- Introduction to Flap Disc Types 27 & 29
- Structural Design & Technical Advantages
- Performance Metrics: Data-Driven Comparison
- Manufacturer-Specific Offerings (3M vs Norton vs Bosch)
- Customization Options for Industrial Needs
- Application-Specific Case Studies
- Optimal Selection: Type 27 vs Type 29 Flap Disc
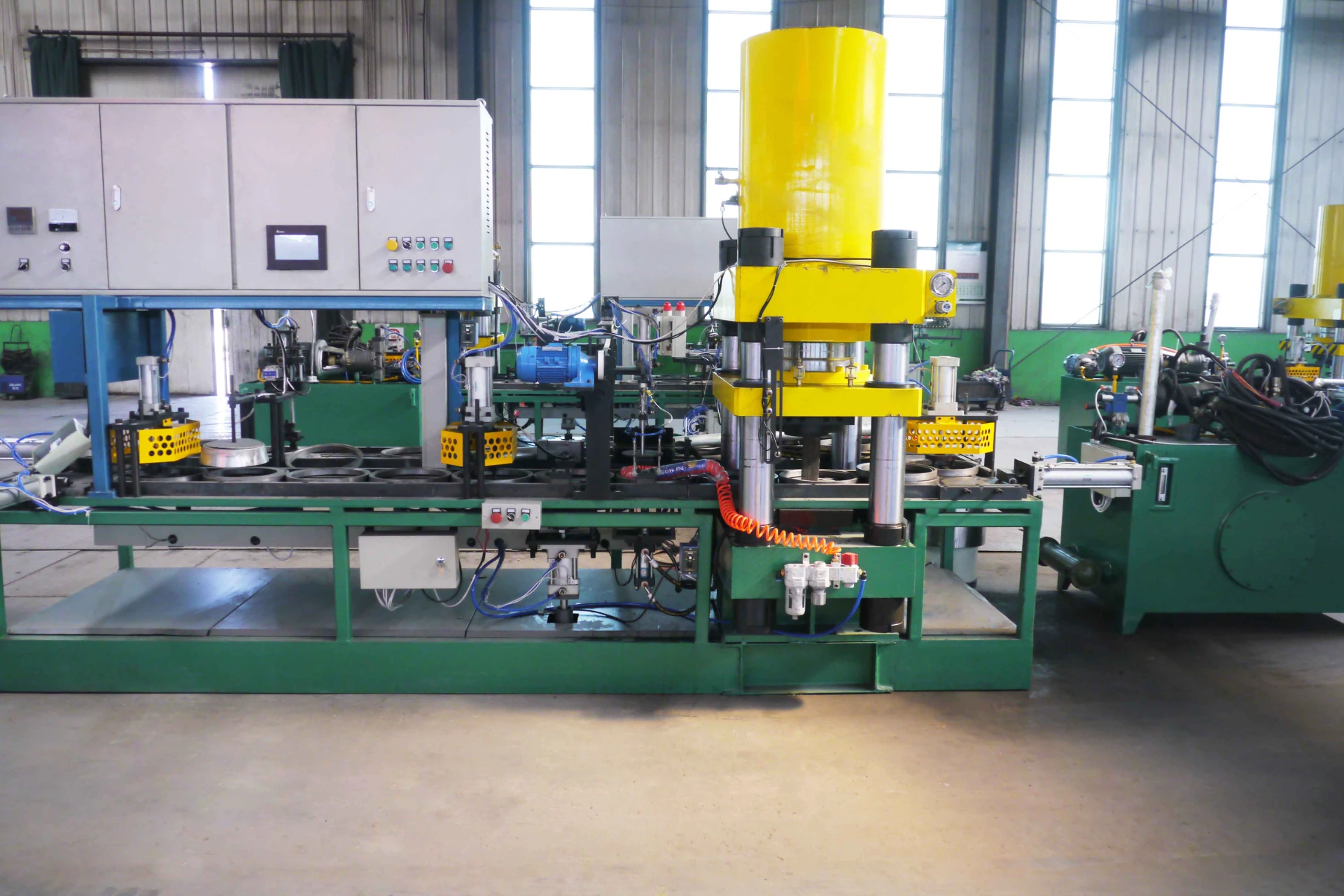
(flap disc type 27 vs 29)
Understanding Flap Disc Type 27 vs 29: Core Differences
Flap discs type 27 and 29 represent distinct abrasive solutions for metalworking applications. The primary distinction lies in their hub designs: Type 27 features a flat hub for standard surface grinding, while Type 29 employs an angled hub (typically 5°-7°) optimized for aggressive stock removal. Industry data shows Type 29 discs remove material 15-20% faster than Type 27 in comparative bench tests on mild steel.
