The Advantages of Flap Disc Polishing in Metal Fabrication
In the realm of metal fabrication and finishing, achieving a smooth, aesthetically pleasing surface is crucial. One of the most effective tools for this purpose is the flap disc. These versatile abrasives have seen widespread use in various industries due to their unique construction and superior performance. This article delves into the advantages of flap disc polishing and how it enhances the metal finishing process.
Understanding Flap Discs
Flap discs consist of a circular backing plate to which multiple overlapping flaps of abrasive material are attached. These flaps are usually made of materials like aluminum oxide, zirconia, or ceramic, which offer different levels of aggression and longevity based on the polishing requirements. Unlike traditional grinding wheels, flap discs are designed to provide a blend of grinding and finishing in a single step, making them an invaluable tool for fabricators and welders alike.
Efficient Metal Removal
One of the standout features of flap disc polishing is its ability to remove material efficiently
. The overlapping design of the flaps allows for a larger surface area to come into contact with the workpiece, leading to faster removal rates. This efficiency is particularly beneficial in applications where operators need to smooth out welds or remove significant material from metal surfaces. It drastically reduces the time spent on finishing tasks, increasing overall productivity.Versatility in Applications
Flap discs are incredibly versatile and can be used on a variety of materials, including steel, stainless steel, aluminum, and even wood and plastic. Whether it’s for grinding, blending, or polishing, these discs can adapt to different processes, making them an essential tool for workshops dealing with diverse projects. Additionally, the grit sizes available range from coarse to fine, allowing operators to choose the appropriate disc for their specific finishing needs.
flap disc polishing
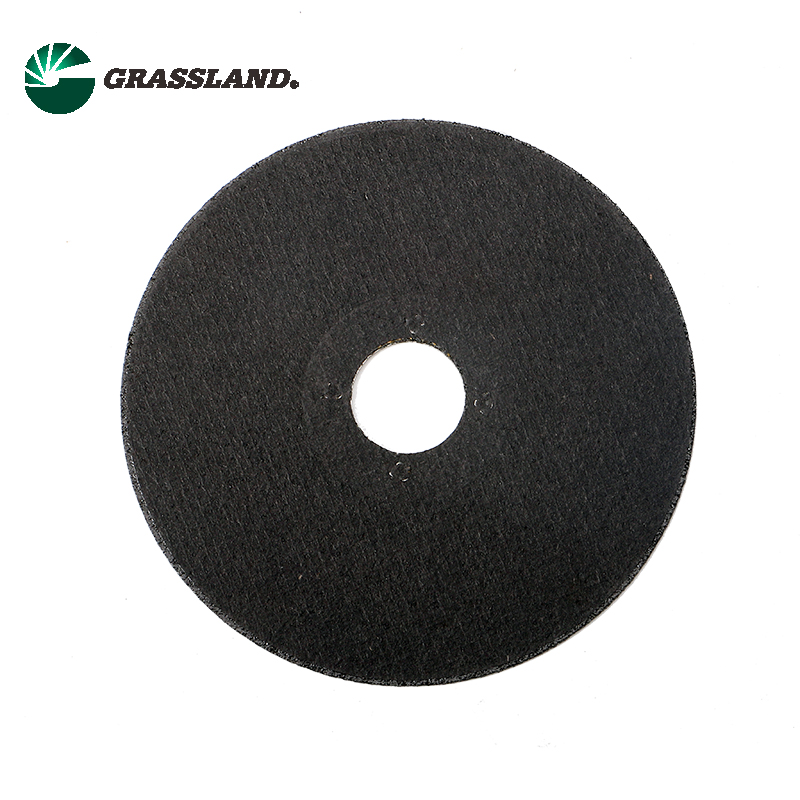
Reduced Heat Generation
One common challenge in metal polishing is the generation of heat, which can lead to warping or altering the material’s properties. Flap discs excel in this area due to their design. The flaps' flexibility allows them to conform to the contours of the workpiece, reducing pressure points that often lead to excess heat build-up. This results in a cooler grinding process, preserving the integrity of the material, which is particularly important in high-precision applications.
Enhanced Surface Finish
Another significant advantage of flap disc polishing is the superior surface finish it can achieve. With the option to use finer grits, operators can create a smooth, polished surface without the need for additional finishing processes. This quality is particularly critical in industries where aesthetics matter, such as automotive and decorative metalwork. The polish achieved with flap discs often requires less post-finishing, saving both time and resources.
Cost-Effectiveness
While providing high efficiency and great results, flap discs are also cost-effective. They typically have a longer lifespan than traditional abrasives, as their design allows for even wear. This means fewer disc changes during a job and lower overall supplies costs. Moreover, the time saved through faster polishing processes translates into significant labor cost reductions, making flap discs a smart investment for any metalworking operation.
Conclusion
Flap disc polishing is a game-changer in metal fabrication and finishing. With their ability to efficiently remove material, versatility across different applications, reduced heat generation, and enhanced surface finish, flap discs stand out as an essential tool for welders and fabricators. Moreover, their cost-effectiveness makes them a go-to choice for businesses looking to improve their productivity and maintain high-quality standards. In today’s fast-paced manufacturing world, utilizing flap disc polishing can give companies a competitive edge while achieving excellent results in metal finishing.
Post time:Nov - 21 - 2024