Cutting Aluminum with an Angle Grinder A Comprehensive Guide
When it comes to fabrication and metalworking, aluminum is one of the most versatile materials available. Its lightweight properties, combined with resistance to corrosion, make it an essential component in various industrial applications. However, cutting aluminum can pose challenges, especially for those who rely on angle grinders for their metal cutting tasks. This article aims to provide valuable insights on how to effectively cut aluminum with an angle grinder.
Understanding Angle Grinders
Angle grinders are powerful handheld tools equipped with a rotating disc that can cut, grind, or polish various materials. Their versatility and efficiency make them popular choices for metal fabrication, woodworking, and construction. Angle grinders can handle a variety of attachments, and selecting the right one is crucial for successfully cutting aluminum.
Choosing the Right Disc
The first step in cutting aluminum with an angle grinder is selecting the appropriate cutting disc. A standard metal cutting disc may not be the best choice for aluminum, as it tends to clog and create excessive heat. Instead, opt for a blade specifically designed for cutting non-ferrous metals, such as those labeled as aluminum cutting discs or multi-purpose discs.
These specialized discs feature a unique design that helps prevent the metal from gumming up, allowing for smoother cuts. Additionally, use a disc with a higher tooth count to create finer cuts and reduce the likelihood of snagging.
Preparing the Workspace
Before you begin cutting aluminum, preparation is key to ensuring safety and achieving the desired results. Ensure that your workspace is clean and well-lit. Clear any clutter that could pose a hazard while you operate your angle grinder.
Secure your aluminum workpiece using clamps or a vice to prevent it from moving while you cut. This ensures not only your safety but also accuracy in your cuts. Always wear personal protective equipment (PPE), including safety glasses, gloves, and a dust mask. Aluminum particles can be sharp and pose risks to your health.
angle grinder cut aluminum
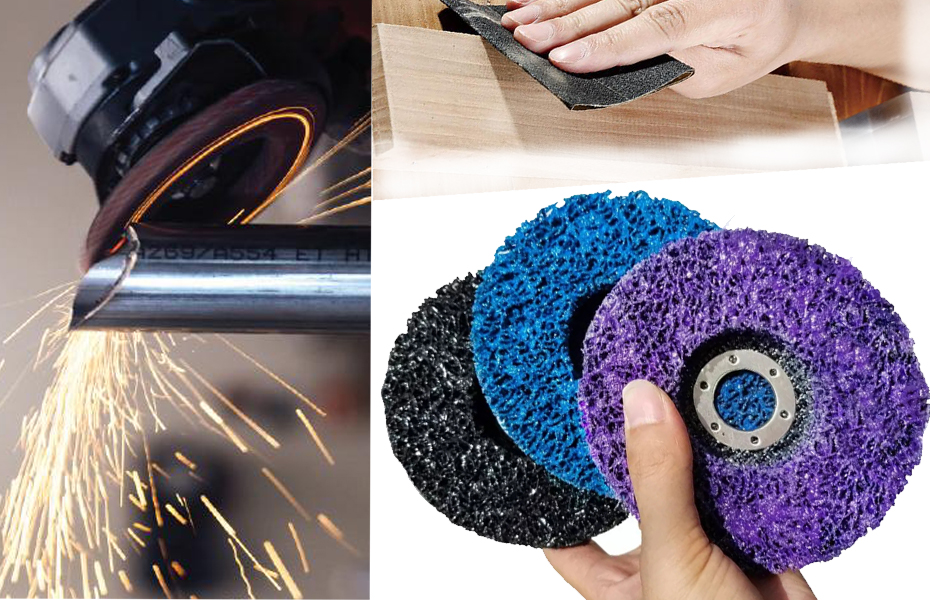
Cutting Techniques
When cutting aluminum with an angle grinder, maintain proper technique for optimal results. Begin by marking your cut line clearly using a marker or a scribe. This will guide you as you cut and help ensure accuracy.
Start the angle grinder and let the disc reach full speed before making contact with the aluminum. Use a gentle, steady pressure as you guide the grinder along the cut line. Avoid forcing the tool, as this can lead to uneven cuts, excessive heat, and premature wear of the cutting disc.
It's also important to maintain a consistent speed and angle while cutting. Adjust your grip to allow for better control and avoid twisting your wrist, which can lead to accidental miscuts.
Cooling the Material
Aluminum has a relatively low melting point compared to other metals, which means it can heat up quickly during the cutting process. Excessive heat can lead to warping or melting, compromising the integrity of your workpiece. To mitigate this, consider using a spray lubricant or cutting fluid designed for aluminum. This helps reduce friction, dissipate heat, and prolong the life of your cutting disc.
Finishing Touches
Once the cut is complete, you may notice sharp edges or burrs around the cut area. Use a flap disc or a deburring tool attached to your angle grinder to smooth these edges and ensure a clean finish. This step is particularly important if the cut aluminum will be handled or assembled as part of a larger project.
Conclusion
Cutting aluminum with an angle grinder can be a straightforward process if done correctly. By choosing the right disc, preparing your workspace, practicing proper cutting techniques, and taking the necessary safety precautions, you can achieve clean, accurate cuts. Whether you're a DIY enthusiast or a professional tradesperson, mastering the art of cutting aluminum with an angle grinder will significantly enhance your metalworking skills. So gear up, and take on your next aluminum project with confidence!
Post time:Dec - 04 - 2024