Understanding the Importance of Cutoff Wheels for Polishers
In the world of metalworking and machining, the right tools make all the difference. Among these tools, cutoff wheels for polishers, also referred to as polishing discs, hold significant importance. These specialized wheels are designed to facilitate the precise cutting, grinding, and finishing of various materials, making them indispensable in workshops and industrial settings.
Cutoff wheels are typically made from durable materials such as aluminum oxide, zirconia, or diamond particles. The choice of material influences the wheel’s effectiveness, longevity, and the types of jobs it can handle. For instance, aluminum oxide wheels are well-suited for softer metals and provide excellent balancing between performance and cost. On the other hand, diamond wheels are preferred for cutting hard materials like ceramic or concrete, as they exhibit exceptional durability and cutting efficiency.
One of the primary advantages of using cutoff wheels is their ability to deliver clean, burr-free cuts. This is particularly important in metalworking, where the quality of the cut can significantly affect the overall aesthetics and functionality of the finished product. Polishing discs minimize the need for additional finishing processes, saving time and increasing productivity.
Moreover, the use of these wheels impacts safety — using the correct type of cutoff wheel not only enhances performance but also minimizes the risk of accidents. Wheels that are not suited for a particular application may fracture or break during use, potentially causing injury. Therefore, it is crucial to select the right cutoff wheel based on the material type and thickness, the tool's speed, and the desired finish.
Types of Cutoff Wheels
Cutoff wheels for polishers come in various sizes and thicknesses, allowing users to choose the most appropriate one for their specific tasks. For precision applications, thinner wheels are preferable as they produce less heat, reducing the risk of warping or damaging the workpiece. In contrast, thicker wheels are more suited for aggressive cutting tasks, where durability and longevity are prioritized over precision.
disco de corte de pulidora
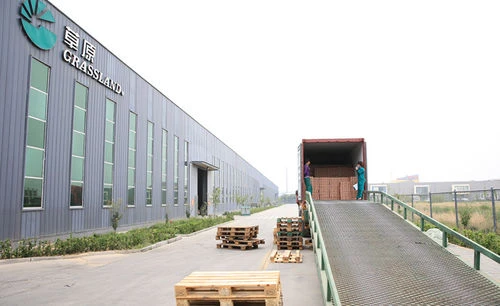
Furthermore, these wheels can be classified based on their bonding agents resin-bonded, metal-bonded, or vitrified. Resin-bonded wheels are the most common due to their flexibility and ability to withstand high speeds, making them ideal for general-purpose cutting and polishing. Metal-bonded wheels, designed for tougher applications, are more rigid and suitable for heavy-duty cutting tasks. Vitrified wheels, while less common, offer excellent stability and performance, particularly in intricate tasks.
Application in Various Industries
The versatility of cutoff wheels extends across numerous industries, including automotive, aerospace, construction, and metal fabrication. In the automotive sector, they are employed for cutting and grinding brake rotors and other components. In aerospace, they assist in preparing components made from lightweight yet hard materials, ensuring precision remains paramount.
Moreover, the construction industry benefits from these wheels during the installation and finishing of various materials. Whether it's the cutting and shaping of tiles or the precision finishing of metal supports, cutoff wheels are essential tools that enhance productivity and safety.
Conclusion
In conclusion, cutoff wheels for polishers play a crucial role in achieving precision and efficiency in various machining and metalworking tasks. Their diverse applications, coupled with advancements in material technology, continue to improve their functionality and performance. When selecting a cutoff wheel, understanding its specifications, suitable applications, and safety measures can lead to better results and increased productivity. As the industry evolves, the importance of using the right tools, like cutoff wheels, remains timeless, directly influencing the quality of work produced.
Post time:Dec - 12 - 2024