Different Types of Abrasives Used in Grinding Wheels
Grinding wheels are essential tools in the manufacturing and metalworking industries, playing a critical role in shaping, finishing, and polishing materials. The performance of a grinding wheel is significantly determined by the type of abrasive used. Abrasives can be broadly categorized into two types natural and synthetic, each with unique properties and applications. Understanding these abrasives helps to select the right grinding wheel for specific tasks, ensuring efficiency and effectiveness in the grinding process.
Natural Abrasives
Natural abrasives are sourced from minerals and geological formations. Historically, they have been used for centuries in various grinding applications. Common natural abrasives include
1. Sand Often found in nature, sand is predominantly made of silicon dioxide. It is commonly used in lower-grade grinding applications and can be utilized in sandpaper and abrasive blasting.
2. Corundum A crystalline form of aluminum oxide, corundum is one of the hardest natural abrasives available. It is often found in different grades, including emery, which contains iron oxide. Corundum is used in grinding wheels for a variety of metals, making it a versatile choice for general-purpose grinding.
3. Diamond Although often considered synthetic due to its current predominant use in industrial applications, natural diamonds were historically used in grinding. They are the hardest known material and are utilized in grinding applications where extreme precision is necessary, such as in the machining of ceramics and hard steels.
Synthetic Abrasives
different types of abrasives used in grinding wheels
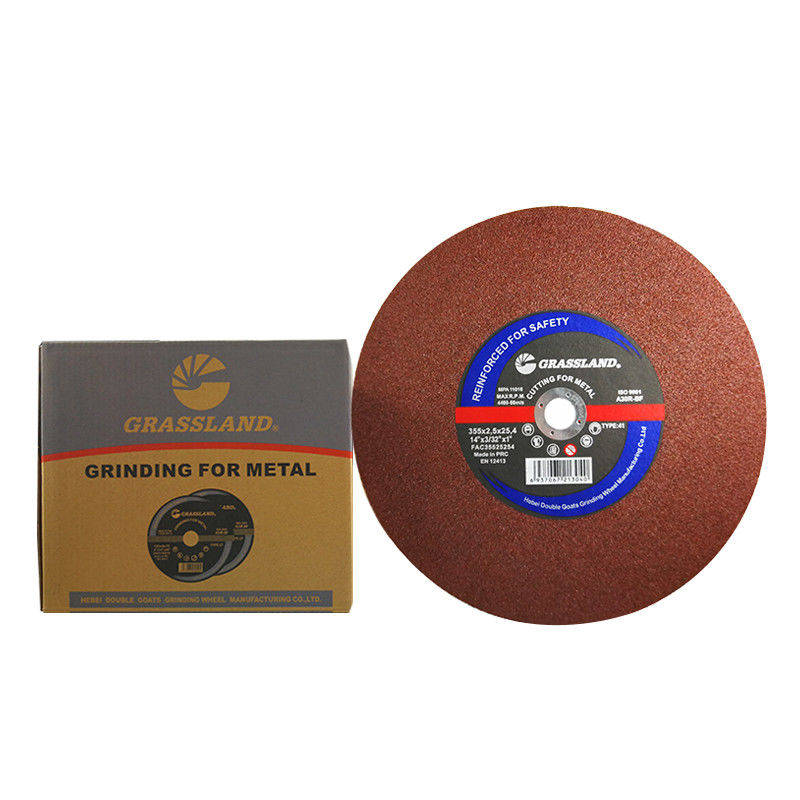
Synthetic abrasives have gained popularity due to their engineered properties, which can be tailored to specific grinding applications. These abrasives are manufactured using various chemical processes, producing consistent and high-performance materials. Key synthetic abrasives include
1. Aluminum Oxide This common synthetic abrasive is made by the fusion of bauxite and other materials. It is available in different types, such as White Aluminum Oxide and Brown Aluminum Oxide. White Aluminum Oxide provides a fine finish, while Brown Aluminum Oxide is more durable and used in heavy stock removal operations. Its versatility makes aluminum oxide a favorite for grinding ferrous metals as well as non-ferrous materials like aluminum.
2. Silicon Carbide Known for its hardness and carborundum structure, silicon carbide is a favored choice for grinding materials such as glass, ceramics, and hard plastics. It is also used in applications where a finer finish is required. Due to its high wear resistance, silicon carbide is popular in the manufacturing of grinding wheels designed for wet or dry applications.
3. Cubic Boron Nitride (CBN) CBN is the second hardest material known and is primarily used in grinding high-speed steel and hard materials. Unlike diamond, CBN retains its grinding ability at high temperatures, making it ideal for grinding ferrous materials. CBN wheels are often employed in industrial settings where precision and durability are paramount.
4. Diamond Abrasives While natural diamonds are rare, synthetic diamond abrasives have revolutionized the grinding and polishing industries. Used extensively in stone cutting, jewelry manufacturing, and ultra-precision machining, synthetic diamond grinding wheels offer exceptional wear resistance and cutting performance.
Choosing the Right Abrasive
Selecting the appropriate abrasive for a grinding wheel depends on various factors, including the material being machined, the required finish, and the grinding conditions. For instance, aluminum oxide is suitable for general metalworking, while silicon carbide may be chosen for softer materials like plastic and glass. CBN and diamond abrasives are preferable in applications that require precision and the ability to handle high temperatures.
In conclusion, understanding the different types of abrasives used in grinding wheels is essential for maximizing efficiency and achieving desired outcomes in manufacturing processes. With advancements in both natural and synthetic abrasives, the grinding industry continues to evolve, providing versatile solutions to meet the demands of various industries. The careful selection of grinding wheels based on abrasive types ensures that manufacturers can effectively tackle their cutting and finishing operations.
Post time:Dec - 12 - 2024