Ceramic Flap Discs The Ultimate Tool for Precision Grinding
In the world of metalworking and surface finishing, achieving the highest quality and efficiency is essential. One tool that has gained significant popularity among professionals and DIY enthusiasts alike is the ceramic flap disc. Known for its superior performance, these discs combine the durability of ceramic abrasives with the flexibility and versatility of a flap design. In this article, we will explore the advantages, applications, and characteristics of ceramic flap discs, highlighting why they are a preferred choice for many grinding and finishing tasks.
What are Ceramic Flap Discs?
Ceramic flap discs are abrasive tools composed of overlapping layers, or flaps, made from ceramic grit. These flaps are attached to a backing plate, typically constructed from fiberglass or plastic, and are designed to perform various grinding and finishing operations. The unique design allows the disc to wear down evenly, maintaining its effectiveness throughout its lifecycle.
Advantages of Ceramic Flap Discs
1. Superior Durability One of the most significant advantages of ceramic flap discs is their durability. The ceramic abrasive is highly resistant to heat and wear, making it ideal for heavy-duty applications. Unlike traditional aluminum oxide discs, ceramic grits maintain their cutting properties longer, leading to more extended usage and reduced costs.
2. Cool Grinding Ceramic flap discs are designed to manage heat efficiently, preventing the material from burning or discoloring during the grinding process. This characteristic is particularly crucial when working with heat-sensitive materials, such as stainless steel or other alloys.
3. Versatility These discs can be used on various materials, including metals, wood, and plastics. Whether you're removing welds, deburring edges, or preparing surfaces for painting, ceramic flap discs are up to the task. Their versatility makes them an excellent addition to any toolkit.
ceramic flap disc
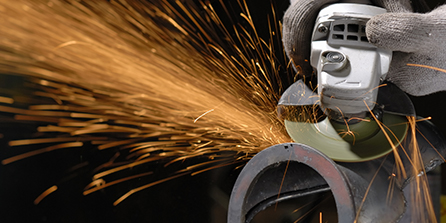
4. High Material Removal Rate Ceramic flap discs offer a superior material removal rate compared to other types of abrasives. The aggressive cutting action of the ceramic grit allows for fast and efficient stock removal, which can significantly speed up projects and improve productivity.
5. Enhanced Finish Quality The flexibility of the flaps allows for better conformability to the surface being worked on, resulting in a smoother finish. This is particularly beneficial when preparing surfaces for painting or polishing, as it minimizes the need for additional finishing steps.
Applications of Ceramic Flap Discs
Ceramic flap discs are widely used across various industries, including metal fabrication, automotive, construction, and woodworking. Their primary applications include
- Weld Grinding Perfect for removing weld seams and smoothing out joints on metal parts. - Deburring Efficiently eliminates sharp edges and burrs from manufactured components. - Surface Preparation Ideal for preparing surfaces before painting or coating, ensuring better adhesion and a smoother finish. - Stock Removal Effective in heavy material removal tasks, thanks to their aggressive cutting properties. - Finishing Operations Used for fine finishing on metals and other materials to achieve a polished look.
Choosing the Right Ceramic Flap Disc
When selecting a ceramic flap disc, factors such as grit size, disc diameter, and backing type should be considered. A finer grit is suitable for finishing applications, while a coarser grit is preferred for aggressive material removal. It is also important to choose the right disc diameter to fit your grinding tool effectively.
In conclusion, ceramic flap discs are a powerful and versatile tool for professionals and hobbyists alike. Their durability, efficiency, and high-quality finish make them an indispensable choice for a wide range of grinding and finishing tasks. Whether working with metal, wood, or synthetic materials, ceramic flap discs offer the ultimate solution to achieve the desired results with ease and precision.
Post time:Dec - 18 - 2024