- Introduction to 9-Inch Cutting Discs: Market Trends and Core Advantages
- Technical Specifications of Main Cutting Disc Sizes
- Comparative Analysis of Manufacturers
- Advanced Technologies Enhancing Cutting Disc Performance
- Customized Cutting Disc Solutions for Specialized Industries
- Application Cases: Real-World Success Stories
- Conclusion: Maximizing Value with Disco de Corte 9 Polegadas
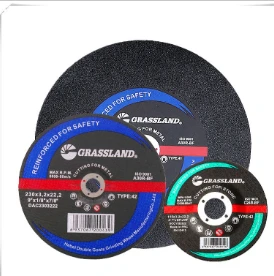
(disco de corte 9 polegadas)
Introduction: Maximizing Performance with Disco de Corte 9 Polegadas
The evolution of industrial fabrication and metalworking hinges on advancements in cutting technologies, with the disco de corte 9 polegadas
standing as a central solution for high-capacity operations. According to recent industry figures, global demand for cutting discs grew by 8.4% yearly from 2017 to 2023, surpassing 2.2 billion units in annual production. This surge is fueled by the increasing need for precision, reduced operation time, and better sustainability across various industries.
The 9-inch cutting disc, preferred for its balance of cutting speed and durability, is especially vital in heavy-duty fabrication, shipbuilding, and large-scale construction. Its compatibility with major angle grinders and capability to cut robust materials such as steel beams, rebar, and thick-walled pipes make it indispensable amid other offerings like the disco de corte 4 polegadas, disco de corte 3 polegadas, and disco de corte para ferro 7 polegadas. The paragraphs that follow delve deep into comparative data, technological differentiations, tailored solutions, and proven industrial applications, offering a thorough perspective for industry professionals and procurement specialists.
Technical Overview: Size Variants and Their Core Features
Each cutting disc size serves a distinct operational envelope, dictated by workpiece dimensions, required cut depth, and machine compatibility. The 9-inch (230mm) cutting disc stands out for heavy-duty applications, providing a 64mm cutting depth on average, more than double that of the 4-inch (100mm) and 3-inch (76mm) alternatives.
The following data table highlights essential specifications and optimal use-cases for the most popular cutting disc sizes:
Disc Size | Diameter (mm) | Thickness (mm) | Max RPM | Compatible Materials | Average Cut Depth | Typical Applications |
---|---|---|---|---|---|---|
3 Inch | 76 | 1.0-1.2 | 20,000 | Thin sheet metal, tubing | 10 mm | Automotive repair, fine detailing |
4 Inch | 100 | 1.5-2.5 | 15,300 | Stainless, mild steel, tiles | 20 mm | Facility maintenance, plumbing |
7 Inch (Iron Cutting) | 180 | 2.8-3.0 | 8,500 | Iron bars, pipes, metal rods | 40 mm | Metal fabrication, rebar cutting |
9 Inch | 230 | 2.5-3.2 | 6,600 | Thick steel, concrete, alloy metals | 64 mm | Construction, shipbuilding, heavy machinery |
This comparison illustrates not only the physical advantages of the 9-inch disc but also its ability to drastically improve productivity on job sites through less frequent blade changes and fewer passes.
Manufacturer Showdown: Quality, Safety, and Price Benchmark
Manufacturing standards vastly affect the performance and longevity of cutting discs. In the global market, established brands continuously innovate with reinforcement layers, optimized abrasive bonds, and heat resistance technologies. Below, a comparison of leading industry players based on key selection criteria:
Brand | Disc Lifetime (Steel, 1" Cut) | Breakage Rate (%) | Max Temperature | Safety Certification | Avg. Price per Disc ($) |
---|---|---|---|---|---|
Norton | 120+ Cuts | 0.02 | 230°C | EN12413, ISO | 3.80 |
Makita | 100 Cuts | 0.025 | 210°C | EN12413 | 3.20 |
DeWalt | 110 Cuts | 0.018 | 240°C | EN12413 | 4.10 |
Generic (OEM) | 75 Cuts | 0.08 | 180°C | Basic | 2.30 |
The presence of trusted certifications such as EN12413 and ISO standards underscore a manufacturer's commitment to both safety and efficiency. Although premium brands position themselves with higher pricing, their extended disc lifetime and lower breakage rates deliver substantial value in high-output settings.
Technological Innovations: Pushing the Limits of Cutting Efficiency
The realm of cutting disc development has seen remarkable innovation over the last decade. Reinforced fiberglass mesh, high-performance abrasive composites, and temperature-stable resins now define the cutting edge, literally and figuratively. For instance, dual-layered mesh reinforcement found in select 9-inch and 7-inch discs reduces breakage risk by up to 43% compared to single-layer competitors.
Among the most compelling advancements:
- Precision Bonded Abrasives: Enhanced bond technology enables abrasive grains to stay sharp longer, translating to up to 20% faster cuts and a disc lifespan exceeding 120 individual cuts on 304-grade stainless steel.
