The Essential Guide to Using a Flap Disc Grinder
Flap disc grinders have become an indispensable tool for metalworking and surface finishing tasks. Combining the functions of grinding, blending, and polishing into one versatile tool, flap discs are characterized by their layered design, which allows for both aggressive material removal and smooth finishing. This article will guide you through the proper use of flap disc grinders, emphasizing safety, techniques, and maintenance.
Understanding Flap Discs
Flap discs are composed of numerous overlapping abrasive flaps attached to a backing plate. They come in various grits, allowing users to select the appropriate disc for their project, whether it demands heavy stock removal or a more refined finish. The common abrasives used include alumina, zirconia, and ceramic, each offering different benefits depending on the material being worked on.
Equipment Safety
Before diving into usage, it's crucial to prioritize safety. Always wear protective gear, including safety goggles, gloves, and a dust mask, to shield yourself from harmful dust and flying debris. Ensure that the flap disc grinder is equipped with the appropriate safety features, such as a guard to prevent injuries from accidental contact with the disc.
1. Inspect Your Tools Before operating your flap disc grinder, inspect it for any damage. Check the cord, plug, and on/off switch for any signs of wear. Ensure the flap disc is properly mounted and free from cracks or defects. 2. Work Environment Make sure that your workspace is clean and free of any flammable materials. Adequate lighting will also enhance visibility, reducing the risk of accidents.
Techniques for Effective Use
Using a flap disc grinder involves specific techniques to maximize efficiency and ensure a high-quality finish
1. Choosing the Right Disc Select a flap disc grit suitable for your application. A coarse grit (24-60) is excellent for heavy stock removal, while a medium grit (60-120) can be used for blending, and fine grit (120-400) is ideal for polishing.
flap disc grinder use
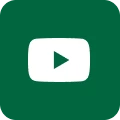
2. Proper Angle and Pressure When grinding, hold the grinder at an angle of approximately 15 to 30 degrees to the workpiece. This positioning ensures effective material removal without risking gouging the surface. Apply moderate pressure; excessive force can lead to premature wear of the disc and can damage the material being worked on.
3. Moving Techniques Use a sweeping motion to distribute the grinding evenly across the surface. Avoid staying in one spot for too long, as this can overheat the workpiece or lead to uneven surfaces. For finishing, lighter pressure and a consistent motion will yield the best results.
4. Cooling Breaks If working on a project that generates significant heat, take regular breaks to prevent overheating. This practice not only protects the material but also extends the life of the flap disc.
Maintenance and Care
Proper maintenance of your flap disc grinder extends its lifespan and maintains optimal performance
1. Clean Regularly After use, clean the grinder and flap discs from dust and debris. This care prevents the buildup of materials that could affect performance.
2. Store Safely Store the grinder in a dry, cool place when not in use. Keep flap discs in protective packaging to prevent damage.
3. Check for Wear Regularly inspect flap discs for signs of wear or damage. Replace discs when they become too worn or lose their effectiveness.
Conclusion
Using a flap disc grinder effectively requires knowledge of proper techniques, safety protocols, and maintenance routines. By following the guidelines outlined in this article, metalworkers and DIY enthusiasts alike can maximize the performance and longevity of their tools while achieving outstanding results in their projects. Embracing the versatility of flap disc grinders will enhance your craftsmanship, making your tasks easier and more efficient.
Post time:Dec - 18 - 2024