Aluminum flap wheels are widely used across various industries due to their many benefits
1. Metal Fabrication In metal fabrication shops, these wheels are used to grind, deburr, and finish metal components. They are particularly effective for removing welds and preparing surfaces for painting or coating.
2. Automotive Industry Flap wheels are essential in the automotive industry for finishing engines, frames, and body parts. They assist in achieving a smooth surface finish and preparing parts for further processing.
3. Woodworking In woodworking, aluminum flap wheels can be used for sanding and shaping wooden surfaces. They provide a smooth finish without leaving deep marks, making them suitable for fine woodworking and cabinet making.
4. Aviation The aviation industry relies on flap wheels for maintaining aircraft components. The need for precise surface finishing in aviation makes these wheels a valuable tool for ensuring safety and performance.
5. Construction In the construction sector, aluminum flap wheels can be used for various tasks, including finishing concrete, stone, and metal fixtures.
Conclusion
In conclusion, aluminum flap wheels are indispensable tools in many trades and industries, offering efficiency, versatility, and consistency in metalworking and finishing applications. Whether you are a professional or a hobbyist, understanding the uses and benefits of aluminum flap wheels can enhance your productivity and the quality of your finished products. As technology continues to evolve, these tools will undoubtedly remain a staple in the world of fabrication and finishing.
Post time:Oct - 11 - 2024