Aluminum Oxide vs. Zirconia Flap Discs An In-Depth Comparison
In the world of abrasive materials, flap discs have become a staple for various grinding and finishing applications. Among the most popular materials used for these discs are aluminum oxide and zirconia. Each type offers unique properties, advantages, and disadvantages, making them suitable for different tasks. This article aims to provide an in-depth comparison of aluminum oxide and zirconia flap discs, helping users select the best option for their specific needs.
Composition and Structure
Aluminum oxide flap discs are made from a combination of aluminum oxide grains, a cost-effective and versatile abrasive material. This type of disc is generally bonded onto a flexible backing, which allows for a degree of flexibility in use. Zirconia flap discs, on the other hand, utilize zirconia alumina as the abrasive material. Zirconia grains are tougher and more durable, and they are commonly used in applications that require more aggressive material removal.
Abrasive Performance
When it comes to abrasive performance, zirconia flap discs have a clear advantage over aluminum oxide discs. Zirconia is known for its superior toughness and longevity, making it an ideal choice for heavy grinding tasks. Users often favor zirconia discs for applications on hard metals, such as stainless steel and high-carbon steels, where higher removal rates and longer life are needed. Aluminum oxide discs, while effective for lighter applications such as finishing and surface preparation, tend to wear out more quickly under aggressive grinding conditions.
Heat Resistance
Another significant factor to consider is heat resistance. Zirconia discs manage heat better than aluminum oxide discs. During grinding, friction generates heat, which can degrade the abrasive grain and negatively impact performance. Zirconia's tough grit design enables it to withstand higher temperatures, thus preserving its effectiveness over longer periods of use. Aluminum oxide discs, being less resistant to heat, may lose their cutting capabilities faster when used in prolonged or intensive applications.
aluminum oxide vs zirconia flap disc
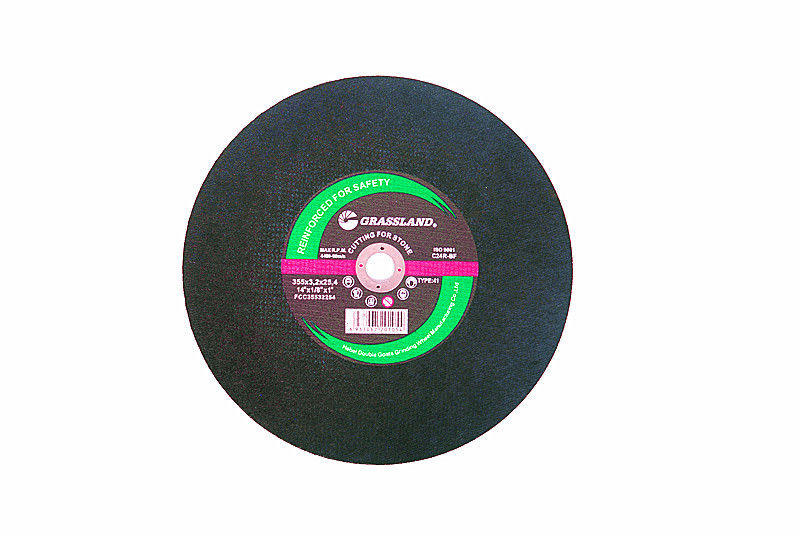
Cost Efficiency
Cost is always a consideration in any manufacturing or repair operation. Generally, aluminum oxide flap discs are more affordable than zirconia discs, making them a popular choice for budget-conscious buyers. They provide adequate performance for general-purpose tasks without necessitating a significant investment. However, in high-demand environments where durability and performance are paramount, the higher initial cost of zirconia discs can be justified by their longevity and efficiency, ultimately resulting in lower operational costs over time.
Application Suitability
When determining the right flap disc for a specific task, understanding the application is crucial. Aluminum oxide flap discs work well for tasks such as paint or rust removal, surface preparation, and light grinding on softer metals and wood. They are particularly suitable for DIY or occasional use where performance does not need to withstand heavy wear.
Conversely, zirconia flap discs excel in industrial settings or professional environments where materials are tough and time is of the essence. Their ability to handle aggressive grinding on stainless steel, cast iron, and other hard-to-grind materials makes them the go-to option for heavy machinery maintenance and metal fabrication industries.
Conclusion
In summary, both aluminum oxide and zirconia flap discs have their unique strengths and weaknesses. Aluminum oxide discs are cost-effective and suitable for lighter applications, while zirconia discs offer superior durability and performance for heavier tasks. Ultimately, the choice between the two materials should be guided by the specific requirements of the job, including the type of material being worked on, required abrasiveness, and budget constraints. By understanding the differences and applications of each type of flap disc, users can make informed decisions that enhance their efficiency and productivity in various grinding tasks.
Post time:Nov - 24 - 2024