A Comparative Analysis of T27 and T29 Flap Discs
Flap discs have become an essential tool in the field of metal fabrication and finishing. They are favored for their versatility, efficiency, and ability to deliver a superior finish. Among the various types of flap discs, T27 and T29 are two of the most commonly used designs. Each of these discs has unique characteristics that make them suitable for different applications. This article provides a comparative analysis of T27 and T29 flap discs, highlighting their structure, uses, advantages, and limitations.
Structure and Design
The primary difference between T27 and T29 flap discs lies in their design. T27 discs feature a flat profile, where the flaps are arranged in a parallel manner to the backing plate. This design allows for greater contact with the workpiece surface, making them ideal for flat surfaces and finishing applications. On the other hand, T29 discs have a slightly angled configuration, meaning that the flaps are arranged at a 10 to 15-degree angle relative to the backing plate. This design allows for a more aggressive cut and is better suited for contouring and grinding applications.
Applications
The choice between T27 and T29 flap discs often depends on the specific job requirements. T27 flap discs are primarily used for finishing and blending tasks. They excel in applications where a smooth surface is critical, such as preparing metal surfaces for painting or coating. The flat design helps in achieving a uniform finish without excessive material removal.
A Comparative Analysis of T27 and T29 Flap Discs
Speed and Longevity
flap disc t27 vs t29
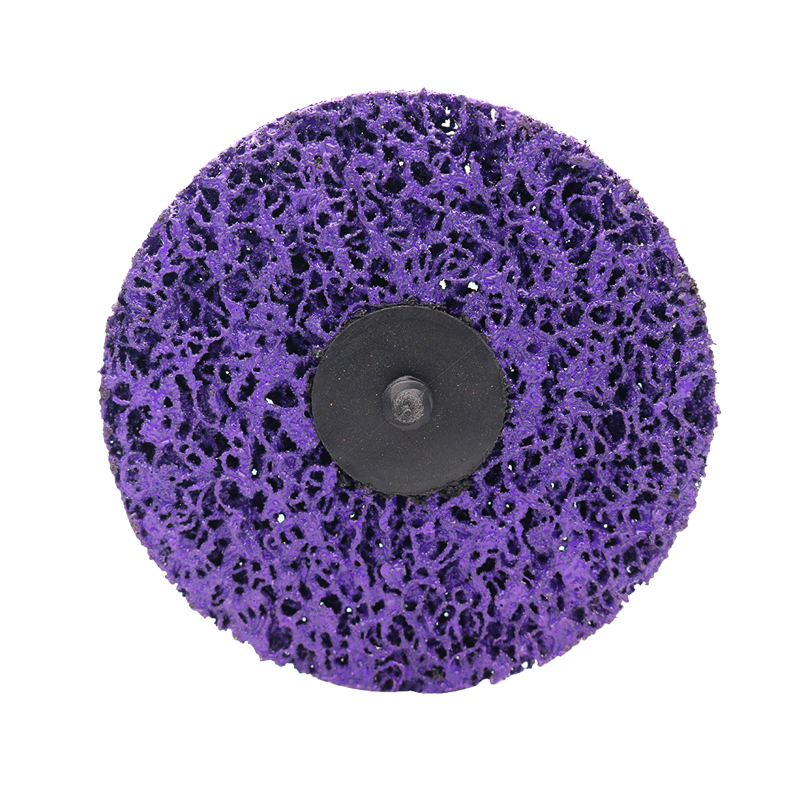
Another significant point of comparison between T27 and T29 flap discs is their speed and longevity. T27 discs tend to operate at lower speeds, which minimizes heat generation and prolongs the life of the disc. This aspect is particularly important in applications where overheating could lead to warping or damage to the workpiece.
In contrast, T29 discs can withstand higher speeds and are designed for more robust material removal without losing their effectiveness quickly. However, this comes with the caveat that excessive heat can lead to quicker wear on the flaps. Care must be taken to monitor the disc while in use to prevent overheating and ensure optimal performance.
Advantages and Limitations
Both T27 and T29 flap discs come with their respective advantages and limitations. The T27 flap discs are known for their excellent finish quality and less aggressive grinding, which makes them a popular choice among professionals looking for precision in their work. However, they may not be the best option for heavy-duty tasks that require rapid material removal.
On the other hand, T29 flap discs offer greater versatility and robustness in handling aggressive grinding requirements. Their angled design allows them to tackle more demanding applications efficiently, but they might compromise on finish quality compared to T27 discs. For applications where surface integrity is less critical, T29 might be the better choice.
Conclusion
In summary, the choice between T27 and T29 flap discs ultimately depends on the specific application at hand. For tasks that require precision finishing and a smooth surface, T27 flap discs are ideal. In contrast, for more aggressive grinding and material removal tasks, T29 flap discs provide superior performance. Understanding the distinct characteristics of each type will enable professionals to choose the right flap disc for their needs, thereby optimizing efficiency and achieving desirable outcomes in metal fabrication and finishing projects.
Post time:Dec - 25 - 2024