Understanding Flap Discs for Grinders A Comprehensive Guide
Flap discs are essential tools widely used in metalworking, woodworking, and various industrial applications for grinding, blending, and finishing surfaces. They have gained popularity due to their versatility and efficiency compared to traditional grinding wheels. In this article, we will explore what flap discs are, their construction, various types, applications, and advantages.
What is a Flap Disc?
A flap disc is a particular type of abrasive tool that features overlapping, flexible flaps of abrasive material attached to a backing plate. These flaps are arranged radially and are designed to provide a grinding surface while maintaining a degree of flexibility. This design allows for both grinding and finishing in one step, making flap discs a favorite among professionals and DIY enthusiasts.
Construction of Flap Discs
Flap discs consist of three primary components
1. Abrasive Flaps These flaps are typically made from materials like aluminum oxide, zirconia alumina, or ceramic. The choice of material depends on the application and the type of metal being worked on. Zirconia, for instance, is excellent for stainless steel and high-alloy materials, while aluminum oxide is suitable for softer metals.
2. Backing Plate The flaps are affixed to a backing plate made of fiberglass, plastic, or metal. The backing plate provides structure and stability to the disc, ensuring that it performs well under pressure.
3. Attachment Mechanism Flap discs can come with different mounting options, such as a 7/8 hole for easy attachment to angle grinders, or a threaded hole for direct mounting on specific machines.
Types of Flap Discs
Flap discs come in several types, each designed for specific applications
1. Type 27 These are flat flap discs best used for grinding and blending applications on flat surfaces. They have a wider flanged edge that helps with material removal.
2. Type 29 These flap discs have a more conical shape, which allows for better grinding on contoured or irregular surfaces. They are ideal for edge work and can reach into crevices.
flap disc for grinder
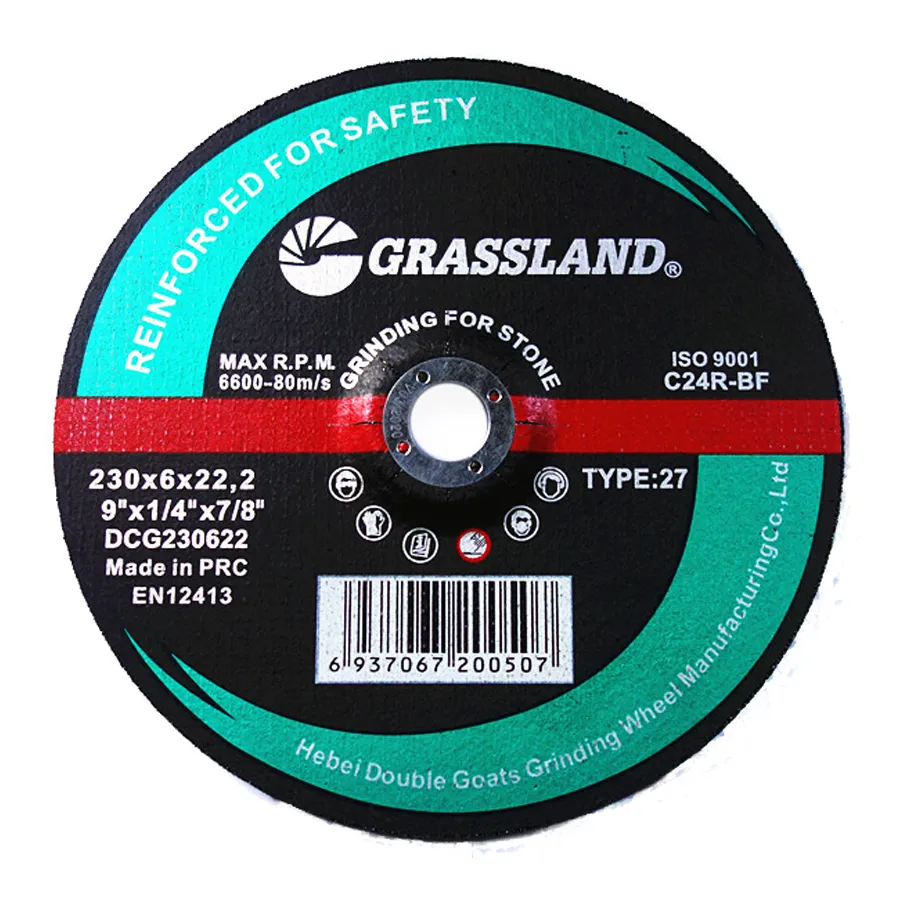
3. Specialty Discs There are also flap discs designed for specific materials or finishes, such as those designed for use on wood or for creating a satin finish on aluminum.
Applications of Flap Discs
Flap discs are incredibly versatile and find application in various fields, including
- Metal Fabrication Used for grinding, deburring, and finishing metal surfaces. - Woodworking Ideal for smoothing wood joints and finishing surfaces without damaging the material. - Automotive Repair Often used for removing paint, rust, and other surface contaminants from vehicles. - Construction Employed for grinding concrete and masonry, as well as metalworks.
Advantages of Using Flap Discs
1. Efficiency Flap discs remove material quickly while producing less heat compared to traditional grinding wheels, reducing the risk of workpiece damage.
2. Durability The layered structure of flap discs enables them to last longer, providing excellent longevity and reducing the frequency of replacements.
3. Versatility With different grit options available, flap discs can be used for a range of applications, from heavy grinding to fine finishing.
4. User-Friendly Flap discs are easy to change and use, making them accessible for both professionals and hobbyists.
5. Reduced Dust Compared to other grinding tools, flap discs produce less dust, contributing to a cleaner working environment.
Conclusion
Flap discs have revolutionized the way grinding and finishing are performed across various industries. Their unique construction, combined with a wide range of applications and significant advantages, makes them a go-to choice for many metalworkers and craftsmen. By understanding the different types of flap discs and their specific uses, users can enhance their efficiency and achieve superior results in their projects. Whether you are a seasoned professional or a novice tinkering in your garage, incorporating flap discs into your toolkit can greatly improve your workflow and the quality of your work.
Post time:Dec - 25 - 2024