Different Shapes of Grinding Wheels
Grinding wheels are indispensable tools in various industrial applications, including metalworking, construction, and woodworking. They come in various shapes and sizes to perform diverse tasks, from removing material to enhancing surface finishes. Understanding the different shapes of grinding wheels is vital for choosing the right tool for specific grinding needs.
1. Straight Wheels
Straight wheels are the most commonly used grinding wheels. They feature a simple cylindrical design and are typically mounted on a spindle. These wheels are ideal for general grinding applications, including surface grinding, tool grinding, and cylindrical grinding. The straight shape allows for efficient material removal, and the wheels can be easily shaped and profiled to meet specific requirements.
2. Depressed Center Wheels
Depressed center wheels, also known as cutoff wheels or grinding discs, are characterized by their flat surfaces and slightly recessed centers. This design allows for more cutting surface, making them suitable for grinding, cutting, and finishing materials, especially in tight spaces and corners. They are commonly used in angle grinders and are ideal for working with metals and concrete.
3. Cup Wheels
Cup wheels are shaped like a cup and are designed for heavy material removal. They are particularly effective for grinding and shaping concrete and masonry surfaces. The open design of cup wheels allows for efficient dust removal, enhancing visibility during the grinding process. These wheels are often used in construction and renovation projects, as they can quickly flatten large surfaces.
4. Flaring Cup Wheels
different shapes of grinding wheel
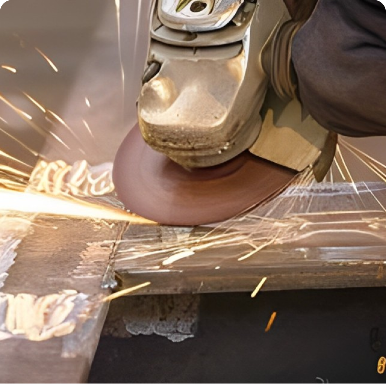
Flaring cup wheels have a design that combines the features of both straight and cup wheels. With a flared shape, these wheels provide a larger surface area for grinding while being effective for grinding and finishing applications. They are often used for grinding the surface of various materials, including metals and hard alloys. Their versatile design allows them to perform well in a range of applications.
5. Mounted Points
Mounted points are small grinding wheels that are usually mounted on a spindle. They come in various shapes, such as cones, cylinders, and discs, and are ideal for intricate work, such as deburring, shaping, and polishing small parts. Mounted points are widely used in jewelers' and metalworking shops, where precision is crucial.
6. Segmented Wheels
Segmented wheels feature a segmented design, which allows for improved thermal management during grinding. These wheels consist of several segments bonded together, providing a more aggressive grinding action. Segmented wheels are typically used for heavy-duty applications, such as grinding concrete, asphalt, and other hard materials. Their design helps reduce glazing and ensures a longer lifespan.
7. Diamond Wheels
Diamond grinding wheels are unique in that they are embedded with industrial diamonds, making them highly effective for grinding hard materials, such as ceramics, glass, and composite materials. They offer superior cutting ability and can provide a fine finish on challenging surfaces. Diamond wheels are often used in specialized applications, including tool sharpening and precision grinding.
Conclusion
The diverse shapes of grinding wheels cater to various industrial needs, enhancing efficiency and precision in grinding tasks. From the simplicity of straight wheels to the specialized functions of diamond wheels, each shape serves its unique purpose. Selecting the right grinding wheel shape is crucial for achieving the desired results and maintaining productivity in operations. Understanding these different shapes not only empowers users to make informed decisions but also contributes to achieving optimal performance in their grinding applications. Whether in metalworking, construction, or woodworking, the right grinding wheel shape can make a significant difference in the quality and efficiency of the work performed.
Post time:Dec - 12 - 2024