Understanding Aluminum Grinding Wheels A Key to Precision and Efficiency
Aluminum grinding wheels are essential tools in various industrial and manufacturing applications where efficiency and precision are paramount. These specialized grinding wheels are designed to handle the unique challenges posed by aluminum, a material known for its lightweight properties and structural integrity. In this article, we will explore the significance of aluminum grinding wheels, their construction, types, and the best practices for their use.
The Importance of Aluminum Grinding Wheels
Aluminum has gained immense popularity across industries due to its favorable properties, including resistance to corrosion, high strength-to-weight ratio, and excellent thermal conductivity. However, when it comes to machining and grinding aluminum, conventional grinding wheels may not be suitable because they can cause smearing or clogging. This is where aluminum grinding wheels come into play, providing an efficient solution for shaping, smoothing, and finishing aluminum surfaces.
Construction and Composition
Aluminum grinding wheels are constructed using various abrasive materials, primarily designed to optimize performance when working with aluminum. The most common abrasives used include aluminum oxide, zirconia alumina, and silicon carbide. Each of these materials is engineered to provide different levels of hardness and wear resistance, allowing users to choose the right wheel for their specific application.
The structure of aluminum grinding wheels typically features a porous bond that allows for better chip clearance. This helps prevent the clogging that can occur when grinding soft materials like aluminum. The grinding wheel's design is crucial in maintaining a cooler operating temperature, which helps prevent distortion of the aluminum workpiece due to heat buildup.
Types of Aluminum Grinding Wheels
There are several types of aluminum grinding wheels, each tailored for different tasks
. Some of the most common types include1. Depressed Center Wheels These wheels are ideal for grinding flat surfaces and are widely used in applications that require aggressive material removal. 2. Cup Wheels Designed for larger surface areas, cup wheels are effective for deburring and finishing aluminum edges and contours.
3. Cut-off Wheels These thin wheels are perfect for precise cutting applications, allowing for quick and clean cuts in aluminum materials.
aluminum grinding wheel
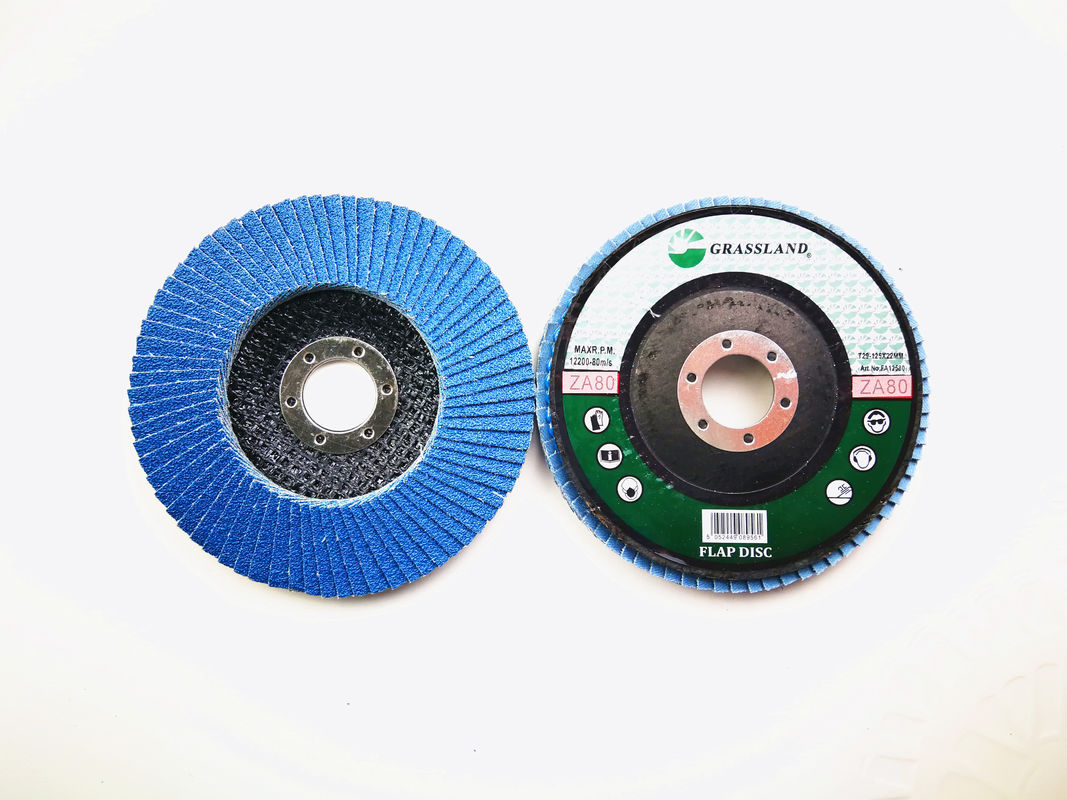
4. Flap Discs These wheels provide a combination of grinding and finishing in one tool, making them versatile for various applications, including surface preparation and blending.
Best Practices for Using Aluminum Grinding Wheels
To maximize the effectiveness and lifespan of aluminum grinding wheels, it is essential to follow these best practices
1. Select the Right Wheel Always choose a grinding wheel that is specifically designed for aluminum. Check the manufacturer's recommendations for compatibility.
2. Maintain Proper Speed Use tools that operate at the recommended speed for the selected grinding wheel to prevent overheating and ensure safe operation.
3. Keep the Work Area Clean Regularly remove aluminum chips and debris from the work area. This helps maintain visibility and reduces the risk of accidents.
4. Use Adequate Pressure Apply sufficient pressure while grinding but avoid excessive force that can lead to wheel damage or overheating.
5. Wear Protective Gear Always use appropriate personal protective equipment (PPE), including safety goggles and gloves, to protect against flying debris and other hazards.
Conclusion
Aluminum grinding wheels are vital in enhancing productivity and precision in aluminum machining processes. By understanding the unique properties of these wheels, selecting the appropriate type for specific tasks, and adhering to best practices, operators can achieve optimal results while ensuring safety and efficiency. As the manufacturing landscape continues to evolve, staying informed about advancements in grinding technology will undoubtedly lead to better performance and enhanced outcomes in aluminum applications.
Post time:Oct - 09 - 2024