Understanding Flap Discs for Grinding Aluminum
When it comes to metalworking, specifically grinding aluminum, choosing the right tools is crucial for achieving optimal results. One essential tool in this process is the flap disc. Traditionally utilized in various industries for surface preparation and finishing tasks, flap discs have garnered attention for their efficiency and versatility, particularly when working with aluminum.
What is a Flap Disc?
A flap disc is an abrasive tool composed of overlapping flaps of abrasive material, typically arranged in a radial pattern around a central hub. The flaps are usually made from materials suited for metal surfaces, such as aluminum oxide or zirconia alumina. The design of a flap disc allows for consistent wear over time, ensuring a stable and long-lasting performance during grinding operations.
Why Use Flap Discs for Aluminum?
Grinding aluminum presents unique challenges due to its soft and ductile nature. When improperly ground, aluminum can clog abrasive materials, leading to inefficient grinding and increased work time. Flap discs are particularly advantageous for aluminum because they provide a controlled exposure of the abrasive material, reducing the risk of clogging and ensuring effective material removal.
1. Versatility Flap discs come in various grits, making them suitable for several tasks, from rough grinding to fine finishing. This adaptability allows operators to use a single tool for multiple applications, streamlining the workflow and minimizing the need for different abrasives.
2. Efficient Cooling One challenge when grinding aluminum is the heat generated during the process. Flap discs are designed to manage heat build-up effectively. Their construction allows for better airflow compared to traditional grinding wheels, which helps keep the workpiece cooler and prevents warping or damage to the aluminum.
flap disc for grinding aluminum
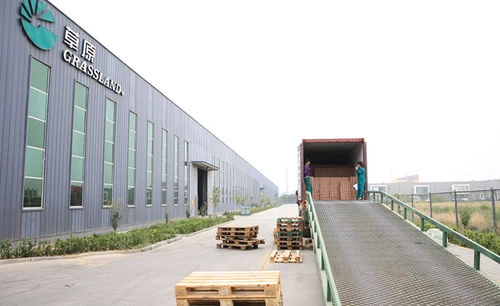
3. Reduced Loading The overlapping flaps of a flap disc create a larger surface area, which helps distribute pressure more evenly. This reduces the likelihood of the abrasive material loading up with metal shavings, a common issue when grinding softer materials like aluminum. As a result, users can achieve a cleaner finish and longer disc life.
4. Excellent Finish Quality Flap discs can produce a superior surface finish compared to conventional grinding wheels. The design allows for smoother operation, resulting in a finer, more uniform finish that is particularly valued in industries where aesthetics are crucial.
5. Ease of Use Flap discs are user-friendly and can be easily mounted on various power tools, such as angle grinders. Their straightforward application makes them accessible for both professionals and hobbyists.
How to Choose the Right Flap Disc for Aluminum
When selecting a flap disc for grinding aluminum, consider the following factors
- Grit Size For initial material removal, opt for a coarser grit (40-60). For finishing touches and smoothing surfaces, finer grits (80-120) work best. - Material Composition Aluminum oxide discs are the most suitable for aluminum, but consider zirconia for added durability in heavier applications. - Disc Type The angle of the flap and the type of backing plate can influence performance. Flat flap discs are ideal for flat surfaces, while conical discs can reach into corners and contours.
Conclusion
Flap discs offer a myriad of advantages for grinding aluminum, making them a preferred choice among metalworkers seeking efficiency and quality. By understanding their benefits and selecting the right type, you can enhance your grinding processes, ensuring exceptional results on every project. Whether you're in automotive repair, aerospace manufacturing, or metal fabricating, incorporating flap discs into your arsenal will undoubtedly elevate your craftsmanship.
Post time:Sep - 28 - 2024