The Essential Role of Cut-Off Wheels for Aluminum in Metalworking
Cut-off wheels are essential tools in the metalworking industry, specifically designed for the cutting and grinding of various materials. Among the array of metals that can be machined, aluminum stands out due to its favorable properties, including lightweight, corrosion resistance, and malleability. However, cutting aluminum requires specially designed cut-off wheels to achieve the best results without causing damage to the material or the tool itself.
Understanding Cut-Off Wheels
Cut-off wheels, also known as abrasive discs, are typically made from a composite of materials that can include aluminum oxide, silicon carbide, or diamond grains. Each type of material has its specific application and effectiveness based on the material being cut. Aluminum, being a softer metal compared to steel, demands a wheel that can precisely slice through it without overheating or causing burrs.
When selecting a cut-off wheel for aluminum, it's crucial to consider several factors, including wheel composition, thickness, diameter, and RPM rating. Wheels designed for cutting softer metals like aluminum usually feature a higher concentration of abrasive grains and softer bonding agents. This configuration allows for faster cutting speeds and reduced friction, minimizing the risk of the wheel binding to the surface of the metal.
Benefits of Using the Right Cut-Off Wheel for Aluminum
1. Precision Cutting The primary advantage of using a cut-off wheel specifically made for aluminum is the precision it offers. These wheels are engineered to produce clean cuts, reducing the chance of jagged edges or deformation during the cutting process. This is particularly important for projects that require tight tolerances and high-quality finishes.
2. Reduced Heat Generation One of the significant challenges when cutting aluminum is the risk of melting or warping due to heat buildup. Cut-off wheels designed for aluminum typically have a cooling effect due to their composition and design, allowing for quicker cuts while managing the thermal load effectively.
3. Longer Tool Life Using the appropriate cut-off wheel can significantly extend the lifespan of both the wheel and the tool it’s mounted on. This is not only cost-effective but also enhances productivity as fewer wheel replacements are needed.
4. Versatility Many cut-off wheels are versatile enough to also handle other materials, including certain plastics and light metals; this makes them a valuable addition to any metalworker's toolkit.
cut off wheel aluminum
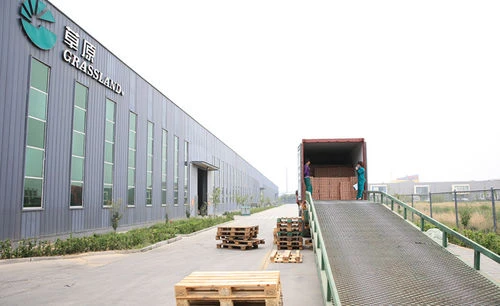
Tips for Efficient Cutting
When using cut-off wheels for aluminum, there are several best practices that can help ensure efficient and clean cuts
- Speed Control Always ensure you are operating at the correct RPM for the specific wheel and machine. Lower speeds can help mitigate heat buildup, while appropriate speeds enhance performance.
- Light Pressure Applying too much pressure can cause the wheel to break or become damaged. It’s best to apply light, steady pressure to allow the wheel to do the cutting effectively.
- Keep it Lubricated Using lubricants or cutting fluids can further reduce heat and assist in making smoother cuts.
- Proper Mounting Ensure the cut-off wheel is securely mounted and properly aligned to avoid vibrations and safety hazards during operation.
Safety Considerations
While using cut-off wheels, safety should always be a priority. Always wear appropriate personal protective equipment (PPE), such as goggles, gloves, and dust masks, to protect against flying debris and dust. Regularly inspect cut-off wheels for any signs of damage or wear, and replace them as necessary to maintain a safe working environment.
Conclusion
Cut-off wheels for aluminum are an integral part of metalworking that significantly enhances cutting efficiency and quality. Understanding their composition, application, and proper usage can lead to improved outcomes in projects, reduced operational costs, and advance safety standards. Whether in industrial settings or hobbyist workshops, investing in the right tools for the job will always pay dividends in productivity and finished product quality.
Post time:Dec - 24 - 2024