Understanding Aluminum Oxide Flap Wheels A Comprehensive Guide
Aluminum oxide flap wheels are specialized tools used in various industries for deburring, finishing, and polishing tasks. Their unique design and material properties make them an essential component in metalworking, woodworking, and other manufacturing processes. This article aims to explore the characteristics, applications, and advantages of aluminum oxide flap wheels.
What are Aluminum Oxide Flap Wheels?
Aluminum oxide flap wheels consist of multiple overlapping flaps made of abrasive material attached to a core. These flaps are typically made from aluminum oxide, a common and effective abrasive material known for its durability and versatility. The design allows for a more flexible grinding action, which can conform to the surfaces being worked on, making them suitable for a variety of shapes and contours.
The flaps are arranged around a cylindrical core, and they come in various sizes, grits, and configurations to accommodate different applications. The grit size refers to the size of the abrasive particles on the flap, affecting the coarseness of the wheel. A lower grit number indicates a coarser wheel, ideal for heavy material removal, while a higher grit number is finer, suitable for polishing and achieving a smooth finish.
Applications of Aluminum Oxide Flap Wheels
Aluminum oxide flap wheels are used in numerous applications across different industries. Some of the most common uses include
1. Metalworking In metal fabrication, flap wheels are utilized for deburring sharp edges and smoothing welds. They can remove oxidation, rust, and paint while preparing surfaces for further processing or finishing.
2. Woodworking Woodworkers employ flap wheels to remove rough edges and finish surfaces, achieving a smooth and polished appearance. They are excellent for contouring and sanding intricate details without damaging the material.
3. Automotive Industry In automotive repair and restoration, aluminum oxide flap wheels are used for polishing and preparing surfaces before painting. They can also help in removing imperfections from metal parts.
4. Aerospace and Marine The aerospace industry benefits from aluminum oxide flap wheels for their ability to prepare surfaces and ensure a good bonding surface for coatings and paints, critical in high-stress environments where safety is a priority.
aluminum oxide flap wheel
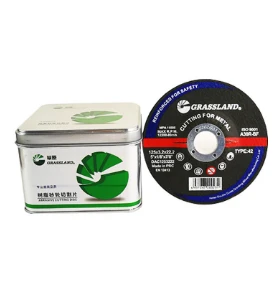
5. Artisan Crafts Crafters and artists use flap wheels in creating intricate designs, performing delicate finishing work to enhance the aesthetics of their pieces.
Advantages of Aluminum Oxide Flap Wheels
The popularity of aluminum oxide flap wheels can be attributed to several advantages
- Versatility Flap wheels can be used on various materials, including metals, woods, and plastics. This versatility makes them ideal for mixed-material workshops.
- Reduced Loading The structure of flap wheels allows for better cooling and reduces the risk of loading, which occurs when debris clogs the abrasive surface, leading to less effective grinding.
- Conformability The overlapping flaps can adapt to the shape of the workpiece, ensuring a consistent finish even on irregular surfaces. This conformability is particularly beneficial for complex shapes and contours.
- Longer Lifespan Due to the durable properties of aluminum oxide, these flap wheels can provide longer usage life compared to other abrasives, making them a cost-effective choice for many applications.
- Enhanced Finish Flap wheels often leave a smoother finish compared to other grinding tools, minimizing the need for additional polishing processes.
Conclusion
In conclusion, aluminum oxide flap wheels are an indispensable tool in various industries for achieving high-quality finishes on a wide array of materials. Their unique design, combined with the properties of aluminum oxide, provides users with a versatile and efficient solution for grinding, deburring, and polishing tasks. Whether in metalworking, woodworking, or automotive applications, the benefits of using flap wheels make them a staple in any workshop or industrial setting. By understanding their functions and applications, one can leverage these tools to enhance productivity and achieve exceptional results in their projects.
Post time:Dec - 12 - 2024