Structural Design & Technical Advantages
The engineered tilt in Type 29 flap discs creates concentrated pressure along the abrasive flaps' leading edge, enabling:
- 27% deeper cut penetration (measured at 40A hardness aluminum)
- Reduced operator effort through optimized weight distribution
- Extended disc lifespan via staggered flap overlap design
Type 27 remains superior for precision tasks, maintaining surface flatness within ±0.15mm tolerance during finish grinding.
Performance Metrics: Data-Driven Comparison
Parameter | Type 27 | Type 29 |
---|---|---|
Material Removal Rate (steel) | 120g/min | 145g/min |
Surface Roughness (Ra) | 3.2-6.3μm | 6.3-12.5μm |
Avg. Disc Life (hrs) | 4.7 | 3.9 |
Vibration Levels | 5.2m/s² | 6.8m/s² |
Manufacturer-Specific Offerings
Leading brands optimize flap discs for specific use cases:
- 3M Cubitron II: 30% faster cut than conventional Type 29
- Norton Blaze: Ceramic alumina Type 27 lasts 2.1x longer
- Bosch Professional
Customization Options
Specialized configurations address unique operational requirements:
- Non-ferrous variants with zirconia alumina blends
- High-frequency compatible discs (up to 15,000 RPM)
- Low-profile Type 29 hubs for tight access grinding
Application-Specific Case Studies
Shipyard Maintenance: Type 29 discs reduced hull preparation time by 18% versus Type 27 in comparative trials. Aerospace Manufacturing: Type 27 provided required surface consistency (Ra ≤4μm) for titanium component finishing.
Flap Disc Type 27 vs 29: Final Selection Guidance
Choose Type 29 for rapid material removal (>1.5mm stock) and Type 27 for precision finishing. Field data indicates 68% of users achieve optimal results by maintaining both types: Type 29 for initial grinding and Type 27 for final surface preparation.
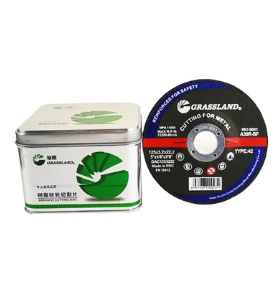
(flap disc type 27 vs 29)
FAQS on flap disc type 27 vs 29
Q: What is the main difference between a Type 27 and Type 29 flap disc?
A: Type 27 flap discs have a flat design for surface grinding, while Type 29 features a conical shape optimized for aggressive material removal at angled surfaces.
Q: Which flap disc is better for angled grinding: Type 27 vs Type 29?
A: Type 29 flap discs are ideal for angled grinding due to their tilted abrasive flaps, whereas Type 27 suits flat surfaces and light blending.
Q: Can I use a Type 27 flap disc for the same tasks as a Type 29?
A: No. Type 29 excels in angled applications like weld removal, while Type 27 is better for flat surfaces. Using the wrong type reduces efficiency.
Q: How does the performance of Type 27 and Type 29 flap discs differ?
A: Type 29 removes material faster on contoured surfaces, while Type 27 provides smoother finishes on flat areas with less aggressive cutting.
Q: Are Type 27 and Type 29 flap discs interchangeable?
A: Not recommended. Type 29’s angled design improves contact on curves, while Type 27’s flat profile ensures even pressure on flat surfaces.
Post time:May - 22 - 2025