Understanding Flap Discs for Grinders
Flap discs are essential tools in the metalworking and fabrication industries, renowned for their versatility and efficiency in grinding, blending, and finishing surfaces. These discs, which are composed of multiple overlapping layers or flaps of abrasive material, offer unique advantages that make them a preferred choice over traditional grinding wheels and sandpaper.
Construction and Design
The typical flap disc consists of an abrasive material attached to a backing plate. The flaps are arranged radially around the disc, creating a conical shape that allows for aggressive material removal while also providing a smooth finish. The flaps are usually made from various abrasive materials, including aluminum oxide, zirconia, and ceramic, catering to different applications and materials.
The backing plate can be either fiberglass or rubber, adding to the durability and stability of the disc during use. The design of flap discs allows them to work effectively on various materials, including metals, wood, and composites, making them versatile tools in any workshop.
Applications
Flap discs are commonly used in a wide range of applications, including metal fabrication, automotive repair, and woodworking. Their ability to grind and finish a surface simultaneously makes them ideal for tasks such as weld removal, paint stripping, and surface preparation before painting or coating.
When used on metal surfaces, flap discs can efficiently remove rust, scale, and old paint without damaging the underlying material. This is particularly beneficial in industries where maintaining the integrity of the base material is crucial. Moreover, the various grit sizes available provide options for both aggressive material removal and finer finishing work.
Advantages of Flap Discs
flap disc for grinder
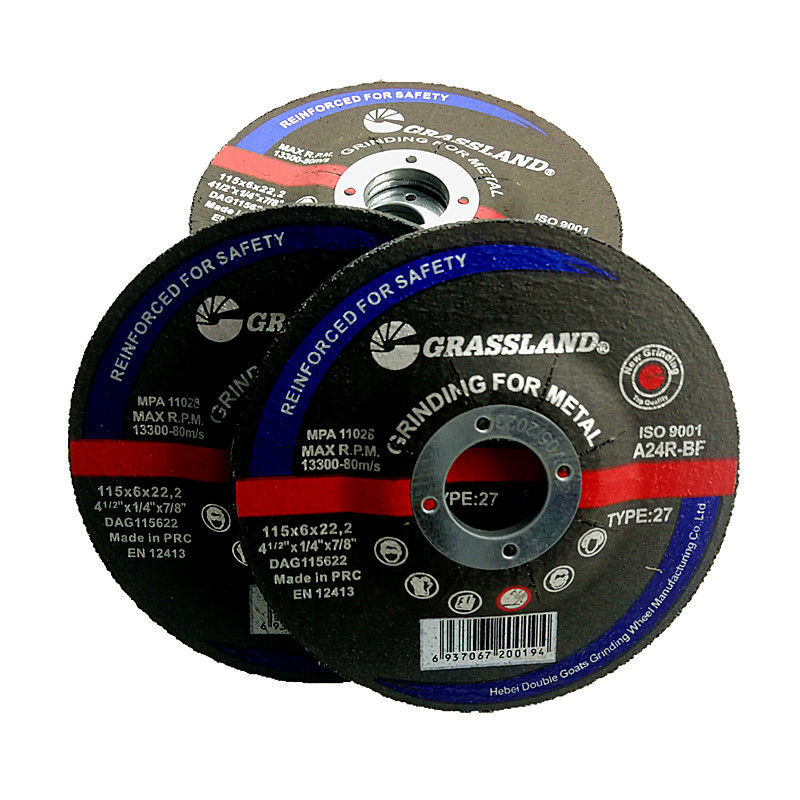
One of the primary advantages of flap discs is their ability to maintain a consistent cutting action throughout their lifespan. Unlike traditional grinding wheels that tend to wear down unevenly, flap discs provide a more uniform finish, leading to reduced operator fatigue and improved efficiency.
Additionally, flap discs generate less heat compared to traditional grinding methods, minimizing the risk of overheating the workpiece. This is especially important when working with heat-sensitive materials, as excessive heat can lead to structural changes and weaken the material.
Another noteworthy advantage is their ease of use. Flap discs are compatible with most angle grinders, making them accessible for both professionals and DIY enthusiasts. They are simple to replace and come in various sizes to fit different grinders, making them adaptable to various tasks.
Choosing the Right Flap Disc
When selecting a flap disc, it's essential to consider several factors, including the material being worked on, the desired finish, and the specific application. Grit size plays a crucial role; lower grit numbers (e.g., 40-60) are ideal for aggressive grinding and material removal, while higher grit numbers (e.g., 80-120) are suited for finishing and smoother surface preparations.
The type of abrasive material also influences the performance of the flap disc. For example, zirconia discs are effective for grinding harder metals, whereas ceramic discs are better suited for high-performance applications. It’s also important to select the correct disc shape for the job—flat discs are typically used for flat surfaces, while conical discs better suit edge grinding and intricate shapes.
Conclusion
Flap discs represent a significant advancement in abrasive technology, providing metalworkers and fabricators with an effective and efficient tool for a variety of applications. Their unique design, coupled with their versatility and ease of use, makes them an indispensable part of any tool collection. Whether you are a professional tradesperson or a weekend hobbyist, understanding and utilizing flap discs can elevate the quality of your work while enhancing productivity.
Post time:Nov - 15 - 2024