The Essential Guide to Cutting Discs for Iron Features, Applications, and Best Practices
In the realm of metalworking and construction, cutting discs have become indispensable tools for professionals and hobbyists alike. One such tool that stands out is the cutting disc for iron, designed specifically to tackle the challenges posed by ferrous materials. This article aims to provide an overview of iron cutting discs, their features, applications, and best practices for usage.
Understanding Cutting Discs
Cutting discs, also known as cutting wheels or blades, are circular tools used in conjunction with angle grinders and other cutting machines. They are made from a combination of abrasive materials that are engineered to slice through various metals, including iron. Iron cutting discs are typically distinguished by their durability, precision, and ability to withstand high operating speeds.
Features of Cutting Discs for Iron
Iron cutting discs generally have a few common features that enhance their performance
1. Material Composition Most iron cutting discs are made from abrasive materials such as aluminum oxide or silicon carbide. These materials provide the necessary hardness and grit to effectively cut through iron without damaging the tool.
2. Thickness The thickness of the cutting disc often ranges from 1mm to 3mm, depending on its intended use. Thinner discs are ideal for quick, precise cuts, while thicker discs are better suited for heavier-duty applications.
3. Size Variations Cutting discs come in various diameters, typically ranging from 115mm to 400mm. The size of the disc should be chosen based on the specifications of the angle grinder and the requirements of the job.
4. Speed Rating Each disc is rated for maximum speed, which is crucial for safe operation. It’s essential to use a cutting disc that matches the speed rating of the grinder to avoid accidents.
Applications of Iron Cutting Discs
Iron cutting discs are versatile tools used in a multitude of applications
1. Metal Fabrication These discs are frequently employed in workshops to cut metal sheets, bars, and pipes. They provide clean, accurate cuts which significantly reduce material waste.
disco de cortar hierro
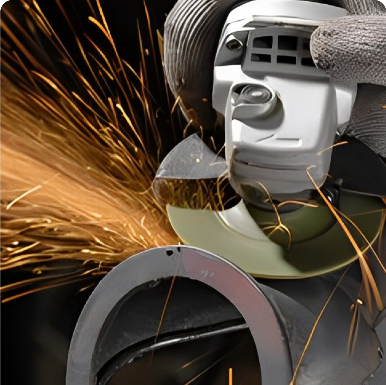
2. Construction In construction projects, cutting discs are used to prepare and modify structural elements, making them suitable for various applications.
3. Repairs and Maintenance Professionals often rely on iron cutting discs for performing repairs where metal components need precise sizing and fitting.
4. Artistic Applications Artists and hobbyists utilize cutting discs to create intricate metal sculptures and designs, demonstrating the versatility of these tools in creative projects.
Best Practices for Using Iron Cutting Discs
To ensure safety and efficiency when using iron cutting discs, consider the following best practices
1. Wear Protective Gear Always wear appropriate personal protective equipment, including safety goggles, gloves, and hearing protection, to safeguard against flying debris and loud noise.
2. Check Equipment Compatibility Ensure that the cutting disc is compatible with the angle grinder regarding size and speed rating. Using incompatible equipment can lead to accidents.
3. Use Proper Technique Maintain a steady hand and consistent pressure while cutting. Avoid forcing the disc, which can lead to breakage and reduce the quality of the cut.
4. Inspect the Disc Prior to use, inspect the disc for any cracks, warping, or other signs of damage. Discard any damaged discs to prevent injury.
5. Cool Down Allow the cutting disc to cool if you notice it becoming excessively hot. Overheating can lead to premature wear or failure of the disc.
Conclusion
Iron cutting discs are essential tools in a wide range of industries, offering precision and efficiency in metal cutting tasks. Understanding their features, applications, and proper usage can significantly enhance performance and safety in every cutting project. As technology continues to evolve, the performance and capabilities of these discs are likely to improve, ensuring they remain vital for metalworking in the future.
Post time:Dec - 05 - 2024