The Advantages of Using Flap Discs for Aluminum Fabrication
Aluminum is widely used in various industries due to its lightweight, corrosion-resistant, and malleable properties. However, when it comes to fabricating or finishing aluminum surfaces, choosing the right tool is crucial to achieving the desired results. One of the most effective tools for this purpose is the flap disc. In this article, we explore the advantages of using flap discs specifically for aluminum and why they have become the go-to choice for many metalworkers and fabricators.
What are Flap Discs?
Flap discs are abrasive tools designed for metalworking. They consist of multiple overlapping layers or “flaps” of abrasive material, usually made from aluminum oxide or zirconia, attached to a central hub. This design allows for both grinding and sanding in a single disc, making them versatile tools for smoothing, blending, and finishing surfaces.
Benefits of Flap Discs for Aluminum
1. Superior Surface Finish When working with aluminum, achieving a smooth, polished surface is often a priority. Flap discs provide an excellent surface finish without gouging the material, as they conform to the contours of the workpiece. The layered design gently wears down the surface, resulting in a clean and professional look.
2. Reduced Heat Generation One of the challenges when working with aluminum is the risk of heat buildup, which can lead to warping or damage to the material. Flap discs generate less heat compared to traditional grinding wheels. Their design allows for efficient heat dissipation, making them ideal for aluminum and reducing the risk of discoloration and structural damage.
3. Versatility Flap discs are available in different grits, ranging from coarse to fine. This allows for a seamless transition from heavy material removal to finishing touches. Whether you are removing welds, deburring edges, or polishing surfaces, flap discs can adapt to various tasks, making them a multi-functional tool in any workshop.
flap discs for aluminum
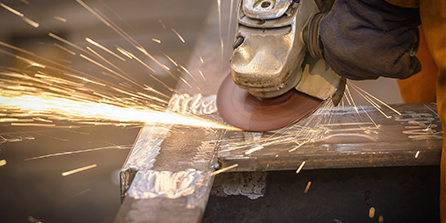
4. Enhanced Control The flexible nature of flap discs allows for greater control during operation. They can be used at various angles and orientations, making it easier to reach tight spots and intricate designs. This characteristic is especially beneficial when working on complex aluminum components where precision is key.
5. Longer Lifespan Flap discs tend to last longer than traditional grinding wheels. The staggered flaps wear down evenly, providing consistent performance throughout their lifespan. This not only reduces the frequency of replacements but also minimizes downtime during projects, making them a cost-effective option for fabricators.
6. Minimal Dust Creation When working with aluminum, excessive dust can be a significant concern. Flap discs typically produce less dust compared to other abrasives. This not only enhances visibility during the working process but also improves air quality, making the workspace safer for operators.
Choosing the Right Flap Disc for Aluminum
When selecting flap discs for aluminum, it is essential to consider the type of aluminum being worked on and the specific requirements of the task. For general grinding and removal, coarse grits (40-60) are effective, while fine grits (80-120) are better suited for finishing and polishing. It’s also important to choose discs specifically designed for aluminum to avoid loading, which can occur when materials adhere to the abrasive surface.
Conclusion
Flap discs have revolutionized the way fabricators work with aluminum, offering numerous advantages over traditional abrasives. Their ability to achieve superior surface finishes, manage heat, provide versatility, enhance control, and minimize dust make them an indispensable tool in metalworking. As industries continue to rely on aluminum for their projects, the use of flap discs will undoubtedly continue to grow, showcasing their effectiveness and efficiency in achieving high-quality results. For those in the metalworking field, incorporating flap discs into your toolkit is not just a choice; it’s a step towards excellence.
Post time:Dec - 05 - 2024