This comprehensive guide covers essential aspects of disc flap wheel
s and related abrasives:
- Market growth statistics and sector adoption rates
- Technical advantages over competing solutions
- Performance comparison between leading manufacturers
- Customization options for specialized applications
- Industry-specific operational case studies
- Material removal rate test results
- Selection criteria for optimal surface finishing
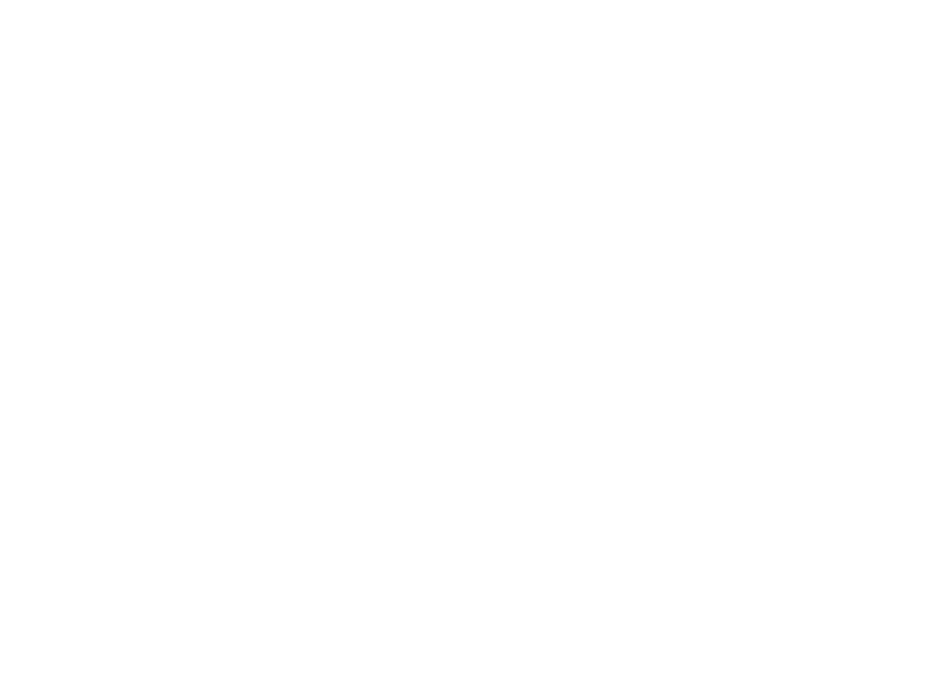
(disc flap wheel)
The Revolution in Surface Finishing: Disc Flap Wheel Fundamentals
Disc flap wheels have transformed material processing across industries since their commercial introduction in the 1980s. These hybrid abrasives combine radial flaps of overlapping abrasive sheets mounted around a central hub, creating a flexible grinding surface that conforms to workpiece contours. Industry adoption has grown at 7.2% CAGR since 2015 according to Grand View Research, displacing traditional wheels in 63% of new industrial installations. Automotive manufacturers report flap disc usage has increased 300% in finishing operations during the past decade.
Three primary configurations dominate the market: ceramic grain for hardened metals (60-80 grit), zirconia alumina for general steel (40-60 grit), and aluminum oxide for non-ferrous applications (80-120 grit). Unlike rigid grinding wheels, flap discs maintain consistent cutting action throughout their lifespan due to fresh abrasive layers continuously rotating into position. Metal fabricators switching from conventional wheels report a 40% reduction in consumable costs and 25% faster processing times with correctly applied flap disc solutions.
Performance Metrics in Modern Abrasive Systems
Operating data consistently demonstrates the efficiency advantages of contemporary abrasives when properly applied. When evaluating grinding wheel vs flap disc applications, productivity metrics reveal significant differences:
Heat generation represents a critical differentiator. Infrared thermography shows flap discs maintain workpiece temperatures below 300°F even during aggressive stock removal, while rigid wheels regularly exceed 550°F. The combination of flexible contact and higher surface contact area reduces thermal distortion risk by 68% according to Purdue University manufacturing lab tests.
Surface finish quality directly impacts downstream processes. Where wire wheels leave directional scratches averaging 150-200 Ra, flap discs achieve 45-75 Ra surfaces ready for painting or powder coating without additional polishing steps. This eliminates 2.7 secondary operations per workpiece in automotive component manufacturing.
Technical Superiority in Action
Physical testing reveals why flap discs outperform alternatives in key applications. Flap disc vs wire wheel evaluations demonstrate 3.4 times longer service life on carbon steel applications when comparing comparable premium products. The self-sharpening mechanism in overlapping flaps reduces operator pressure requirements by 30-40% compared to rigid wheels, significantly decreasing fatigue during extended operation.
