Understanding Flap Discs for Stone A Comprehensive Guide
When it comes to the realm of stone processing, the right tools can significantly enhance productivity and quality. Among these tools, flap discs have emerged as invaluable assets. Specifically designed for the grinding and finishing of stone surfaces, flap discs offer a unique combination of efficiency and precision. In this article, we will explore the fundamentals of flap discs for stone, their benefits, and considerations for selecting the right product for your needs.
What Are Flap Discs?
Flap discs consist of multiple layers or flaps of abrasive material attached to a central disc. This design allows for both grinding and finishing in a single tool, making it a versatile choice for professionals working with stone. The flaps are typically made from various materials, such as zirconia, aluminum oxide, or ceramic, each offering distinct advantages depending on the application and the type of stone being worked on.
Benefits of Using Flap Discs for Stone
1. Versatility Flap discs are suitable for a wide range of applications, including grinding, stock removal, and surface finishing. They can be used on various types of stone, such as granite, marble, and limestone, making them an essential tool for stonemasons, sculptors, and construction workers.
2. Enhanced Performance One of the standout features of flap discs is their ability to provide a smoother finish compared to traditional grinding wheels. The layered flaps help distribute pressure evenly across the stone surface, reducing the risk of gouging or uneven wear.
3. Longer Lifespan Flap discs tend to have a longer operational lifespan than conventional grinding wheels. As the outer layers wear down, new abrasive material is exposed, allowing for continuous cutting and reducing the need for frequent replacements.
4. Reduced Heat Generation The design of flap discs promotes better airflow during operation, which helps dissipate heat. This is particularly important when working with certain types of stone that can be sensitive to heat, as excessive heat can lead to cracking or discoloration.
flap disc for stone
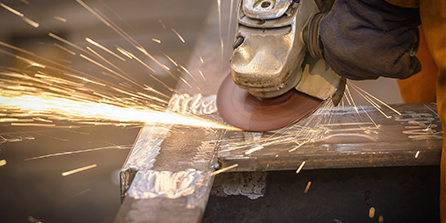
5. Ease of Use Flap discs are generally easy to operate, making them accessible for both seasoned professionals and beginners. They can be mounted on various power tools, including angle grinders, which are commonly used in stone finishing tasks.
Selecting the Right Flap Disc for Stone
Choosing the right flap disc for specific stone applications involves several considerations
- Abrasive Material The type of abrasive material significantly impacts the performance and durability of the flap disc. Zirconia discs are ideal for aggressive stock removal on hard stones, while ceramic flap discs perform well on softer materials and provide a cooler cut.
- Grit Size Grit size determines the coarseness of the abrasive material. Lower grit numbers (e.g., 40-60) are suitable for heavy grinding and material removal, while higher grit numbers (e.g., 80-120) are used for finishing and polishing.
- Disc Diameter The size of the flap disc must match the tool being used. Common sizes range from 4 to 7 inches in diameter. Larger discs provide a broader surface area for faster material removal, while smaller discs offer more control for precise tasks.
- Attachment Type Flap discs come with different attachment systems, including threaded and quick-change designs. Ensure that the type you choose is compatible with your power tool.
Conclusion
In summary, flap discs are a remarkable solution for stone processing, combining grinding and finishing capabilities in a single tool. Their versatility, long lifespan, and reduced heat generation make them an excellent investment for anyone working with stone. By understanding the benefits and considering the right factors for selection, users can enhance their effectiveness and achieve superior results in their stonework. Whether you are a professional artisan or a DIY enthusiast, incorporating flap discs into your toolkit will undoubtedly elevate your stone processing efforts.
Post time:Dec - 05 - 2024