The Benefits and Applications of Aluminum Grinding Flap Discs
Aluminum grinding flap discs are essential tools for metalworking, particularly in the fabrication and finishing of aluminum materials. These discs are designed to provide an efficient and effective means of grinding, blending, and finishing aluminum surfaces. Their unique construction and versatility make them a preferred choice in various industries, including automotive, aerospace, and general manufacturing.
Understanding the Structure of Flap Discs
Flap discs consist of multiple abrasive flaps that are adhered to a backing plate, typically made from fiberglass or plastic. These flaps are usually made from a combination of aluminum oxide or zirconia alumina, materials known for their durability and cutting efficiency. The flaps are arranged in a circular pattern, allowing for a larger surface area to be in contact with the workpiece during operation. This design not only enhances performance but also helps reduce heat buildup and prolongs the lifespan of the disc.
Key Advantages of Aluminum Grinding Flap Discs
1. Versatility Aluminum grinding flap discs are suitable for various applications, including surface preparation, weld seam removal, deburring, and finishing. They can be used on a variety of substrates, including aluminum, stainless steel, and carbon steel, making them an invaluable tool in any workshop.
2. Efficiency The ergonomic design and aggressive cutting action of flap discs increase productivity. They can remove material quickly while providing a smooth finish, which minimizes the need for additional polishing or finishing processes.
3. Reduced Heat Generation One of the significant advantages of flap discs over traditional grinding wheels is their ability to dissipate heat. The flaps' design allows for better airflow, reducing the chances of heat distortions or burn marks on the aluminum workpiece.
4. Cost-effectiveness Although flap discs may have a higher upfront cost compared to traditional grinding wheels, their durability and longevity often result in lower overall costs. They can be used longer and require fewer replacements, which is particularly beneficial for high-volume manufacturing environments.
5. Safety Unlike grinding wheels, which can shatter or break under stress, flap discs are less likely to cause injury due to their flexible design. This characteristic allows them to conform to the workpiece, reducing the risk of snagging and kickback.
aluminum grinding flap disc
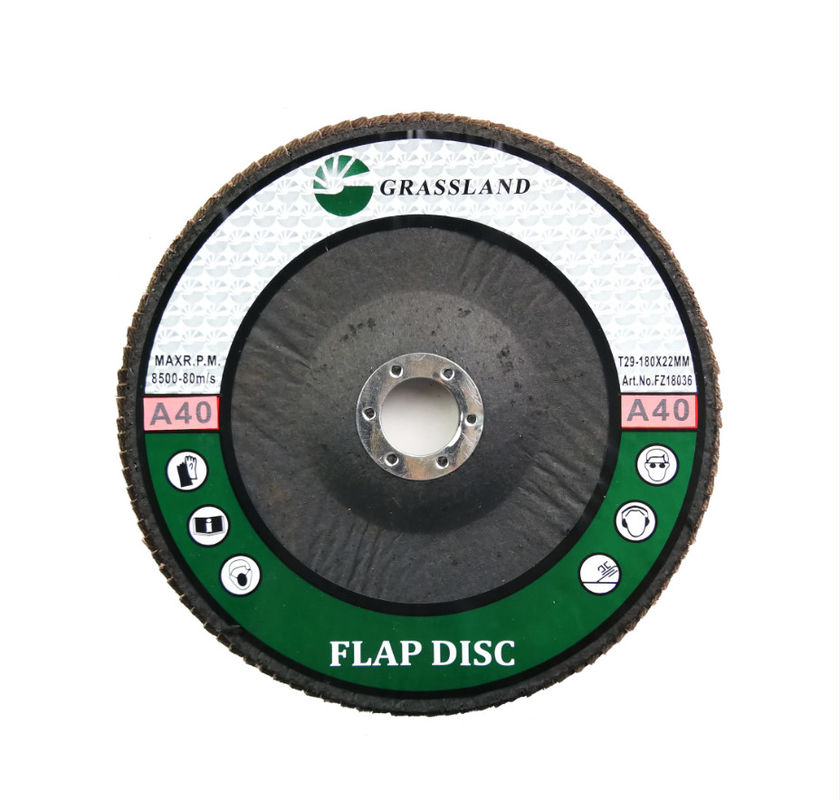
Choosing the Right Flap Disc for Aluminum
When selecting a flap disc for aluminum applications, several factors should be considered
1. Grit Size Flap discs come in various grit sizes, typically ranging from 40 to 120 grit. The choice depends on the desired finish; coarser grits (40-60) are ideal for heavy material removal, while finer grits (80-120) are suitable for finishing tasks.
2. Disc Thickness Thicker discs offer more durability and are better for heavy grinding, while thinner discs provide a finer finish and are more suitable for detailed work.
3. Backing Type Flap discs can have different backing types, such as fiberglass or plastic. Fiberglass-backed discs are more robust, while plastic-backed discs are lighter and can be advantageous in specific applications.
Applications in Various Industries
Aluminum grinding flap discs find their applications across numerous sectors. In the automotive industry, these discs are used for bodywork repair, removal of paint and rust, and prepping metal surfaces for welding. In the aerospace sector, they serve the critical function of maintaining the quality and finish of aircraft components. Moreover, sheet metal fabrication and general construction applications greatly benefit from the efficiency and performance of these discs.
Conclusion
Aluminum grinding flap discs are a vital component in the metalworking toolkit, offering a combination of efficiency, versatility, and safety. Their unique structure allows for effective material removal while maintaining the integrity of the aluminum surface. By choosing the right flap disc for specific applications, metal fabricators can enhance their productivity and achieve superior finishes, making flap discs an indispensable part of modern metalworking practices. As industries continue to evolve and demand higher precision, the role of these innovative tools will undoubtedly become even more critical.
Post time:Sep - 30 - 2024