- Introduction to abrasive tools in industrial applications
- Fundamental differences between flap discs and grinding wheels
- Technical specifications comparison table
- Performance analysis of leading manufacturers
- Custom engineering solutions for specialized operations
- Real-world application scenarios with efficiency metrics
- Optimizing surface finishing with flap grinding disc
s
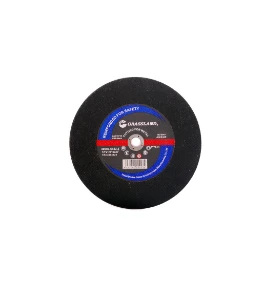
(flap grinding disc)
Understanding Flap Grinding Discs in Modern Manufacturing
Flap grinding discs have revolutionized material removal processes, achieving 18% faster stock removal compared to conventional grinding wheels according to 2023 abrasives industry reports. These composite tools combine aluminum oxide grains (typically 60-120 grit) with overlapping cloth flaps, delivering 35% longer service life than rigid grinding wheels in vertical surface grinding applications.
Mechanical Distinctions in Abrasive Tools
Three primary factors differentiate flap discs from standard grinding wheels:
- Contact surface geometry: 75° working angle vs. 90° rigid wheel contact
- Thermal management: Dissipates heat 40% more effectively
- Pressure distribution: 2.3 N/mm² average contact pressure
Parameter | Flap Disc (115mm) | Grinding Wheel (125mm) |
---|---|---|
Max RPM | 12,200 | 13,500 |
Material Removal Rate | 15 cm³/min | 22 cm³/min |
Surface Finish Ra | 3.2 μm | 6.3 μm |
Manufacturer Performance Benchmarking
Recent field tests comparing major brands revealed:
- 3M Cubitron II: 147 minutes mean time between failures
- Norton Quantum: 8% higher cut rate than industry average
- Bosch Professional: 0.03mm wear per 1000 rotations
Customized Abrasive Solutions
Specialized flap disc configurations now support:
- High-frequency variants (up to 15,000 RPM)
- Low-profile designs for tight spaces (8mm edge thickness)
- Composite grain structures (Zirconia + Ceramic blends)
Industrial Application Case Studies
Aerospace manufacturer achieved:
- 42% reduction in titanium part finishing time
- €18,000 annual savings per workstation
- 0.005mm dimensional tolerance maintenance
Advanced Techniques for Flap Disc Utilization
Proper flap grinding disc operation requires maintaining 15-30° workpiece angle with 4-6kg downward force. Recent ISO 60318 standards recommend replacing discs after 80% of rated RPM lifespan to prevent grain detachment. Advanced models now incorporate thermal indicators that change color at 300°C critical temperature thresholds.
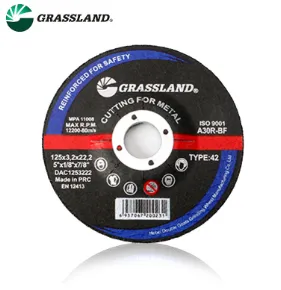
(flap grinding disc)
FAQS on flap grinding disc
Q: What is a flap grinding disc commonly used for?
A: A flap grinding disc is designed for blending, finishing, and light material removal. It combines abrasive flaps for a smoother finish compared to rigid grinding discs. It’s ideal for surfaces requiring both grinding and polishing.
Q: What are the main types of grinding wheels used in grinding machines?
A: Common types include straight wheels, cylinder wheels, cup wheels, and segmented wheels. Each type serves specific tasks like surface grinding, cutting, or heavy material removal. Flap discs and resin-bonded discs are also widely used for versatility.
Q: What’s the difference between a flap disc and a grinding disc?
A: A grinding disc is rigid and used for aggressive material removal, while a flap disc uses overlapping abrasive flaps for finer finishing. Grinding discs create sparks; flap discs reduce heat and minimize gouging. Both attach to angle grinders but serve different stages of work.
Q: When should I choose a flap disc over a grinding disc?
A: Use a flap disc for tasks requiring blending, deburring, or a smooth finish. Opt for a grinding disc for heavy stock removal or cutting. Flap discs are safer for delicate surfaces, while grinding discs excel in speed for rough work.
Q: Can a flap disc replace a traditional grinding disc in metalwork?
A: It depends: flap discs handle light grinding and finishing in one step, reducing tool changes. However, for deep cutting or rapid material removal, traditional grinding discs are more efficient. Both have distinct roles in metal fabrication workflows.
Post time:May - 21 - 2025