Understanding Flap Discs An Essential Tool for Abrasive Grinding
Flap discs, particularly the widely used 4.1-inch variety, are integral to various grinding and finishing applications, ranging from metal fabrication to woodworking. These versatile tools consist of overlapping abrasive flaps that are adhered to a central backing, creating a design that combines grinding and polishing capabilities. The use of flap discs has seen significant growth in the industrial sector due to their effectiveness, efficiency, and user-friendly nature.
What are Flap Discs?
Flap discs come in various diameters, with the 4.1-inch size being favored for both handheld and stationary tools. These discs are designed to meet different grinding and finishing requirements, making them suitable for a wide range of materials including metals, wood, and plastics. The flaps themselves are typically made from aluminum oxide, zirconia, or ceramic, which are chosen based on the material being worked on and the desired finish.
The unique design of flap discs enables them to operate in a cooler manner compared to traditional grinding wheels. This is particularly important in applications where heat buildup can compromise the integrity of the material or lead to warping. The layered construction allows for even wear, prolonging the life of the tool and reducing the necessity for frequent replacements.
Benefits of Using Flap Discs
One of the primary advantages of flap discs, especially the 4.1-inch variety, is their versatility. They are capable of performing multiple tasks, including stock removal, blending, and finishing. This makes them a cost-effective solution for operations that require different levels of abrasive action.
Flap discs also offer a more refined finishing compared to conventional grinding wheels. The flap design allows for greater control and maneuverability, making it easier to achieve an even surface finish. This is particularly beneficial in applications where aesthetics matter, such as in automotive or decorative metalwork.
flap disc 4.1 2
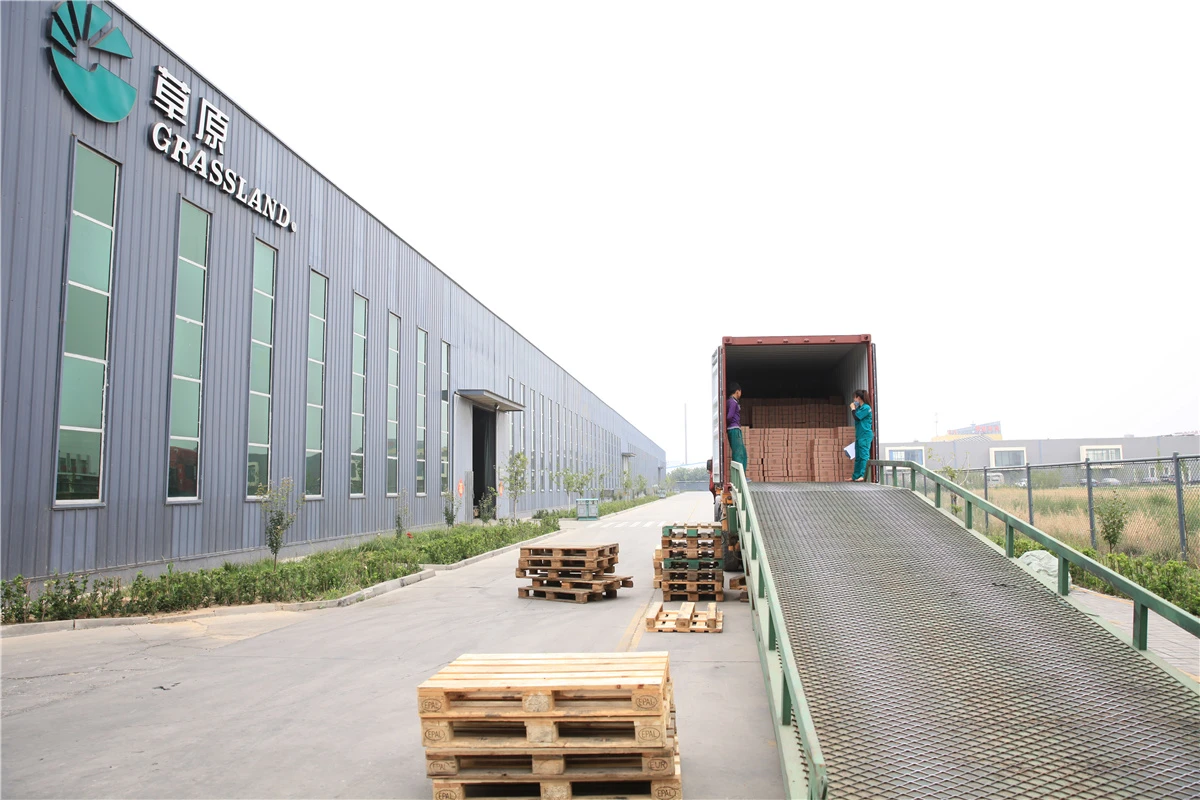
Furthermore, the user-friendly nature of flap discs is another reason for their popularity. They can be easily mounted on standard angle grinders or other power tools, facilitating a quick changeover between different grinding requirements. This ease of use reduces downtime in production environments, allowing for more efficient workflows.
Choosing the Right Flap Disc
When selecting a flap disc, several factors need to be considered. The material to be worked on is crucial, as this will dictate both the type of abrasive and the grit size needed. For example, zirconia flap discs are ideal for high-pressure applications and tend to perform well on stainless steel, while aluminum oxide is better suited for softer metals or wood.
Grit size is another important consideration. Coarse grits (like 40 or 60) are suitable for aggressive stock removal, while finer grits (like 120 or 180) are better for finishing work. Understanding the specific requirements of your project will help in choosing the most appropriate flap disc.
Safety Considerations
While flap discs are relatively safe to use, adhering to safety guidelines is essential. Always wear appropriate personal protective equipment, such as goggles and face shields, to protect against flying debris. Ensuring that the flap disc is rated for the speed of your grinder is also vital to prevent accidents. Regular inspection for wear and tear can further enhance safety during operation.
Conclusion
Flap discs, particularly the 4.1-inch variety, are indispensable tools in various industries, offering a unique combination of versatility, efficiency, and ease of use. As technology advances, the quality and functionality of these discs continue to improve, catering to the evolving needs of professionals across many fields. Whether for heavy-duty grinding or delicate finishing tasks, flap discs remain a go-to solution, proving their worth in any toolkit. By understanding their features, benefits, and proper usage, users can maximize their effectiveness and ensure high-quality results in their projects.
Post time:Nov - 28 - 2024