Understanding Flap Discs The Versatile Tool for Metalworking
Flap discs are an essential tool in the arsenal of metalworkers, welders, and fabricators. Known for their versatility and effectiveness, these discs offer unique advantages over traditional grinding wheels and sanding pads. Among various types and specifications, flap discs marked as “40” typically indicate their grit size, which is a vital consideration in achieving the desired finish on different materials.
What Are Flap Discs?
Flap discs consist of multiple overlapping flaps of abrasive material, typically made from aluminum oxide or zirconia, attached to a central hub. These flaps are arranged in a manner that allows for efficient material removal while providing a smooth finish. Flap discs come in various sizes and shapes, but the most common are the conical and flat profiles. Each design caters to different applications and user preferences.
The Significance of Grit Size
When discussing flap discs, the grit size is a crucial specification. For instance, a flap disc labeled “40” signifies a coarse grit designed for aggressive material removal. This level of abrasiveness makes it ideal for initial grinding and leveling operations on rough surfaces. A 40 grit flap disc is typically employed for tasks like removing welds, shaping metal components, and preparing surfaces for further finishing work.
Applications of 40 Grit Flap Discs
The 40 grit flap disc finds its utility in various applications across different industries
1. Welding Preparation Before welding new materials, a 40 grit disc can effectively remove rust, paint, or any contaminants from the surface, ensuring a clean and strong weld.
2. Metal Fabrication In the fabrication process, fabricators often use this disc to shape and grind down metal components, providing them with the desired contours and dimensions.
flap disc 40
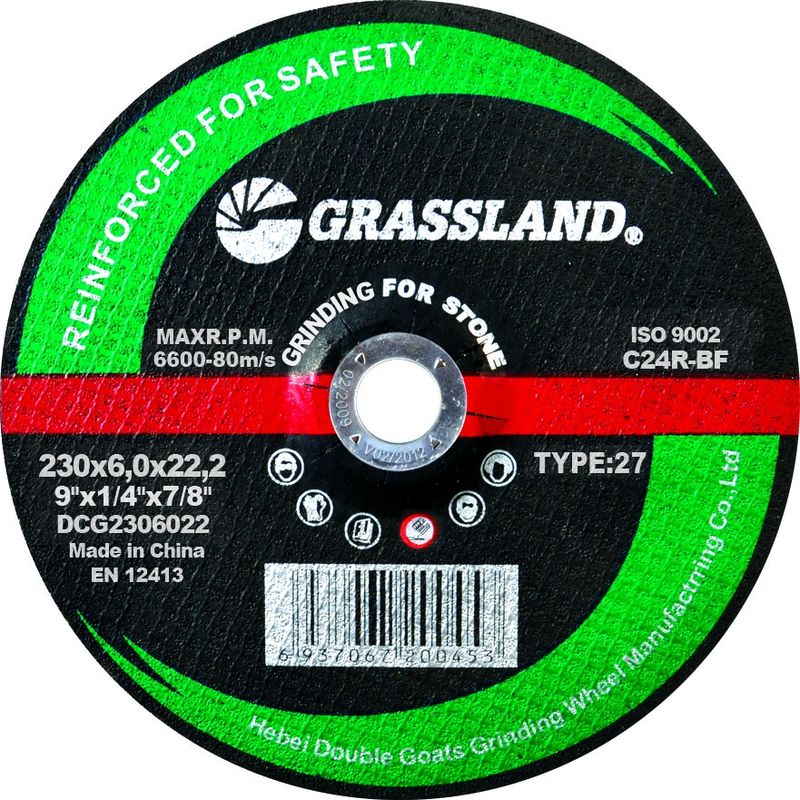
3. Surface Finishing While often utilized for aggressive grinding, a 40 grit flap disc can also be used for preliminary surface finishing, setting the stage for finer grit discs to achieve a smooth finish.
4. Automotive Industry In auto bodywork, these discs are invaluable for stripping paint and preparing metal for repairs or repainting, making it a favored choice among mechanics and bodywork specialists.
Advantages of Using Flap Discs
Flap discs present several advantages over traditional grinding methods. One significant benefit is their ability to perform both grinding and finishing tasks without the need to switch tools. This feature enhances efficiency and productivity in metalworking, saving time on projects.
Moreover, the design of flap discs allows for better heat dissipation, reducing the risk of overheating both the tool and the workpiece. This characteristic leads to longer tool life and improved surface integrity.
Choosing the Right Flap Disc
When selecting a flap disc, users should consider not only the grit size but also the material of the abrasive, the type of backing, and the specific application. For instance, while a 40 grit flap disc may be efficient for heavy tasks, finer discs are available for finishing applications that require a more polished result.
Conclusion
In conclusion, flap discs, particularly those with a grit size of 40, serve as dynamic tools in the metalworking industry. Their ability to combine aggressive grinding capabilities with finishing options sets them apart from traditional tools. As industries continue to evolve and demand more efficient, effective solutions, flap discs will undoubtedly remain a staple in workshops across the globe. Whether for welding preparation, surface finishing, or metal fabrication, a 40 grit flap disc is an invaluable asset, enabling professionals to achieve high-quality results with precision and ease.
Post time:Dec - 04 - 2024