The Versatility of Aluminum Oxide Cutting Wheels in Modern Fabrication
In the world of metalworking and fabrication, precision and efficiency are critical. One of the unsung heroes in achieving these goals is the aluminum oxide cutting wheel. This essential tool plays a crucial role in numerous applications, from metal cutting to surface preparation, due to its unique properties and versatility.
What is Aluminum Oxide?
Aluminum oxide, also known as alumina, is a chemical compound of aluminum and oxygen. It is known for its hardness and durability, making it an ideal material for cutting wheels. In the manufacturing of cutting wheels, aluminum oxide grains are bonded together with a resin or ceramic material, creating a robust tool that can withstand high speeds and abrasive wear.
Properties and Benefits
One of the primary advantages of aluminum oxide cutting wheels is their hardness. These wheels can efficiently cut through various materials, including metals like steel and stainless steel, making them indispensable in workshops and manufacturing plants. The hardness of aluminum oxide ensures a longer lifespan for the cutting wheel, reducing the frequency of replacements and ultimately saving on costs.
Another significant benefit is their ability to produce consistent results. When precision is paramount, aluminum oxide cutting wheels deliver clean cuts, minimizing the need for secondary operations such as grinding or polishing. This is especially important in industries where tolerances are tight and surface finishes are critical, such as aerospace, automotive, and construction.
Aluminum oxide wheels also exhibit excellent thermal stability. They can withstand high temperatures generated during cutting without losing their structural integrity. This property is essential when dealing with materials that heat up rapidly, as it prevents the wheels from warping or degrading, thus maintaining their performance during long cutting sessions.
aluminum oxide cutting wheel
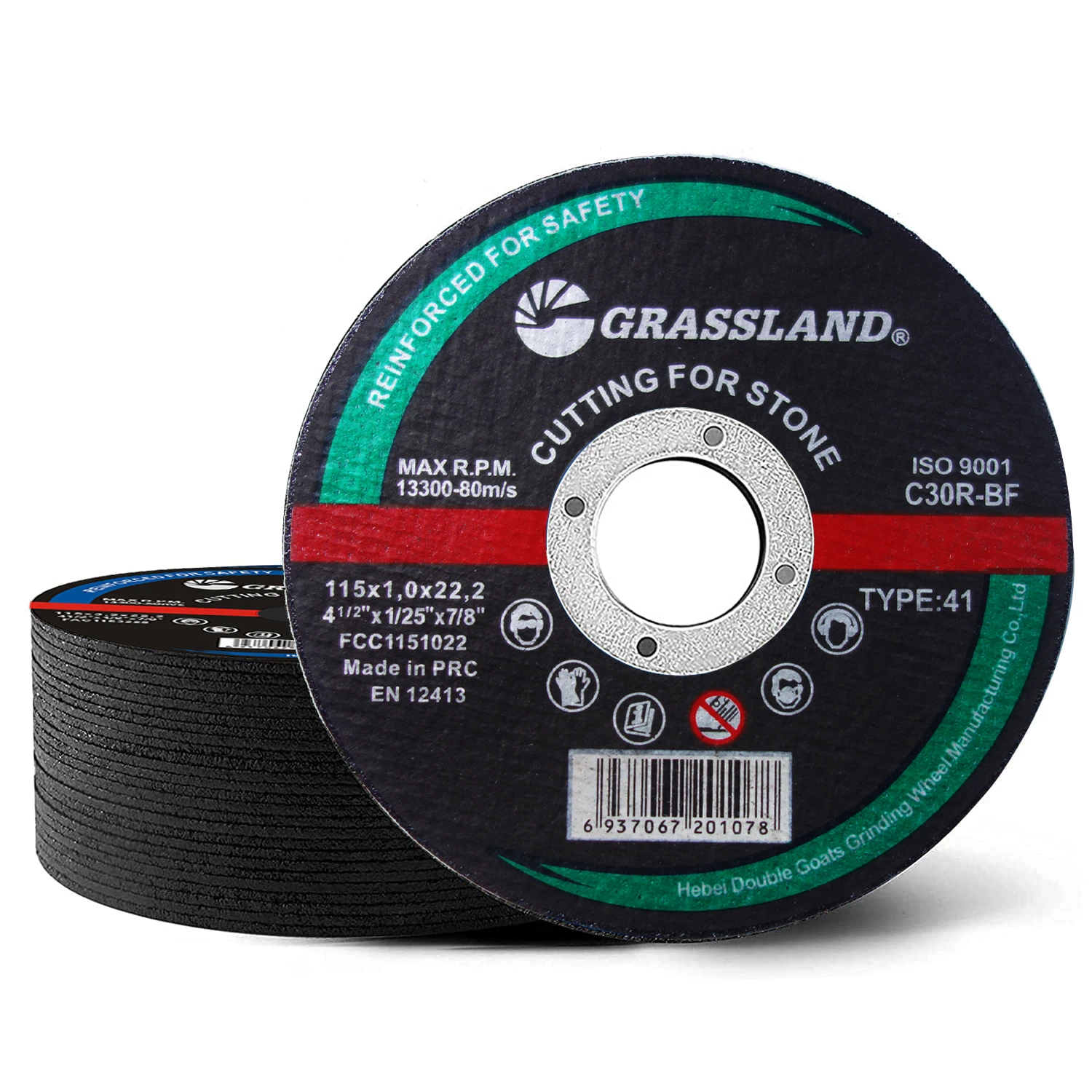
Additionally, the versatility of aluminum oxide cutting wheels extends beyond metalworking. These wheels can also be used for cutting and grinding other materials such as plastics, ceramics, and even wood, making them a valuable asset across multiple industries. Their adaptability fulfills a wide range of requirements, offering users flexibility in their operations.
Different Types of Aluminum Oxide Cutting Wheels
Aluminum oxide cutting wheels come in various types to cater to specific needs. For instance, there are general-purpose wheels designed for a broad range of materials, while others are fine-tuned for particular applications like metal fabrication or masonry. The wheels are available in different grit sizes, allowing users to choose the appropriate one based on the material and desired finish.
Another common variant is the reinforced aluminum oxide cutting wheel, which has added strength to withstand higher pressure and speed. These wheels are particularly useful in industrial settings where heavy-duty applications are the norm, ensuring safety and reliability during operation.
Safety Considerations
While using aluminum oxide cutting wheels, it's essential to consider safety precautions. Proper protective gear, such as safety glasses, gloves, and hearing protection, should always be worn to protect against debris and noise. Additionally, ensuring that the cutting wheel is installed correctly on the machine is crucial to prevent accidents and maximize performance.
Conclusion
In conclusion, aluminum oxide cutting wheels are an indispensable tool in the realm of metalworking and fabrication. Their hardness, durability, and versatility make them suitable for a wide array of applications across various industries. As manufacturing continues to evolve and the demand for precision and efficiency increases, aluminum oxide cutting wheels will undoubtedly remain a central figure in achieving these goals, allowing businesses to maintain high standards of quality while optimizing their operations. Understanding the features and proper usage of these cutting wheels can lead to significant improvements in productivity and safety for operations that depend heavily on cutting and grinding applications.
Post time:Oct - 17 - 2024