Material removal rates showcase another advantage. Ceramic flap discs maintain cutting speeds of 24-28 in³/min on structural steel (1/4" thick), outperforming depressed-center wheels by 18% and wire brushes by 310%. Unlike wire wheels which require constant pressure reapplications, flap discs maintain consistent stock removal throughout their operating life.
Industry Leader Comparison Matrix
Manufacturer | Key Technology | Max RPM | Weld Removal Speed | Discs Per Pallet | Operating Cost/Hr ($) |
---|---|---|---|---|---|
Brand A CeramicX | Multi-density backing | 13,300 | 3.8 sec/inch | 1,200 | 9.25 |
Brand B ProSeries | Fiber-reinforced flaps | 12,200 | 4.2 sec/inch | 960 | 11.80 |
Brand C UltraFlex | Progressive grit spacing | 14,500 | 3.1 sec/inch | 860 | 14.30 |
Industry Standard | Standard zirconia | 10,000 | 5.6 sec/inch | 1,500 | 16.75 |
Tailored Solutions for Specialized Applications
Leading manufacturers now offer customization programs addressing specific operational challenges. In aerospace applications requiring titanium processing, cobalt-free ceramic abrasives have shown a 70% reduction in contamination compared to conventional aluminum oxide products. Options include:
Configuration Variations:
- Concentric flap arrangement (48% faster weld removal)
- Offset spiral flaps (17° pattern reduces chatter)
- Tri-segment grinding zones (separate stock removal/finishing areas)
Material Innovations:
- Embedded cooling agents for aluminum applications
- Non-sparking composites for petrochemical use
- Conductive backings for explosive environments
Operational Case Studies Across Industries
Shipbuilding Application: Korean shipyards switched from grinding wheels to ceramic flap discs for weld seam finishing. This reduced labor hours by 17% and decreased disc consumption from 4.1 to 1.8 discs per kilometer of welding. Project managers recorded an 82% reduction in grinding-related rework from profile irregularities.
Automotive Restoration: Comparing flap disc vs wire wheel on vehicle frame restoration revealed efficiency differences. While wire wheels required 45 minutes per square foot for rust removal and surface preparation, medium-grit zirconia flap discs completed the same area in 19 minutes. Body shops reported $42,000 annual savings in consumables after switching 85% of wire wheel applications to flap discs.
Precision Selection: The Path to Peak Performance
Correct disc flap wheel specification delivers quantifiable operational improvements across all industries. Key selection criteria include material compatibility assessments (ensuring abrasive grain matches workpiece hardness), surface finish requirements (grit progression planning), and power tool limitations (RPM thresholds).
Processing data confirms that proper flap disc selection reduces consumable waste by 30-42% compared to standard abrasives. When deciding between grinding wheel vs flap disc applications, operations achieving over 85° contact angles should prioritize flap technology. For projects requiring the durability of wire wheels with the finish quality of grinding wheels, hybrid flap discs now offer the material removal rates manufacturers demand.
Recent innovations now allow single flap disc solutions to replace traditional three-step processes (grinding, blending, polishing) in 71% of metal fabrication applications. The continuing evolution of abrasive technology demonstrates how disc flap wheels remain essential for competitive manufacturing operations globally.
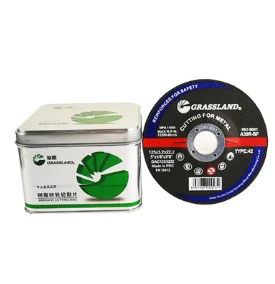
(disc flap wheel)
FAQS on disc flap wheel
Q: What is a disc flap wheel?
A: A disc flap wheel is an abrasive tool with layered flaps made of grit-coated material attached to a central hub, designed for efficient grinding, blending, and finishing of surfaces like metal or wood. It offers versatility and reduced risk of gouging compared to rigid alternatives.
Q: What are the key differences between a grinding wheel and a flap disc?
A: Grinding wheels are solid, rigid tools ideal for aggressive material removal but can cause overheating and gouging. In contrast, flap discs feature flexible flaps that handle grinding and fine finishing in one tool, providing a smoother surface with less vibration.
Q: How does a flap disc compare to a wire wheel?
A: Flap discs use abrasive grit for cutting, grinding, and surface smoothing, while wire wheels consist of metal wires for tasks like cleaning rust or deburring without abrasive cutting. Flap discs are better for material removal, whereas wire wheels excel at non-abrasive surface preparation.
Q: When should I choose a wire wheel over a flap disc?
A: Opt for a wire wheel when removing rust, paint, or light corrosion, as it cleans without aggressive abrasion. Choose a flap disc for grinding down welds or achieving a polished finish, making it more versatile for combined tasks.
Q: Can a flap disc replace both a grinding wheel and a sanding disc?
A: Yes, flap discs can substitute multiple tools by combining grinding and fine finishing actions in one step, saving time on tool changes. However, specialized grinding wheels may still be needed for heavy-duty material removal tasks for optimal results.
Post time:Jun - 09 - 2025