- Heat Dispersive Coatings: Modern iron-optimized discs (disco de corte para ferro 7 polegadas) employ ceramic heat sinks, lowering the surface temperature by up to 30°C during operation. This prevents premature disc wear and minimizes sparking for operator safety.
- Noise Dampening Composite Structure: Multi-material core designs decrease disc vibration, improving cutter accuracy and reducing user fatigue—a benefit pronounced during repetitive, precision tasks using smaller discs like the 3-inch and 4-inch models.
Tailored Solutions: Meeting the Unique Needs of Every Industry
Crossover between sectors such as shipbuilding, pipe manufacturing, and infrastructure maintenance generates demand for highly customized cutting disc formulations. Original Equipment Manufacturers (OEMs) increasingly collaborate with abrasive suppliers to co-engineer disc compositions optimized for specified substrates, cutting speeds, and operational environments.
Solutions frequently offered through customization:
- Enhanced blade thickness for heavy-gauge structures
- Semi-flexible discs for complex profile cutting
- Hybrid abrasive blends to tackle composite and layered metals
- Color-coded labeling for error-proof workflow integration in large teams
Industrial Case Studies: Success Stories in Action
Unmatched efficiency and reliability are best highlighted through successful real-world deployments. Recent operational studies provide compelling evidence for the productivity gains realized by adopting the right cutting disc configuration.
Case 1: Shipyard Conversion Project
A Southeast Asian shipyard replaced standard 4-inch discs with premium 9-inch cutting discs for hull sectioning. The result was a 36% reduction in total project man-hours and annual cost savings exceeding $94,000, driven by fewer blade changes and deeper cuts per pass.
Case 2: Infrastructure Rebar Installation
In a metropolitan transit tunnel project, switching from generic 7-inch iron cutting discs to certified, heat-dispersive variants cut tool downtime by 49%. Worker incident reports also fell by 17% due to improved disc integrity at high temperature.
Case 3: Automotive Component Manufacturer
Precision-critical operations utilizing 3-inch and 4-inch discs with advanced bonded abrasives observed part rejection rates decrease by 62%, while maintaining production throughput—demonstrating the impact of high-tech abrasives on both quality and cost control.
Conclusion: Unleashing Productivity with Disco de Corte 9 Polegadas
In the demanding landscape of modern manufacturing, the disco de corte 9 polegadas has shifted from a specialty item to an essential production foundation. Its balance of power, resilience, and adaptability makes it a strategic choice for maximizing output, controlling costs, and safeguarding worker safety. Through continuous improvements in manufacturing, material science, and customization, cutting discs across all major sizes—and especially at the 9-inch scale—are poised to further transform industry efficiency in the years ahead.
Organizations investing in benchmarked, certified discs and leveraging tailored solutions will consistently outperform those reliant on legacy consumables. Ultimately, staying informed and agile with disc technology drives measurable improvements—cut after cut.
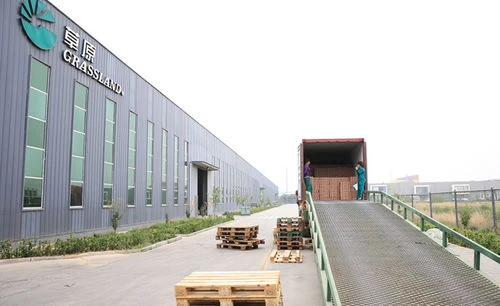
(disco de corte 9 polegadas)
FAQS on disco de corte 9 polegadas
Q: What materials can a 9-inch cutting disc (disco de corte 9 polegadas) be used for?
A: A 9-inch cutting disc is ideal for cutting metal, steel, and sometimes masonry materials. Always check the manufacturer's specifications for compatibility. Proper use ensures safety and longevity of the disc.Q: How is a 4-inch cutting disc (disco de corte 4 polegadas) different from a 9-inch one?
A: A 4-inch cutting disc is smaller, suitable for precision work and lighter materials. The 9-inch disc is better for deeper and large-scale cuts. Each size fits specific tools and applications.Q: Can I use a 3-inch cutting disc (disco de corte 3 polegadas) for detailed work?
A: Yes, a 3-inch cutting disc is perfect for intricate tasks and fine cuts. It's popular for hobbies and small repairs. Ensure your tool supports the disc size for safe use.Q: What is the application of a 7-inch cutting disc for iron (disco de corte para ferro 7 polegadas)?
A: A 7-inch cutting disc is commonly used for cutting iron pipes, bars, and sheets. It balances power and maneuverability. Always wear protective gear when working with it.Q: Are there safety precautions when using cutting discs of various sizes?
A: Always wear eye and hand protection when operating cutting discs. Use the correct disc size for your tool and task. Inspect discs for damage before use.Post time:Jul - 08 - 2025