The Advantages of Flap Disc Polishing A Comprehensive Guide
In the realm of metalworking and fabrication, achieving a smooth, polished finish is often critical for both aesthetic and functional purposes. Flap discs have emerged as a valuable tool in this context, providing efficient polishing solutions that cater to a variety of materials and applications. This article explores the features, benefits, and best practices associated with flap disc polishing.
Understanding Flap Discs
Flap discs are abrasive tools made of multiple overlapping layers or flaps of abrasive material, typically adhered to a backing plate. These flaps are arranged radially and are designed to conform to the surface being polished. The unique structure of flap discs allows for a combination of grinding and polishing in a single tool, making them versatile for various tasks.
The Benefits of Flap Disc Polishing
1. Versatility Flap discs can be used on a wide range of materials, including metals, wood, plastics, and composites. This versatility makes them an ideal choice for weld blending, deburring, and final polishing, enabling users to achieve desired results on different surfaces without needing to switch tools.
2. Efficiency Compared to traditional sanding methods or grinding wheels, flap discs provide faster material removal rates while maintaining a finer finish. This efficiency is particularly advantageous in industrial settings where productivity is paramount.
3. Consistent Finishing The overlapping flaps of a flap disc help to distribute pressure evenly across the surface. This feature ensures a more uniform finish, reducing the risk of gouging or uneven spots that can occur with other abrasive tools.
4. Reduced Heat Buildup Flap discs tend to generate less heat during operation than other grinding tools. This characteristic is crucial for preventing damage to heat-sensitive materials and ensuring a longer lifespan for both the tools and the workpiece.
flap disc polishing
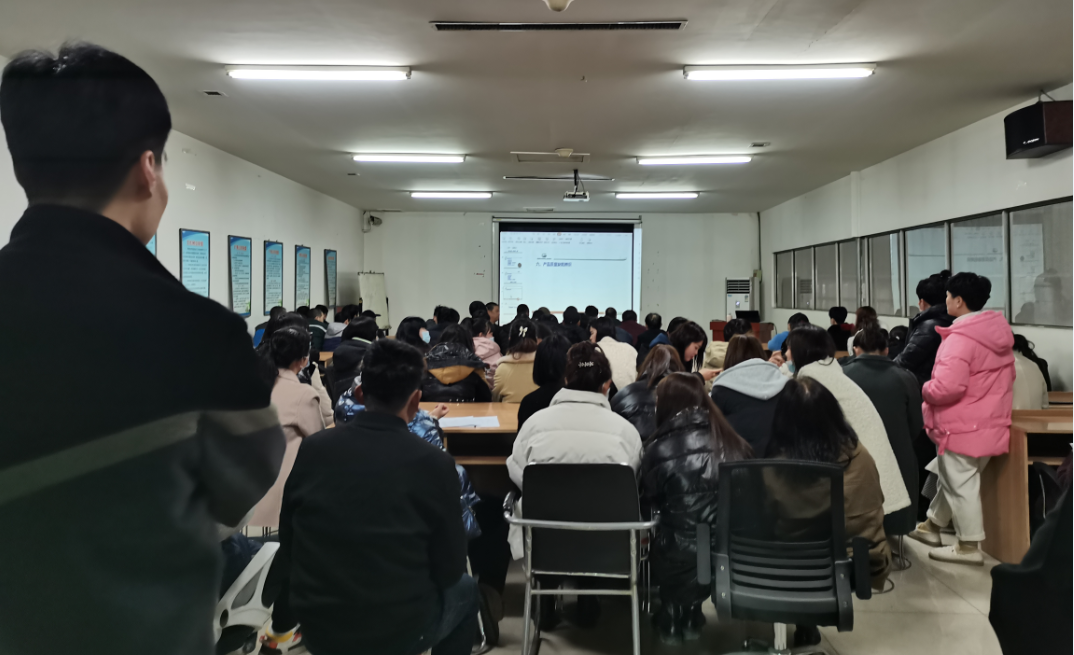
5. Ease of Use Flap discs are typically compatible with various angle grinders and can be easily mounted and replaced. This user-friendly aspect contributes to their popularity among both professionals and DIY enthusiasts.
Best Practices for Flap Disc Polishing
To maximize the effectiveness of flap discs in polishing applications, consider the following best practices
- Choose the Right Grit Flap discs come in various grits ranging from coarse to fine. Selecting the appropriate grit for your specific task is vital; coarser grits are suitable for heavy material removal, while finer grits are ideal for polishing and achieving a smooth surface finish.
- Maintain Proper Angle and Pressure When using a flap disc, maintaining the correct angle and applying consistent pressure can dramatically affect the quality of the finish. A typical angle of 15 to 30 degrees from the work surface can yield optimal results.
- Move in a Controlled Manner Avoid applying excessive force or staying in one spot for too long, as this can cause uneven wear on the flap disc and lead to undesirable surface imperfections. Instead, use smooth, controlled movements to ensure uniformity.
- Regularly Inspect and Replace Discs Like any abrasive tool, flap discs have a limited lifespan. Regularly checking for wear and replacing them when necessary ensures consistent performance and quality in your polishing tasks.
Conclusion
Flap disc polishing presents an efficient, versatile, and user-friendly option for achieving superior finishes on various materials. With their ability to grind and polish in a single step, these tools are indispensable for professionals and hobbyists alike. By following best practices and choosing the right materials, users can unlock the full potential of flap discs, enhancing their metalworking and fabrication pursuits. Whether you're in a factory, workshop, or home garage, flap discs are a valuable addition that can streamline your polishing process and produce high-quality results.
Post time:Dec - 15 - 2024