Understanding Flap Disc Technology and Its Applications
Flap discs are a versatile and efficient tool used primarily in grinding and finishing applications. They consist of multiple overlapping flaps made of abrasive material attached to a backing plate. This design allows for a greater surface area to come into contact with the material being worked on, which results in faster material removal and smoother finishes compared to traditional grinding discs. As a popular choice among professionals and DIY enthusiasts alike, flap discs have become a staple in various industries, including metalworking, woodworking, and construction.
The Advantages of Flap Discs
One of the key benefits of flap discs is their ability to provide consistent performance throughout their lifespan. Unlike conventional grinding wheels that become less effective as they wear down, flap discs maintain their cutting ability by gradually exposing fresh abrasive material as the flaps wear away. This characteristic not only improves efficiency but also enhances the quality of the finish, making flap discs ideal for tasks requiring precision.
Flap discs are also relatively lightweight and easy to handle, which reduces user fatigue during extended use. Additionally, they generate less heat compared to traditional grinding methods, which minimizes the risk of damaging the workpiece, particularly when working with heat-sensitive materials. Their design allows for effective grinding, blending, and finishing in one operation, saving time and effort for users.
Choosing the Right Flap Disc
When selecting a flap disc, several factors should be considered to ensure optimal performance for specific applications. The type of abrasive material is crucial, as it determines the disc's effectiveness and durability. Common abrasive materials include aluminum oxide, zirconia alumina, and ceramic. Aluminum oxide is suitable for general purpose grinding, while zirconia alumina offers superior durability and is ideal for tougher materials. Ceramic abrasives are typically used for high-performance applications, such as grinding stainless steel.
flap disc toolstation
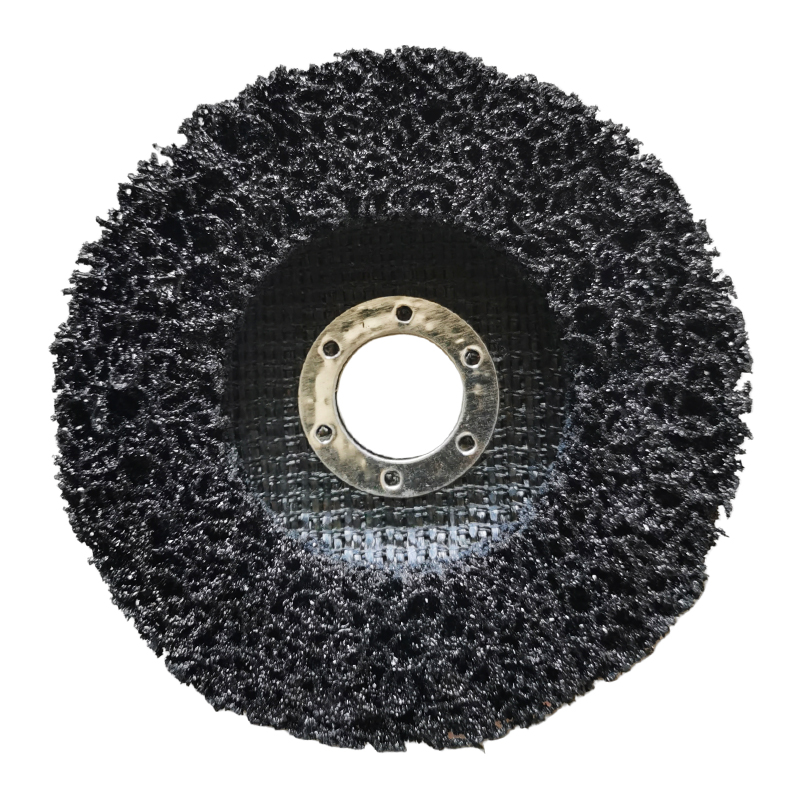
The shape and size of the flap disc should also match the surface area and contours of the workpiece. Flap discs are available in various sizes, often ranging from 4 to 7 inches in diameter, with different grit options that dictate the aggressiveness of the cut. Coarser grits are better for heavy material removal, while finer grits are preferable for achieving a smooth finish.
Additionally, the backing material of the flap disc plays a role in its performance. A fiberglass backing plate is common for standard applications, while a metal backing can offer additional stability for heavy-duty tasks. It is essential to choose a flap disc that aligns with the specific requirements of the project, including the material type and desired finish.
Safety Considerations
While flap discs are generally safe to use, it is important to follow proper safety precautions to minimize the risk of injury. Users should always wear appropriate personal protective equipment, such as gloves, goggles, and face shields, to shield against flying debris and sparks. Properly maintaining tools and equipment is also crucial; ensuring that flap discs are secured correctly and replaced when worn out can enhance safety and effectiveness.
Before starting any grinding task, users should familiarize themselves with the specific characteristics of the flap disc being used, including its maximum speed rating (RPM). Always operate within these limits to avoid accidents or equipment failure.
Conclusion
Flap discs are an invaluable asset in various industries, providing efficiency and versatility in grinding and finishing applications. Their unique design offers advantages over traditional grinding methods, including consistent performance and reduced heat generation. By considering factors such as abrasive material, size, shape, and safety precautions, users can maximize the effectiveness of flap discs in their projects. As technology continues to advance, flap discs will likely evolve, further enhancing their effectiveness and expanding their applications in the world of manufacturing and construction. Whether you're a seasoned professional or a weekend DIYer, understanding flap disc technology can significantly improve your work quality and efficiency.
Post time:Dec - 01 - 2024