Understanding Cutting Wheels for Metal An Essential Tool in Metalworking
In the vast world of metalworking, one of the most pivotal tools is the cutting wheel. These wheels, essential for a variety of applications, are engineered specifically to slice through metals with precision and efficiency. Understanding the types, materials, and applications of cutting wheels can greatly enhance a metalworker's capabilities.
What Is a Cutting Wheel?
A cutting wheel, often referred to as a cut-off wheel, is a flat, circular disk that is mounted on a power tool, typically an angle grinder or a chop saw. Designed explicitly for cutting, these wheels are made from durable materials, including abrasives such as aluminum oxide, silicon carbide, and diamond. Each type of cutting wheel serves a specific purpose, and the choice largely depends on the material being cut and the desired outcome.
Types of Cutting Wheels for Metal
1. Abrasive Cutting Wheels These are the most common type of wheels used in metalworking. They consist of abrasive particles bonded together, providing a rough surface that can grind through various metals. Available in different grits, they are suitable for cutting steel, stainless steel, and non-ferrous metals.
2. Diamond Cutting Wheels These wheels are embedded with diamond particles, making them incredibly durable and efficient for cutting hard materials such as cast iron, concrete, and certain alloys. Their longer lifespan and ability to produce less heat during cutting make them a favorite in industrial settings.
3. Thin Cutting Wheels Designed for precision cutting, these wheels are thinner than standard grinding wheels, allowing for smaller kerfs, which minimizes material loss. Thin wheels are ideal for detailed work and can be used effectively on metals like stainless steel and aluminum.
Factors to Consider When Choosing a Cutting Wheel
cutting wheel metal
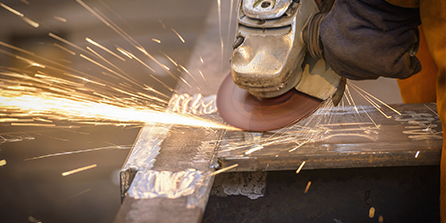
1. Material Compatibility It is crucial to select a cutting wheel that is compatible with the type of metal you intend to cut. Using the wrong wheel can lead to inefficient cutting and potential damage.
2. Wheel Thickness Thicker wheels are more durable and can withstand more pressure but are less effective for intricate cuts. In contrast, thin wheels provide precision but may wear out faster.
3. RPM Ratings Each cutting wheel is rated for a maximum RPM (revolutions per minute). Exceeding this rating can lead to catastrophic failures, so it's vital to ensure that the wheel's RPM rating matches or exceeds the speed of your tool.
4. Safety Features Look for cutting wheels that are designed with safety in mind. Reinforced designs and those with safety ratings can reduce the risk of accidents and injuries during operation.
Best Practices for Using Cutting Wheels
Using cutting wheels effectively requires adherence to safety guidelines and best practices. Always wear appropriate personal protective equipment (PPE), including goggles, gloves, and hearing protection. Before starting, inspect the wheel for cracks or damage and ensure that it is properly mounted. Work at a consistent speed and apply even pressure to avoid overheating and premature wear of the wheel.
Additionally, maintaining a clean workspace free of obstructions can help prevent accidents. Regularly check the cutting angle and technique to ensure maximum effectiveness and safety.
Conclusion
Cutting wheels are indispensable tools in metalworking, offering versatility and efficiency for a range of applications. By understanding the different types of wheels available, considering key factors when choosing the right wheel, and following best practices during usage, metalworkers can enhance their craftsmanship and ensure safety in their work environment. As with any tool, the right knowledge and preparation will lead to successful projects and satisfied results.
Post time:Nov - 16 - 2024