Understanding Flap Disc Grinding Wheels A Comprehensive Guide
Flap disc grinding wheels are essential tools in metalworking and surface finishing processes, lauded for their versatility and efficiency. These wheels consist of multiple overlapping abrasive flaps, allowing for both grinding and polishing in a single application. This article provides a comprehensive overview of flap disc grinding wheels, their construction, benefits, and ideal applications.
Construction of Flap Discs
Flap discs are commonly made from various abrasive materials, including aluminum oxide, zirconia, and ceramic. The choice of material is crucial as it determines the wheel's effectiveness on different substrates. For instance, aluminum oxide is suitable for general-purpose grinding, while zirconia and ceramic flaps provide superior performance on hard metals due to their durability and longevity.
The flaps are typically arranged around a central hub, which allows for greater flexibility and easier blending of surfaces. This design not only reduces the risk of gouging the material being worked on but also improves the overall finish. The angle of the flaps can vary, with common configurations including a flat or conical shape, allowing users to choose based on their specific grinding needs.
Benefits of Flap Disc Grinding Wheels
1. Versatility Flap discs can be used for a multitude of applications, from grinding and deburring to surface blending and finishing. This versatility makes them an excellent choice for metal fabrication, automotive repair, and woodworking industries.
2. Efficiency The design of flap discs facilitates quicker material removal compared to traditional grinding wheels. Their multi-layered structure allows for less heat generation during operation, leading to extended tool life and reduced workpiece distortion.
3. Reduced Vibration Unlike rigid grinding wheels, flap discs provide flexibility, which minimizes vibration and improves the user's control. This feature enhances precision in grinding and finishing operations, making them suitable for both professional and DIY users.
4. User-Friendly Flap discs come in various sizes and grits, catering to a wide range of applications. The simple attachment process to angle grinders or other power tools further contributes to their popularity among users of varying skill levels.
5. Cost-Effectiveness Although flap discs may have a higher upfront cost than conventional grinding wheels, their longevity and efficiency yield a lower cost per use. This durability translates into fewer replacements and less downtime, greatly benefiting operational productivity.
flap disc grinding wheels
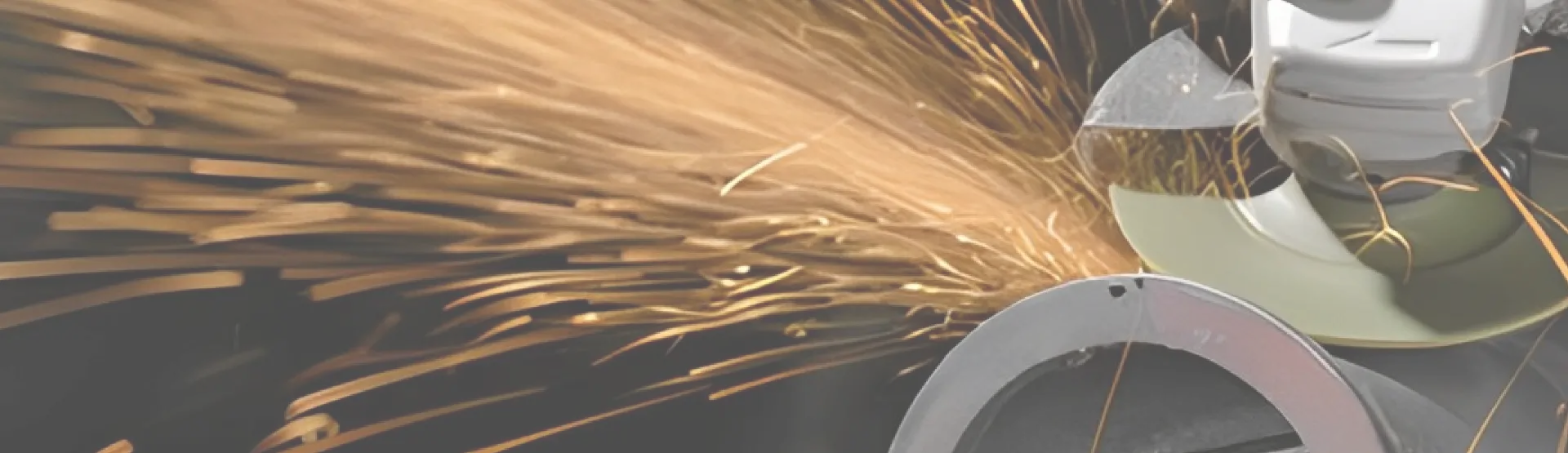
Ideal Applications
Flap disc grinding wheels excel in both heavy stock removal and finer finishing tasks. Here are some common applications
- Metal Fabrication They are extensively used for grinding welds and removing surface imperfections from ferrous and non-ferrous metals. - Automotive Industry Flap discs are perfect for bodywork preparation and finishing, as they efficiently contour surfaces and achieve a smooth finish. - Woodworking Woodworkers utilize flap discs to shape and finish wood surfaces. They are particularly effective for sanding contours and edges. - Masonry and Concrete Certain flap discs designed for tougher materials are ideal for grinding concrete and masonry surfaces.
Choosing the Right Flap Disc
When selecting a flap disc, several factors must be considered
1. Material Type Choose a suitable abrasive material based on the workpiece's hardness. Zirconia discs work well for metals, while aluminum oxide is better for softer materials. 2. Grit Size Flap discs are available in various grit sizes ranging from coarse to fine. Coarser grits (like 40 or 60) are suitable for aggressive material removal, while finer grits (like 120 or 240) are used for polishing and finishing.
3. Disc Diameter Standard flap discs range from 4 to 9 inches in diameter. The size should be chosen based on the area to be worked on and the type of tool being used.
4. Disc Shape Flat and conical shapes serve different purposes. Flat discs are preferred for flat surfaces, while conical discs are better for contouring.
Conclusion
Flap disc grinding wheels represent a crucial advancement in the field of abrasives, providing significant advantages in terms of versatility, efficiency, and ease of use. By understanding their construction, benefits, and applications, users can make informed decisions that enhance their productivity and achieve superior results in metalworking and finishing tasks.
Post time:Dec - 15 - 2024