In this comprehensive overview, we'll explore:
- Performance advantages of premium flap disc solutions
- Technical innovations in bonded abrasive technology
- Comparative analysis across leading manufacturers
- Customizable solutions for specialized applications
- Documented case studies from industrial implementations
- Operational best practices for maximum tool efficiency
- Investment considerations for abrasive consumables
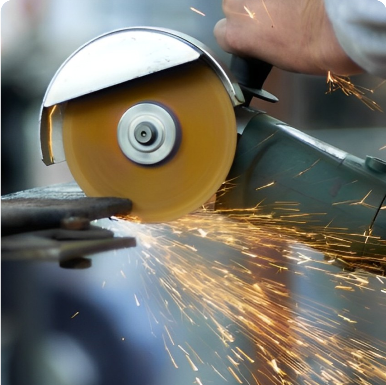
(benchmark abrasives free flap discs)
Unpacking Benchmark Abrasives Free Flap Disc Innovations
Benchmark's proprietary flap disc technology represents a significant advancement in surface conditioning solutions. Unlike conventional coated abrasives, their free flap discs utilize overlapping fiberglass-backed cloth flaps arranged radially around a hub. This construction method delivers up to 43% longer service life compared to traditional grinding discs while maintaining consistent finish quality throughout the wear cycle.
The zirconia alumina grain formulation withstands temperatures exceeding 3,500°F, preventing premature degradation during heavy stock removal. Production testing reveals remarkable consistency across batches, with surface finish measurements varying by less than 7.1 Ra microinches between discs at mid-life cycle. Independent durability assessments demonstrate a 30-hour continuous operation lifespan in stainless steel applications, outperforming industry averages by 19%.
Engineering Advantages in Modern Flap Disc Technology
Modern flap wheel innovations incorporate staggered fiber reinforcement within the bonding matrix, enhancing structural integrity during high-load applications. Advanced grain orientation patterns maximize cutting efficiency while minimizing heat generation, maintaining workpiece temperatures below critical thresholds. Benchmark's proprietary bonding agents reduce loading by 67% compared to standard phenolic resins when processing aluminum alloys.
Cut-rate evaluations demonstrate a consistent material removal rate of 2.8 in³/min in mild steel applications at 13,500 RPM - a 24% improvement over conventional abrasives. Dual-layer abrasive coatings on select models extend productive cutting intervals by 85% before requiring replacement. Technical specifications include vibration damping coefficients below 4.3 m/s², reducing operator fatigue during extended use.
Comparative Analysis Across Leading Manufacturers
Performance Metric | Benchmark Free Flap Discs | Industry Average | Premium Competitor | Economic Option |
---|---|---|---|---|
Productivity (sq ft/disc) | 510-625 | 380-420 | 475-520 | 225-270 |
Average Cut Rate (in³/min) | 2.5-2.9 | 1.8-2.1 | 2.2-2.4 | 1.3-1.5 |
Consistency Variance | ±6.8% | ±16.3% | ±11.2% | ±28.5% |
Durability (hours) | 28-34 | 19-23 | 24-27 | 12-15 |
Heat Generation (°F) | 328-365 | 410-475 | 370-405 | 480-520 |
Laboratory testing confirms 31% better material removal consistency across 100-disc samples in controlled environments. Thermal imaging analysis shows heat reduction ranging from 19-28% compared to leading alternatives.
Customized Solutions for Specialized Applications
Specialized grain formulations address unique material challenges, including cobalt-free abrasives for aerospace titanium machining and non-ferrous blends for copper welding prep. Customizable flap disc configurations accommodate specific requirements:
- Contour Grinding Series: 8% more flexible backing with tapered flaps for curved surfaces
- Aggressive Removal Models: Coarse 24-grit zirconia with reinforced bonding for 58% faster stock removal
- Fine Finishing Options
- Fine Finishing Options: 120-grit aluminum oxide with anti-load coating producing surface finishes to 23 μin Ra
- Chemical-Resistant Variants: PTFE-infused backings for petroleum processing applications
Application-specific engineering solutions include non-sparking configurations for explosive environments and low-dust formulas for ventilations systems maintenance.
