Understanding Fillet Weld Flap Discs A Comprehensive Guide
Fillet weld flap discs are essential tools in metalworking and fabrication industries, known for their efficiency in weld preparation and finishing. With the growing need for precision and high-quality finishes, understanding the application and benefits of fillet weld flap discs is crucial for welders and metal fabricators alike.
What Are Fillet Weld Flap Discs?
Fillet weld flap discs are a specific type of abrasive disc, designed primarily for use on angle grinders. They consist of multiple layers or flaps of abrasive material that are bonded to a backing plate. The flaps are usually made of materials like aluminum oxide or zirconia, which are selected for their durability and cutting efficiency. These discs are particularly effective for smoothing out the surfaces of welds, removing slag, and preparing edges for additional welding or finishing.
Applications of Fillet Weld Flap Discs
The main applications of fillet weld flap discs can be summarized as follows
1. Weld Preparation Before welding, it is essential to clean and prepare the metal surfaces. Fillet weld flap discs can be used to remove rust, scale, and old paint, ensuring a clean surface for better weld penetration.
2. Weld Finishing After welding, the surface may be uneven or contain imperfections. Flap discs enable fabricators to grind down these irregularities, providing a smooth finish that enhances both aesthetics and structural integrity.
3. Deburring The sharp edges left by cutting or welding processes can be hazardous. Flap discs effectively deburr these edges, making the finished product safer and more visually appealing.
4. Contouring and Shaping When working with irregular surfaces or shapes, flap discs can be manipulated to match contours, allowing for detailed and intricate work.
Choosing the Right Fillet Weld Flap Disc
Selecting the appropriate flap disc for a specific task is essential to achieving optimal results. When choosing a fillet weld flap disc, consider the following factors
fillet weld flap disc
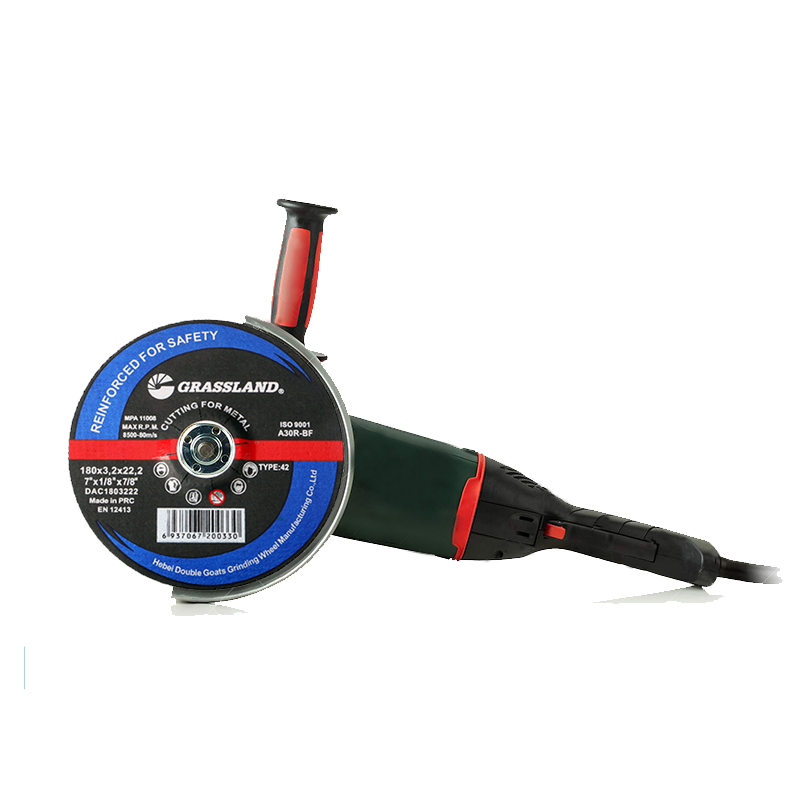
- Abrasive Material Different materials offer varying levels of durability and cutting speed. Zirconia discs, for example, provide more durability and are ideal for harder metals, while aluminum oxide is more suited for softer materials.
- Grit Size Flap discs come in various grit sizes, from coarse to fine. Coarse grits remove material more aggressively, while finer grits are ideal for finishing. Selecting the right grit size is crucial for the desired finish.
- Disc Diameter The size of the flap disc should match the angle grinder being used. Common sizes include 4.5, 5, and 7. Larger discs cover more surface area and can be more efficient for extensive surface preparation.
- Backing Plate The backing material contributes to the overall flexibility and durability of the flap disc. A flexible backing plate allows for better adaptability to contours, while rigid plates are better for flat surfaces.
Best Practices for Using Fillet Weld Flap Discs
To maximize the efficiency and lifespan of fillet weld flap discs, follow these best practices
- Use Appropriate Speed Ensure that the speed setting on the angle grinder matches the specifications of the disc. Using too high a speed can lead to premature wear and tear.
- Maintain Proper Pressure Applying too much pressure can cause overheating and rapidly wear down the disc. Instead, allow the abrasive flaps to do the work with moderate pressure.
- Keep Disc Cool Overheating can affect the performance of the abrasive material. Periodically reducing pressure or lifting the disc off the surface can help keep temperatures low.
- Work Safely Always wear appropriate personal protective equipment, such as gloves, goggles, and masks, to prevent injury from flying debris and dust.
Conclusion
Fillet weld flap discs are indispensable tools for anyone involved in metalworking and fabrication. Their versatility in application, combined with the ability to achieve high-quality finishes, makes them a go-to solution for weld preparation, finishing, and shaping. By understanding how to choose and effectively use these discs, fabricators can enhance their productivity while producing exceptional results. With advancements in abrasive technology, the range of options available continues to grow, ensuring that there is a flap disc suitable for every metalworking task.
Post time:Dec - 02 - 2024