Understanding Flap Disc Grinding Wheels A Comprehensive Overview
Flap disc grinding wheels have become an essential tool in the metalworking and fabrication industries, renowned for their efficiency, versatility, and adaptability in various applications. As professional and hobbyist metalworkers seek effective solutions for surface preparation, grinding, and finishing, flap discs have emerged as a favored choice, surpassing traditional grinding wheels in several key aspects.
What Are Flap Discs?
Flap discs are made up of numerous overlapping layers, or flaps, of abrasive material, typically sandpaper or similar abrasive cloth. These flaps are adhered to a rigid backing plate, usually comprised of fiberglass or metal. The design allows for both grinding and finishing in one tool, making flap discs particularly useful for achieving smooth and polished surfaces on a variety of materials, including metal, wood, and plastics.
Advantages of Flap Discs
1. Versatility Flap discs can be utilized for a wide range of applications, including grinding, blending, finishing, and deburring. This versatility makes them suitable for various materials, from tough metals to soft plastics, allowing fabricators to streamline their processes by using a single tool for multiple tasks.
2. Efficiency Thanks to their design, flap discs can remove material quickly while producing less heat than traditional grinding wheels. This reduction in heat generation minimizes the risk of warping or damaging the substrate, which is particularly important in precision metalworking. The efficient material removal also enhances productivity, allowing users to complete tasks faster.
3. Finishing Quality The layered design of flap discs provides a consistent finish, which is crucial in applications where surface quality matters. They can transition smoothly from heavy material removal to finer finishing, making it easier to achieve the desired finish without the need for multiple tools.
4. Safety Flap discs are generally regarded as safer to use compared to traditional grinding wheels. The flexible flaps conform better to the surface being worked on, reducing the chances of snagging or binding. Additionally, since they are less prone to breakage, users face a lower risk of injury during operation.
flap disc grinding wheel
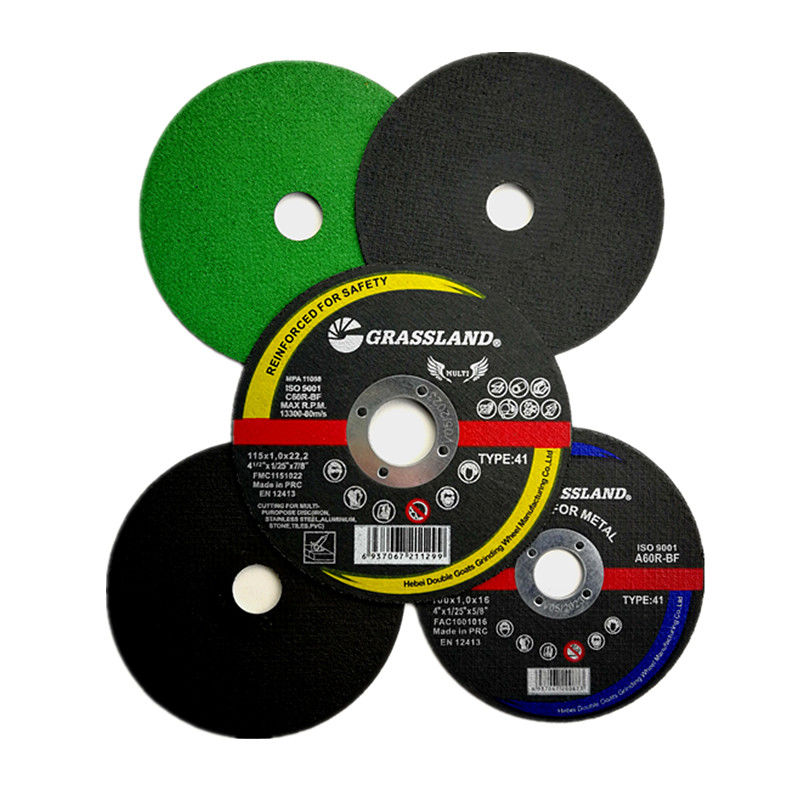
5. Cost-Effective While the initial investment in flap discs may be higher than traditional grinding wheels, their durability and the decreased need for tool changes can result in significant cost savings over time. Fewer tool changes mean less downtime, which translates into increased productivity and profitability.
Choosing the Right Flap Disc
Selecting the appropriate flap disc is crucial to achieving the desired results, and it comes down to a few essential factors
- Material Flap discs are available in various abrasive materials, including aluminum oxide, zirconia alumina, and ceramic. Each material has unique properties tailored for different applications. Zirconia alumina, for example, is ideal for aggressive grinding on metals, while aluminum oxide is suitable for wood and softer materials.
- Grit Size The grit size of the flap disc determines the coarseness or fineness of the abrasive. Lower grit numbers correspond to coarser abrasives for heavy material removal, while higher grit numbers are ideal for finer finishes. Choosing the right grit size is essential based on the specific task at hand.
- Backing Plate Flap discs come in various backing plate configurations, including flat and conical shapes. Flat discs are commonly used for flat surfaces, whereas conical (or tapered) discs are better suited for surface grinding in hard-to-reach areas or for edge blending.
- Size Flap discs are available in multiple diameters, typically ranging from 4 inches to 7 inches. The size you choose should align with the equipment you’re using and the scale of your project.
Conclusion
Flap disc grinding wheels represent a significant advancement in abrasive technology, providing unparalleled versatility, efficiency, and safety for metalworking and fabrication tasks. By understanding the properties and applications of flap discs, metalworkers can select the right tools for their projects, enhancing their work quality and productivity. As industries continue to evolve, flap discs will undoubtedly remain a preferred choice for those seeking reliable and effective grinding solutions.
Post time:Oct - 07 - 2024