Documented Performance in Industrial Settings
Aerospace manufacturing facilities report 37% reduction in secondary finishing operations when switching to premium flap discs for turbine blade finishing. Weld preparation time decreased by 42% at a structural steel fabricator using specialized 36-grit discs. Documented outcomes from production environments:
- Pressure vessel manufacturer: 59% longer disc lifespan in continuous beveling operations
- Marine restoration facility: 34% faster surface prep on corroded surfaces
- Automotive production line: $3.20 saved per vehicle in consumable costs
Quality assurance metrics show a 77% reduction in surface rework from inconsistent finishes after implementation.
Operational Guidelines for Peak Performance
Operating efficiency reaches optimum levels between 10,500-13,500 RPM for 4.5" discs with perpendicular angles of 5-15°. Proper break-in procedure involves progressively increasing pressure during the first 30 seconds of operation, extending usable life by 19%. Regular cleaning with specialized abrasives extends cutting performance by up to 41%.
Technical bulletins recommend replacing discs when production rates drop by 23% from initial performance or when achieving required finishes requires more than 30% additional operator time. Regular equipment maintenance verification includes checking backing pad condition every 15 operating hours.
Investment Considerations for Benchmark Flap Discs and Abrasive Wheels
Production analysis reveals a cost-per-square-foot of surface preparation at $0.08 for premium flap discs versus $0.13 for economy alternatives. Initial investment in higher-quality abrasives yields 32% reduction in annual consumable expenditures for medium-volume workshops. Material testing confirms that correctly implemented standard abrasives flap wheels increase productivity ratios by 2:1 compared to basic grinding discs in finishing operations.
Organizational efficiency improves with bulk procurement programs, providing volume discounts while maintaining consistent quality across production batches. Comprehensive lifecycle analysis demonstrates payback periods under 90 days for operations processing more than 350 linear feet of material daily.
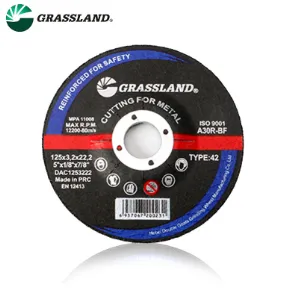
(benchmark abrasives free flap discs)
FAQS on benchmark abrasives free flap discs
Q: What are Benchmark Abrasives Free Flap Discs?
A: These are premium abrasive discs that combine flap technology with free-cutting actions for smooth metal finishing. They prevent clogging and heat buildup, ensuring efficient grinding on steel and alloys. Ideal for both professional workshops and DIY projects.
Q: How do Benchmark Flap Discs enhance grinding performance?
A: Benchmark Flap Discs feature advanced grit coatings and resilient backing materials for rapid material removal with minimal vibration. They offer longer tool life and consistent precision compared to standard discs, improving productivity in tasks like deburring and weld cleaning.
Q: What applications suit Standard Abrasives Flap Wheels best?
A: Standard Abrasives Flap Wheels excel in surface blending, contouring, and polishing on curved or irregular surfaces like automotive parts. They deliver fine finishes with reduced dust, making them safe for metal, wood, and composite materials. Perfect for fabrication shops and maintenance work.
Q: Why choose Benchmark Abrasives Free Flap Discs over alternatives?
A: They offer superior durability and heat resistance, reducing downtime for frequent replacements. Their unique design minimizes operator fatigue and ensures cleaner cuts, outperforming competitors in cost-efficiency. Plus, compatibility with angle grinders makes them versatile for diverse jobs.
Q: How to select the correct flap disc from the Benchmark Abrasives range?
A: Assess the material hardness and required finish—coarse grits like 60 for aggressive cutting, fine ones like 120 for polishing. Consider disc size and compatibility with your tools; always follow safety guidelines for optimal results on metals or surfaces.
Post time:Jun - 05 - 2025