Understanding Flap Discs The Versatile Tool for Metalworking
In the realm of metalworking, efficient and effective tools are essential for achieving high-quality results. One such tool that has gained immense popularity is the flap disc, particularly the 125mm variant. Flap discs are favored for their versatility in grinding, blending, and finishing surfaces, making them indispensable in industries ranging from manufacturing to automotive repair.
What is a Flap Disc?
A flap disc consists of multiple overlapping pieces of abrasive material, which are arranged in a fan-like formation around a central hub. This design allows for a greater surface area to be in contact with the workpiece, facilitating faster material removal while providing a smooth finish. The 125mm size is particularly popular due to its manageable dimensions, making it suitable for hand-held and stationary grinders alike.
Applications of Flap Discs
The applications of flap discs are varied and extensive. They can be used on metal, wood, plastic, and even stone, making them highly versatile in machining operations. Flap discs excel in tasks such as
1. Grinding The primary use of flap discs is for grinding materials down. The layered abrasive flaps help in removing material efficiently and uniformly, reducing the risk of uneven surfaces.
2. Blending Once the initial grinding is complete, flap discs can be used to blend the edges of different materials. This process is critical for creating seamless transitions between welded or joined sections.
3. Finishing A flap disc can provide a polished finish that is often desired in various projects. By choosing a finer grit, operators can achieve a smoother surface that enhances the aesthetic appeal of metalwork.
4. Deburring Post-manufacturing, many parts will have sharp edges or burrs. Flap discs quickly and effectively remove these imperfections, ensuring that parts are safe and ready for use.
flap disc 125
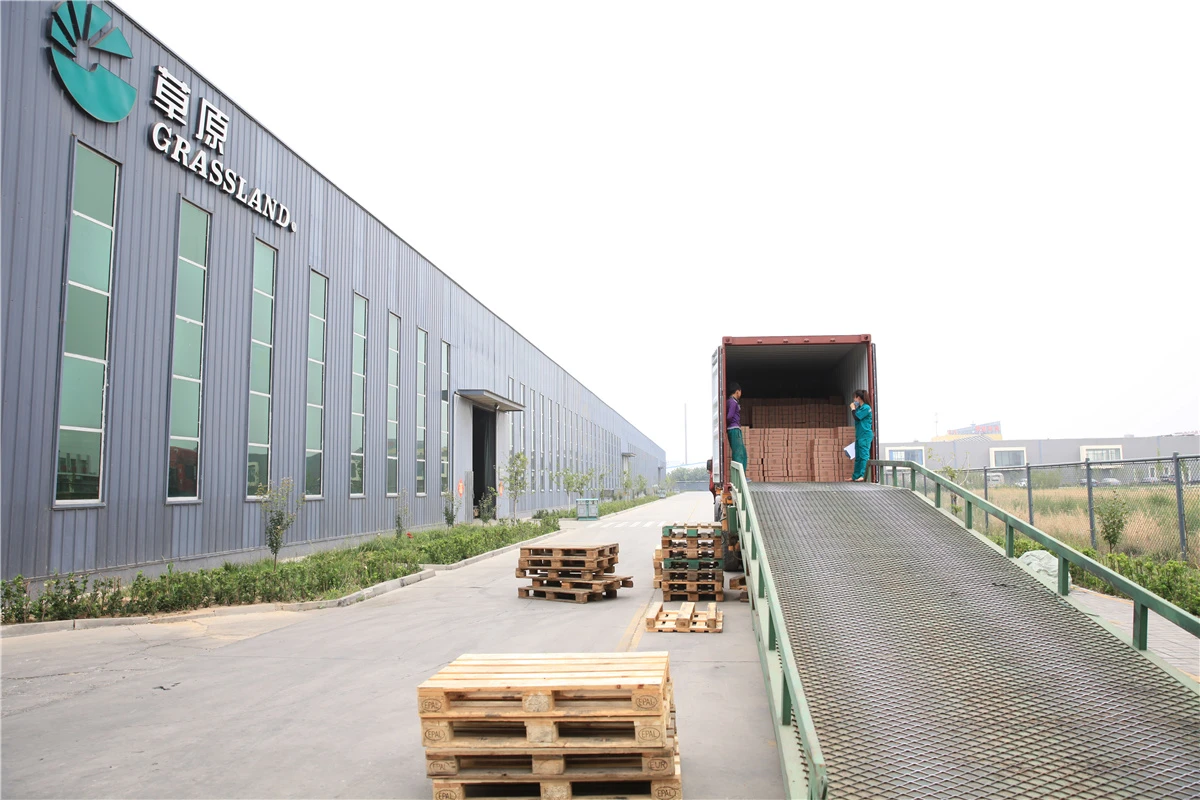
Choosing the Right Flap Disc
Selecting the appropriate flap disc is crucial for optimal performance. Factors to consider include
- Grit Size The grit size of the disc determines its abrasiveness. Coarser grits (e.g., 40-60) are suitable for heavy material removal, while finer grits (e.g., 120-240) are ideal for finishing and polishing tasks.
- Material Flap discs are available in various materials such as aluminum oxide, zirconia, and ceramic. Each material has its own advantages, with ceramic being particularly effective for tough materials due to its durability and heat resistance.
- Backing Type Flap discs may have different backing types, including fiberglass and plastic. Fiberglass backing is more robust and suitable for heavy applications, while plastic is lighter and may be used for more delicate tasks.
Safety Considerations
When using flap discs, safety should be a priority. Operators must wear appropriate personal protective equipment (PPE) such as eye protection, gloves, and a dust mask. It is also essential to ensure that the flap disc is compatible with the grinder in use and to follow the manufacturer's specifications to prevent accidents and maximize tool life.
Conclusion
Flap discs, particularly the 125mm variant, are integral tools in the metalworking industry, offering versatility and efficiency that cater to a range of applications. Their ability to grind, blend, and finish surfaces makes them a favorite among professionals and DIY enthusiasts alike. By understanding the characteristics of flap discs and how to choose the right one for your project, you can enhance your efficiency and the quality of your work. Whether you are a seasoned metalworker or a hobbyist, incorporating flap discs into your toolkit will undoubtedly elevate your craftsmanship.
Post time:Dec - 19 - 2024